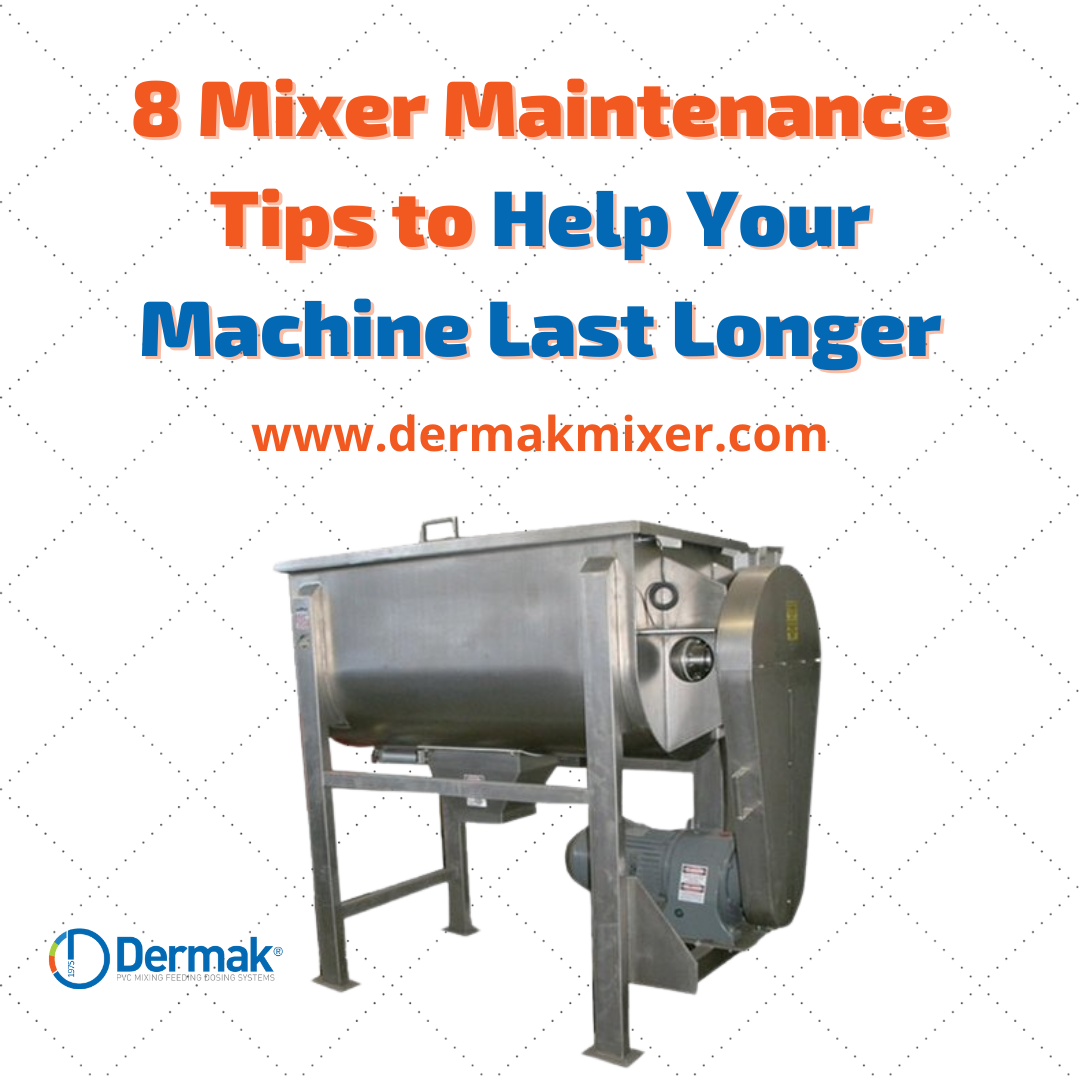
Ribbon blenders, paddle mixers, and other types of mixers are essential components of a food preparation system. These mixers can endure for decades if properly maintained. They may wear out prematurely if not properly maintained. Setting out time regularly to maintain your ingredient system mixer can save you hundreds of dollars in the long run. To extend the life of your ribbon blender, paddle mixer, or other mixers, keep these maintenance tips in mind.
Check Components for Lubrication
Checking lubricant levels and ensuring that the mixer’s moving parts are properly lubricated regularly will help your mixer last for years. This is one of the most important general mixer and ribbon blender maintenance tips to remember, and it’s also one of the simplest. Because some portions of the mixer, such as the driving components, account for a large portion of the overall cost, replacing them will be nearly as expensive as purchasing a new mixer. Particular attention should be paid to the lubrication around the drive, reducer, and shaft bearings. Once a month, set aside time to monitor these levels.
Maintain the Seal
Seals on the mixer and agitator retain ingredients in the mixer while also protecting the shaft from movement. If a seal is compromised, material may leak out or the shaft alignment may move. Mixer seals come in a variety of shapes and sizes, and the best mixer maintenance tips for each may vary depending on which type your machine has.
- Check the air pressure and quality to ensure that the air-tight seal is still in place.
- Stuffing Boxes: Examine the packing material for signs of wear or damage, and tighten or replace the stuffing boxes as needed.
- Lip-seals should be checked for leaks and damage regularly. If these mechanical seals are wearing out faster than usual, the seal material may be incompatible with the material being mixed, especially if you’re working with caustic or abrasive ingredients.
- Measure and adjust the spring compression to suit the manufacturer’s specifications for single seals. If the seal faces are worn out or the seal isn’t holding, replace them.
Monitor the Drive System Tension
One of the most important components of ribbon mixers and other mixers is the drive system. One of the most important ingredient system mixer maintenance tips is to keep the reducer, belt, or chain-and-sprocket mechanism properly oiled (see the first point above). It is critical to check the tensioning of the belt or chain regularly. If the belt or chain is too loose, it may slip and harm the sprocket or burn the belt. If the belt or chain is overly tight, it will prematurely wear out the bearings. Maintain the tension under the manufacturer’s instructions, and check it monthly to ensure it is proper.
Check the Discharge Gate Operation
Dust, dirt, powder, or foreign objects might become trapped in the discharge gate over time, preventing it from fully closing. When using limit switches, make sure the gate is entirely closed or open. During operation, keep an eye on the discharge gate to make sure it opens and closes properly. A material can remain in the mixer if the gate doesn’t fully open. The material will leak if the gate is not fully closed.
Protect the Mixer Tub
The mixer’s body is also an important aspect of maintaining a functioning ingredient system mixer. If the agitator is too close to the walls, whether you have a ribbon mixer, paddle mixer, or another type of mixer, the body of the machine can be harmed. Foreign items, such as metal shards or small rocks, might also cause the mixer to malfunction. The mixer blades may move too close or too far away from the tub as the shaft shifts over time. This will not only harm the mixer, but will also introduce metal particles into the mix, causing the mixing procedure to be disrupted. Keep in mind that the mixer was created to best match the needs of your ingredients—if the mixer’s components aren’t up to par, the mixer won’t work.
Clean Intervents
As components enter the mixer, intervents allow displaced air to escape. These intervents are prone to becoming clogged with dust. Clean them regularly to allow air to leave and your ingredients to flow freely into the mixer. Dry materials can form clouds of dust as air escapes through alternate exits if it can’t control through intervents. The presence of dust increases the risk of fire and explosion.
Inspect Electrical
Make sure there are no breaks in the electrical cords. Cords frequently get in the way as workers and machinery move throughout the building. A faulty electrical cord poses a safety danger to workers, putting them at risk of electric shock and fire. When a faulty electrical cord is combined with the preceding issue—clogged intervents causing dust clouds—two seemingly minor issues can quickly escalate into a major one, including a powder fire or explosion.
Using an electrical cord that is faulty might potentially cause damage to the machine’s interior components. Check the current absorbed by your ribbon blender or other mixer while it’s running to make sure it’s working properly. There could be damage somewhere in the electrical system or motor if it’s consuming too much or too little.
Check the Coefficient of Variation
Checking the coefficient of variation is one of the greatest ways to ensure that your mixer is in good operating order (CV). Take a few samples of your mix and send them to a lab once a year to have the CV checked. This may appear to be an unduly careful procedure, but it can assist prevent over- or under-mixing, as well as reveal if your mixer is malfunctioning.
If your process changes, such as automating a manual step, you may be able to shorten your mixing time to accommodate the increased speed. Checking the CV will reveal whether the revised mixing time is sufficient or if other adjustments are required.
These mixer maintenance measures may appear time-consuming when taken all together, but devoting a little time to each will make them much more doable. Consider the time, money, and effort required to replace or repair a mixer that has been neglected. When comparing the two, it will always be faster, cheaper, and easier to set aside maintenance time.