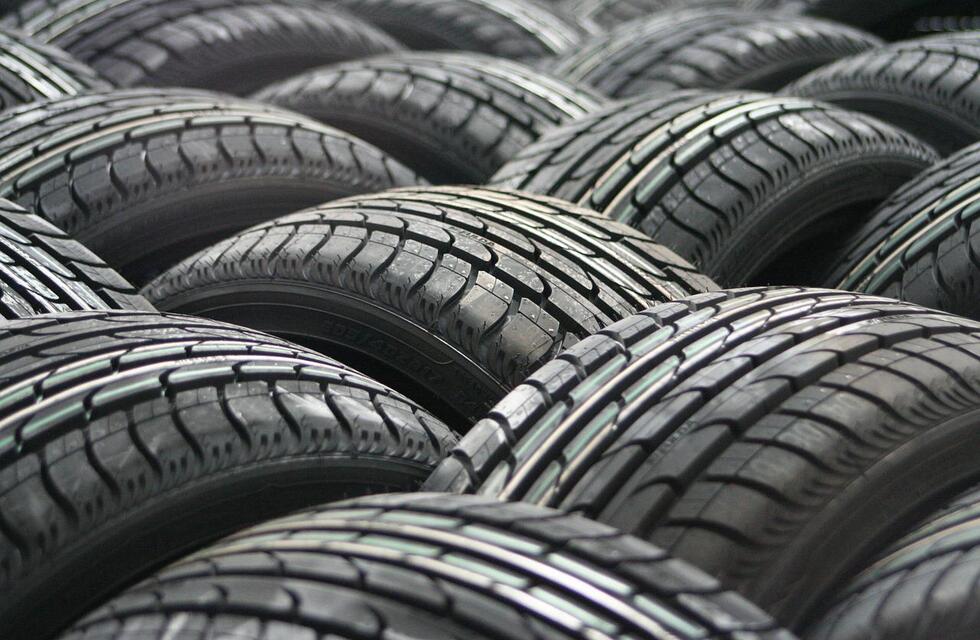
The tire manufacturing industry has very specific processes that make it particularly different from the others.
We refer to processes as specific as the mixture of different rubbers, extrusion, calendering and vulcanization.
In each of these processes, the material to be transported presents special conditions in terms of its texture, shape, composition and temperature. Therefore, the conveyor belt on which it will be transported in each of them must also be the most optimal for each situation.
Here is a brief description of each of them:
Rubber mix.
This is the initial process for the manufacture of the tire. And it consists of carrying out the mixture of the different elements that will make up the final product:
· Different types of rubbers. Typically, the four rubbers used to make tires are natural rubber, and the synthetic ones are styrene-butadiene rubber (SBR), polybutadiene rubber (BR), and butyl rubber.
· Carbon black, which is also a by-product of petroleum and which will give the tire resistance, in addition to the characteristic black color.
· Sulfur, which is the main element to allow vulcanization.
· And other products such as oils, antioxidants and anti-ozonants as well as healing agents and accelerators.
The mixing process is critical, it is carried out by subjecting the mixture to high temperatures that can reach up to 180ºC. In the last stage of the mixing process, temperatures must not exceed 110ºC or there will be a risk of abrasion.
The resulting mixture is a very viscous product with a high temperature. A conveyor belt is required, with a good grip, without adhesion and capable of working at temperatures above 100ºC.
Our recommendation is the use of the E30 Wave Embedded model, which with waves embedded in the belt surface itself meets both requirements. In addition, this arrangement of waves allows easy cleaning by means of a brushing system, manual or automatic, transversally in the direction of the wave.
This modular belt model, made of nylon, can withstand very high temperatures.
The resulting rubber sheet to be stored correctly without running the risk of adhering to each other is immersed in a tank with soapy water. Cooling is also carried out with this same process. It can now be stored in a swing panel unit.
In this area we need a transport belt that allows the drainage of the liquid to allow proper cooling as well as subsequent drying. For this phase we recommend the Flush Grid models, in their different steps, whose open surface will allow this correct drainage and aeration?
Extrusion
Generally speaking, extrusion is a process used to create objects with a defined cross section.
The material is passed through a die of a specific cross section, which will give it a certain shape.
The extrusion in the tire manufacturing process results in a perfect sheet that will be used to make the tread and sidewalls of the tire. This extrusion process is also carried out with the material at high temperatures.
For the transport of these hot sheets, obtained after extrusion, we recommend conveyor belts with a good grip capacity and that allow aeration to evacuate the heat from the rubber.
The most appropriate would be the Flush Grid and Open Grid models in their different steps. Made of polypropylene, they would withstand temperatures of up to 100ºC, enough for this process.
The calendered.
This process consists of the mechanical union, by means of pressure and heat, between the rubber and a framework of cloth, copper, wire or steel threads.
The calendering is carried out by means of a system of steel rollers, which rotate in opposite directions, and which are kept at a high temperature.
Rubber sheets are fed to rollers and pressed against the top and bottom of the cloth or steel cords.
A continuous sheet of composite material goes through several more rollers to guarantee a good bond between the parts.
The quality of a calendering process is measured by the thickness of the sheet, the space between the cords, the number of cords and the penetration of the rubber into the composite sheet.
The composite sheet is then cut into sizes, shapes and angles, depending on the contour of the tire to be manufactured. This process will give consistency to the resulting sheet, greater resistance and will also eliminate air or gas bubbles.
Vulcanization.
It is the process in which, and through heat, the sulfur that was incorporated in the initial mixture, is combined with the rubber mass, in order to obtain a harder and more resistant product.
In the vulcanization process, closely parallel linear polymers form bonds with each other. The end result is that the elastic rubber molecules stick together. This forms a rubber that, without losing its natural elasticity, is more stable, much more durable and resistant to chemical aggression. It also transforms the sticky surface of the material into a smoother, smoother surface that does not stick to metal or other items.
Vulcanization is an irreversible process that converts cured rubbers into thermostable materials, that is, they do not melt with heat.
In this process, it is advisable to transport the product using a plastic modular belt that is tolerant of high temperatures and has good behavior in the presence of corrosive agents.
For this purpose, we would also recommend belts with an open surface and made of polypropylene, a material that has good tolerance against a large number of corrosive elements.
Once the vulcanization and forming process has been completed, the tire can already be considered a finished product. We find processes that are much more common in any industry, such as verification and weighing, packaging (palletizing), storage and dispatch. From this moment on, the internal transport system does not require a demand beyond providing a reliable service and good treatment of the product. So for these last few steps we recommend the E30 and B50 series, closed surface, heavy duty, modular Flat Top belts.
What is Microwave Rubber Heating Technology?