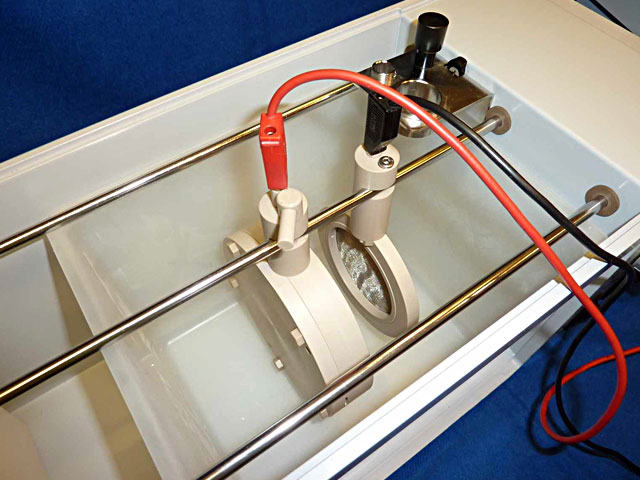
The future of Electroplating involves advancements in technology, sustainability, and environmental concerns. The development of nanotechnology and automation are improving the efficiency and quality of the electroplating process, while the use of electroplating in e-waste recycling is helping to address the problem of electronic waste. The adoption of eco-friendly electroplating solutions, such as non-toxic electrolytes and renewable energy sources, is reducing the environmental impact of the process. As the demand for high-quality, sustainable electroplating solutions continues.
Electroplating is a chemical process that involves the use of an electrolytic cell. An electrolytic cell consists of two electrodes, an anode, and a cathode. The anode is the metal that is being deposited, while the cathode is the surface to be coated. Both electrodes are placed in a solution containing ions of the metal being deposited. When a direct current (DC) is passed through the electrolytic cell, the anode dissolves, and the metal ions are attracted to the cathode, where they are reduced and deposited on the surface. The thickness of the deposit is controlled by the amount of time the current is applied.
Electroplating is used in a range of industries, including automotive, aerospace, electronics, and jewellery. It is also used for decorative purposes, such as coating statues and picture frames. In the automotive industry, electroplating is used to improve the appearance and corrosion resistance of parts, such as wheels, bumpers, and trim. Chrome plating is a common electroplating process used in the automotive industry. In the aerospace industry, electroplating is used to protect parts from corrosion and wear. Electroplating is also used to improve the thermal and electrical conductivity of parts.