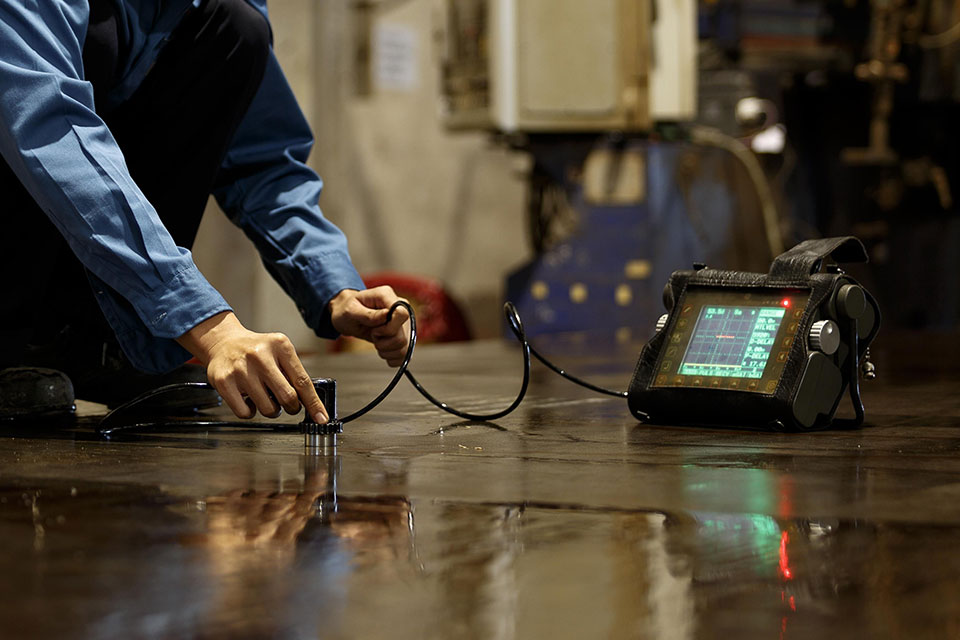
Non-destructive testing (NDT) serves as a powerful tool for quality assurance by identifying hidden flaws and ensuring the integrity of materials and components without causing damage. This enables manufacturers to deliver products of the highest quality, meeting industry standards and customer expectations. NDT techniques, such as ultrasonic testing (UT), radiographic testing (RT), magnetic particle testing (MT), and liquid penetrant testing (PT), are employed to inspect materials and detect defects that may compromise quality. These methods enable the detection of internal flaws, cracks, discontinuities, or material inconsistencies that might not be visible to the naked eye. By implementing NDT in the manufacturing process, manufacturers can ensure that their products meet required specifications, such as dimensional accuracy, structural soundness, and material composition. This helps prevent the production of faulty or substandard products, reducing the risk of product failures, recalls, or safety hazards.
Non-destructive testing techniques provide valuable information for quality control, enabling manufacturers to make informed decisions about product acceptance, rejection, or necessary corrective actions. By identifying and addressing hidden flaws early in the manufacturing process, NDT supports the production of reliable, durable, and safe products. Ultimately, NDT for quality assurance contributes to customer satisfaction, brand reputation, and compliance with industry regulations. It provides manufacturers with the confidence that their products have undergone rigorous testing and inspection, defying hidden flaws and ensuring the delivery of high-quality goods to the market.
Read More: https://blogconnoisseur.blogspot.com/2023/07/unveiling-unseen-exploring-non.html