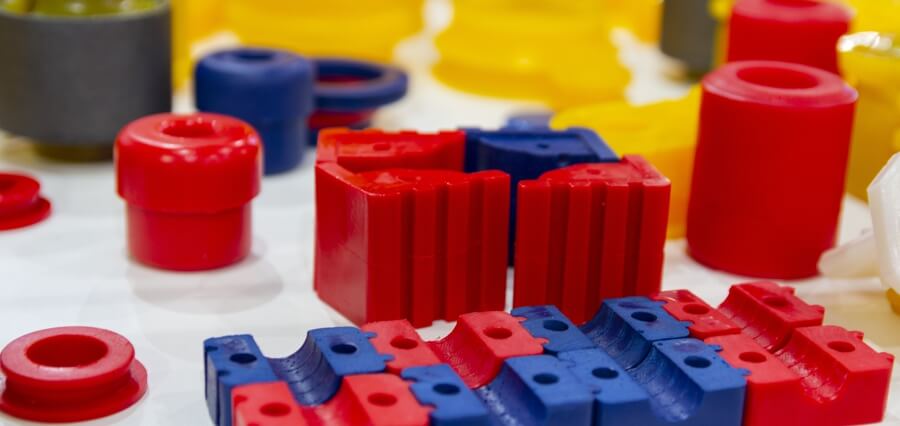
Urethane casting is an excellent alternative to plastic and rubber parts in most instances, but especially when used in the manufacturing process for heavy-duty equipment and parts. Polyurethane is the material choice for companies across the board—from gym equipment to construction and everything in between.
Commonly up against rubber, silicone, and plastic, polyurethane reigns supreme in the majority of instances because of its durability, customization options, tear strength, and corrosion resistance.
Leveraging urethane parts in the manufacturing process can help with product quality, cost, and lead times.
How Urethane Helps Automotive Manufacturing
Stated by custom urethane manufacturers, a prime example of how polyurethane is used in today’s manufacturing industry is the automotive industry’s parts and sealants.
The automotive industry uses urethane to produce parts because it has a higher tear strength and abrasion resistance compared to common alternatives like rubber or silicone. Polyurethane products can withstand contact with harsh materials such as road debris, coolant, oil, and grease.
It also has higher durometers than rubber, which means it will last longer without being torn apart over time.
Polyurethane is used for parts like motor mounts, but it’s also used in many other forms in the automotive industry. Urethane is used as a coating on the exterior of a car to protect it against scratches. It can also be used in liquid form as a sealant and in solid form for bumpers. Polyurethane can also absorb substantial shock and has high elasticity, making it safe and durable when used as bumpers on cars.
How Urethane Benefits the Oil and Gas Industry
Polyurethane is the manufacturing material of choice for the oil and gas industry because of its durability, heat resistance, and customizability.
This industry’s selling point is that polyurethane is weather and corrosion-resistant—making it ideal for mining, drilling, and marine environments. Durable parts and equipment are crucial in such a rugged environment, and polyurethane passes the toughest of tests.
Polyurethane can also be customized to whatever specs you need in a surprising number of applications. It can be made with a bright color, which helps to call out dangerous parts that people need to stay away from, and it can be molded into any size or shape.
Polyurethane is also used for refurbishing parts like pipeline rollers by giving them a protective coating. By using it as a coating, you can bring parts that were once worn and corroded back to life. This will save you money and time to replace parts as well.
How Urethane Is Helping the Gym Equipment Industry
One of the biggest investments in a gym is the equipment. Patrons will expect high-quality weights that don’t disintegrate in the middle of a workout, so investing in durable and superior materials up front will save time, money, and headaches.
Urethane is popularly used in the gym equipment industry because it is long-lasting, flexible, and customizable.
When used on weights, polyurethane can take rough handling in the gym. It doesn’t chip as easily as some of its alternatives, which keeps equipment looking new for as long as possible.
A common problem found with rubber in the workout industry is the smell it takes on overtime. Urethane exercise equipment does not give off the same foul odor that rubber equipment does, nor does it break apart as easily. Weights stink over time when they are made with cheap or recycled rubber because inferior products have chemicals and toxins in them. When rubber starts to break down and mixes with sweat, it creates a foul odor.
Rubber lasts between seven and twelve years, but tests have shown that polyurethane lasts 3-5 times longer than that.
Polyurethane also comes in handy in the gym equipment industry because it can be customized. You can choose the color, add a logo or texture, or choose the exact mold and shape you want for your equipment parts or weights.
The upfront costs for urethane solutions are worth the investment; in this case, you get what you pay for.
Picking Polyurethane for Your Manufacturing
While urethane may have a higher price tag up front, the benefits and cost-efficiencies over time are worth it. Polyurethane has a longer lifespan, which means you’ll spend less time and money replacing parts; it is durable enough to withstand the harshest conditions, and it’s customizable to meet any desires or requirements.
Picking polyurethane for your manufacturing processes gives you better parts and options, which allows your business to run smoothly and deliver on its promises.
Source URL.