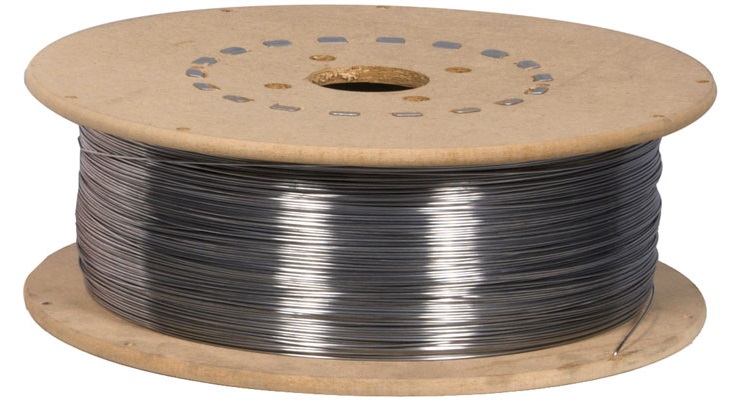
Whether you are a beginner or you are a professional welder, it is obvious that different projects and working environments require different kinds of welding processes. For instance, FCAW and MIG welding have quite different characteristics and it is important for welders to evaluate these differences to select the best welding process to use. Properties like the material thickness, shielding gas, settings of the voltage and even the feed speed of the wire need to be taken into account. Moreover procuring the best equipment as well as protective layers such DIFFCOR from Diffcor Suppliers is also important.
Welding is not a one-size-fits-all kind of process. Several variables tend to affect the overall usage of a particular process, especially the decision whether flux-cored wire from Flux Cored Wire Manufacturers should be used or solid wires. Understanding the basic differences between the two will help you in making the right decision.
Solid Wire
MIG welding uses electrodes made of solid wire for the filler material and it also requires a shielding gas. This gas is usually delivered from a gas battle that is under pressure. Steel wires are generally copper-plated as this helps in preventing oxidation and aids in the conduction of electricity. This also helps in increasing the overall durability of the contact tip.
The shielding gas is used for protecting the weld against any contamination that might be present in the surrounding area. The most common combination used is CO2 and argon. However, if the welding is outdoor it is advisable to use a windshield made from a DIFFCOR product supplied by Diffcor manufacturer as the gas coverage might get blown away by the wind.
Flux-Cored Wire
When it comes to flux-cored, there are two types - the one that is self shielding and other that is shield by gas. As the name suggests, gas-shielded wires require external shielding from gas and the slag formed is relatively easier to remove. Thus, if you welding a thicker metal or applications that aren’t in the right position, then you must make use of gas-shielded flux-cored wires.
On the other hand self-shielded flux-cored wires do not require any external shielding and hence they are more portable. Either of these can be easily purchased from any of the leading Flux Cored Wire Manufacturers depending on your requirements.
Factors to take into account when selecting flux cored wire
Apart from the stark differences mentioned above, the following are some factors that should also be taken into account when arriving at a final decision:
1. Appearance
The appearance of a weld is an important factor when it comes to the quality of the weld. When working on thinner materials, using solid wires is recommended as it tends to create a cleaner look. Using a gas-shielded flux-cored wire might result in spatter and can ruin the whole appearance. Consequently, many welders prefer solid wires when working with applications that are thin.
2. Location
If you are working outdoors then using self-shielded flux-cored wire is recommended. In windy locations, solid or even gas-shielded flux-cored wires are quite difficult to use and they can compromise the overall quality of the weld. With self-shielding wires the welder will not have to set up a windshield.
Conclusion
Apart from these, make sure to check the thickness of the application and the wires and make a choice accordingly. Do not make the mistake of trying to fit one type of wire across all your applications. For the right suggestions and for procuring welding equipment of high quality, you can contact Diffusion Engineers - leading welding equipment manufacturers in India.