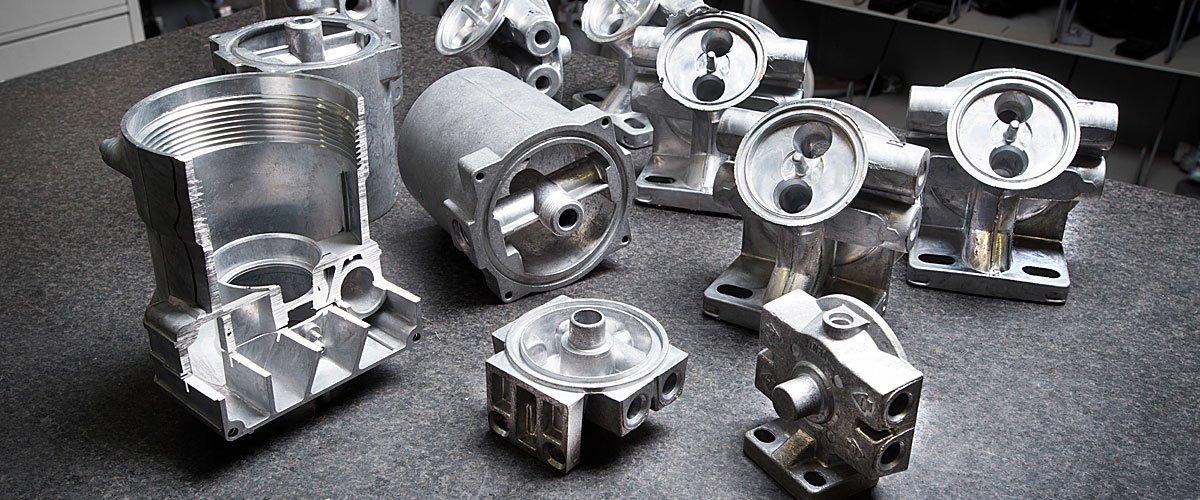
Aluminum casting is a versatile manufacturing process that involves pouring molten aluminum into molds to create complex metal components. From automotive parts to industrial machinery, aluminum castings play a pivotal role in many industries due to their strength, durability and lightweight properties..
The Aluminum Casting Process
The aluminum casting process involves five basic steps:
1. Pattern Making: Wood or resin patterns are created based on the design specifications. These patterns are used to create sand molds.
2. Mold Making: Sand molds are prepared from the patterns using green sand, which is a mixture of sand, clay and chemicals. The molds are two-piece boxes with shaped cavities.
3. Melting and Pouring: Aluminum ingots are melted in furnaces and then poured into the sand molds at temperatures between 650-750 °C.
4. Cooling and Solidification: The molten aluminum allowed to cool and solidify in the molds, acquiring the shape of the cavities.
5. Finishing: The castings are separated from the sand molds. Then operations like trimming, cleaning, fettling and heat treatment are carried out to get finish machined components.
Advantages of Aluminum Casting
Complex Parts Production: Due to the lost-wax casting process, aluminum castings can produce very intricate designs with complex internal passages that would be impossible to manufacture with other methods. This allows for parts consolidation.
Material and Cost Savings: Compared to machining metal billets, aluminum casting uses 30-60% less material while producing near-net shape components. This lowers overall production costs.
Dimensional Stability: Aluminum castings maintain their dimensions very well during production and over the life of the part. They do not require further processing steps like welding or riveting.
Lightweighting: With a density of only one-third that of steel or cast iron, aluminum castings can significantly reduce weight. This improves fuel efficiency in automotive and aerospace applications.
Design Flexibility: Unlike forging or extrusion processes, castings allow for design iterations and variations without the need for new dies or tooling. Design optimization is very easy.
Corrosion Resistance Applications
Marine Components: Due to its inherent corrosion resistance, aluminum is widely used for marine components such as outboard motor parts, propellers and fittings. Aluminum castings provide strength and durability without sacrificing alloy composition.
Industrial Equipment: Pumps, valves, pipes and hydraulic cylinders benefit from aluminum casting’s resistance to seawater, chemicals and harsh environmental conditions. This extends product lifecycles.
Waterworks: Critical applications like water conveyance infrastructure, drainage covers and plumbing parts utilize aluminum’s lightweight and anticorrosion characteristics.
Automotive and Transportation
Cylinder Heads: Automakers extensively use aluminum castings for cylinder heads due to their high specific stiffness. This improves engine thermal efficiency.
Transmission Cases: Complex transmission cases along with housings are readily cast in aluminum to reduce rotating assembly weight and boost fuel economy.
Wheels: Strong yet lightweight aluminum wheels help lower curb weights and rolling resistance in passenger vehicles as well as trucks and buses.
Rail Components: Signaling hardware, couplers and bogie frames used in trains leverage aluminum castings to minimize network loads and extend rail component lifetimes.
Aerospace Industry Adoption
Aircraft Structures: Major airframers design wings, fuselages and landing gear from aluminum castings to realize structural strength gains compared to traditional aluminum mill products.
Engine Components: Critical rotating parts like turbine housings, compressor cases and nozzle guides are cast due to aluminum’s high strength-to-weight and fatigue resistance.
Space Hardware: Launch vehicle and satellite hardware depend on lightweight aluminum casting solutions while maintaining requisite mechanical properties.
Defense Applications
Armored Vehicles: Parts for tanks, APCs and artillery systems use cast aluminum suspension arms, power packs and engine modules to improve military vehicles’ power-to-weight ratios and maneuverability.
Small Arms: Firearms manufacturing employs cast aluminum alloys for accessories such as charging handles, rail mounting systems and modular assemblies.
Ship Construction: Extruded or cast deck fittings, rigging points and hatchways meet naval corrosion and durability standards while slashing shipboard weight burdens.
Industrial Application Scope
With all of aluminum casting’s inherent benefits, it enjoys wide usage in factory equipment manufacturing for conveyors, automated assembly lines, material handling systems, process piping and plant utilities.
Critical infrastructure sectors related to energy, water resources and construction draw extensively from aluminum casting solutions for switchgear housings, valve bodies, transmission hardware, pumping components and prefabricated structural elements.
Aluminum as a Versatile and Sustainable Material
Despite aluminum’s high initial material and processing costs relative to steels, polymers or composite materials, its performance advantages, design flexibility and lengthy lifetime valuation make it a smart choice economically as well as environmentally.
Being fully recyclable without loss of properties, aluminum conserves energy, cuts carbon impact and supports circular economies. Combined with casting’s design optimization and near-net shape manufacturing, it sets a sustainable production standard.
As global decarbonization becomes imperative, aluminum casting’s lightweight yet robust attributes have never been in higher demand across industries. With its inherent environmental sustainability and substantial impacts on fuel efficiency, aluminum is perfectly positioned to play a leading role in a future of green manufacturing and mobility.
In summary, aluminum casting stands out as a versatile and sustainable metal forming process which will continue enabling innovative product development and optimized designs for many years ahead.
Get more insights on this topic: https://www.ukwebwire.com/aluminum-casting-is-one-of-the-most-widely-used-casting-processes/
Explore more information on this topic, Please visit: https://coolbio.org/system-on-a-chip-soc-the-future-of-electronics/