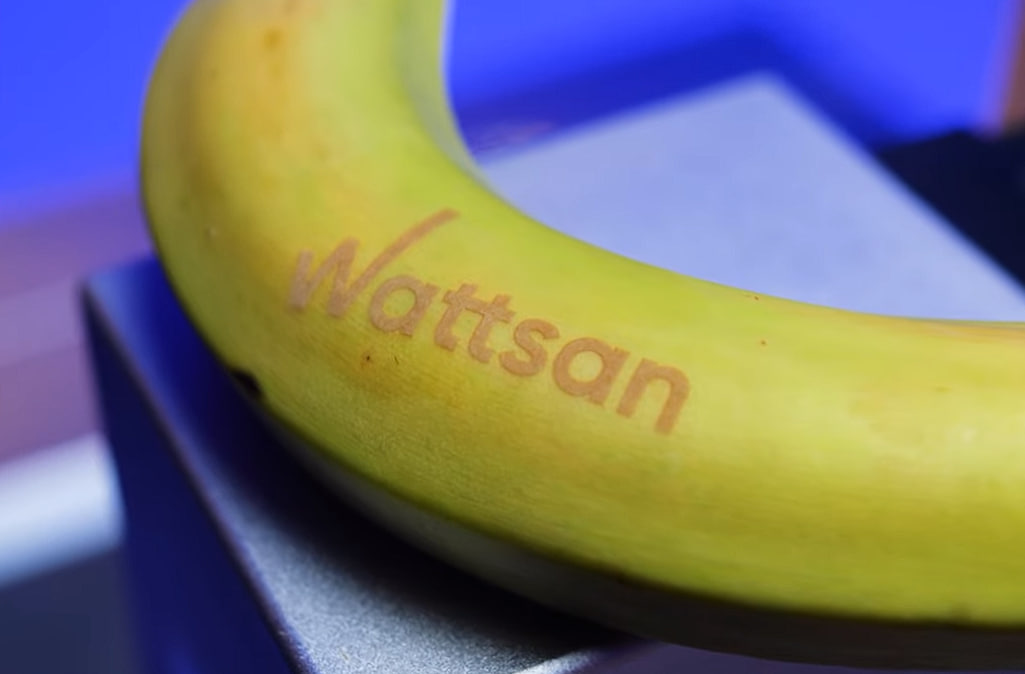
technology has been rapidly gaining popularity in recent years due to its advantages over traditional marking methods. Laser marking allows for precise and permanent marking on various materials: metals, plastics, ceramics and glass. It also offers high marking speeds and low maintenance costs, making it an ideal choice for industrial applications.
Due to the increasing demand for high-quality marking in production, laser marking technology has undergone significant changes in recent years. In this article we look at the modernization of laser marking in industry and its impact on production processes.
Laser marking methods
Laser marking technology has evolved from simple surface etching to advanced marking methods: annealing, ablation and foaming.
- Annealing, which uses a low-power laser to create a permanent mark on the surface of a material without damaging it.
- Ablation involves removing a thin layer of material to create a high-contrast mark.
- Foaming creates an embossed mark by heating the material to form bubbles which remain after cooling.
High-speed marking
The development of high-speed laser marking systems has greatly increased production efficiency. High-speed marking speeds up processing time, increases productivity and reduces production costs. This is particularly useful in industries such as automotive, aerospace and electronics, where high volume production is required.
3D marking
Advances in laser technology have also enabled the use of 3D laser marking, which marks complex shapes and curved surfaces. 3D marking is particularly useful in industries such as medical and aerospace, where complex designs and shapes require precise marking. 3D marking is accomplished by positioning the focus in the XYZ axes. To provide a three-dimensional scanning field, galvanoscanners with a dynamic Z-axis are used.
Integration with Industry 4.0
Laser marking technology has also been integrated into Industry 4.0* to provide real-time data tracking and quality control. This enables manufacturers to track production processes in real time, identify defects and quality issues and make adjustments to improve product quality. In addition, laser marking technology has been integrated with robotic systems to automate the marking process, reducing the need for human intervention and increasing efficiency.
* The Fourth Industrial Revolution
Environmental sustainability
Modernization of laser marking technology is also aimed at reducing the environmental impact. New laser systems consume less energy, produce less waste and have a longer service life. In addition, laser marking technology has enabled the use of environmentally friendly marking materials such as water-based inks and coatings.
Industry applications
Laser marking technology has a wide range of industrial applications:
- product marking,
- Serial numbering,
- part identification,
- product marking, part identification and branding.
In addition, laser marking is widely used in the medical industry for marking surgical instruments and implants, as well as in the aerospace industry for marking components and parts.
Future Trends
The future of laser marking technology is focused on improving accuracy, speed and integration with Industry 4.0. In addition, advances in laser technology are enabling new applications such as laser engraving on glass and ceramics.
Another trend in the modernization of laser marking is the move toward automation and integration with other manufacturing processes. Many laser marking systems now include robotic arms or other automated mechanisms that can quickly and efficiently mark parts as they move along the production line.
Industry 4.0 and the Internet are also contributing to the modernization of laser marking: many laser marking systems are now connected to centralized networks that allow real-time tracking of production and quality data. This allows for better control of the production process, as well as the rapid identification and correction of any quality problems that arise.
The use of laser marking in medical device manufacturing is also becoming increasingly important, as it allows for precise marking of small, fragile parts and components. Laser marking is also used to protect against counterfeiting, ensuring the authenticity and safe use of medical devices.
Conclusion
Modernization of laser marking technology has had a significant impact on production processes, enabling high-speed, accurate and consistent marking. Integration of laser marking technology with Industry 4.0 has enabled real-time data tracking and quality control, improving product quality and reducing costs. With continuous improvements in laser technology, the future of laser marking is promising, offering even more opportunities for industrial applications.