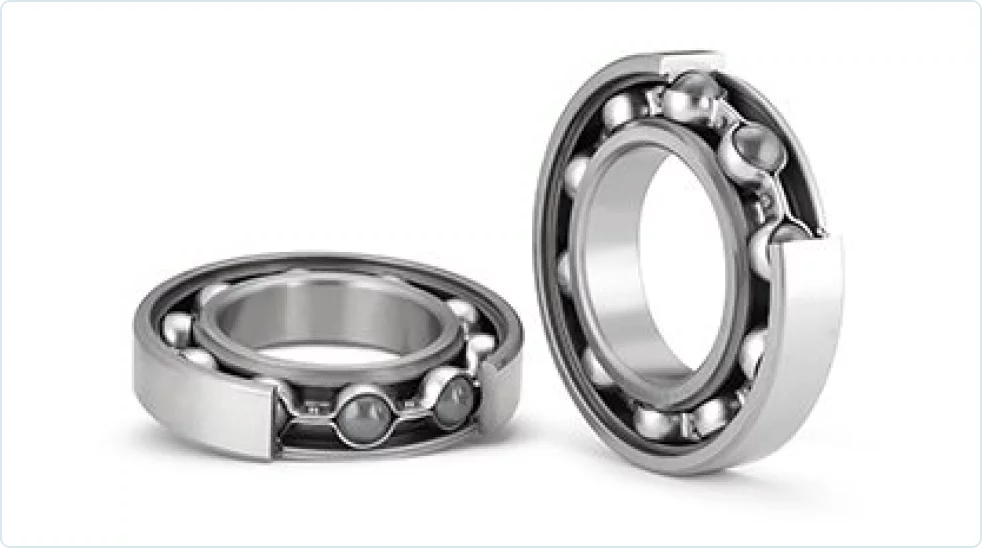
High-temperature bearings are designed to withstand extreme thermal conditions while maintaining their structural integrity and performance. These bearings are essential for ensuring the reliable operation in extreme and demanding applications where conventional bearings would fail prematurely.
Applications of High-Temperature Bearings:
- Jet engines and gas turbines operate at extremely high temperatures and rotational speeds, necessitating the use of high-temperature bearings for critical components like turbine shafts and compressor bearings.
- The intense heat within furnaces and kilns requires bearings that can withstand continuous exposure to high temperatures while ensuring smooth operation and reliable performance.
- High-speed machining processes generate significant frictional heat, demanding bearings that can maintain their dimensional stability and lubrication properties under such conditions.
- The corrosive environments and high temperatures present in chemical processing applications necessitate the use of high-temperature bearings with specialized materials and lubricants.
This article considers material selection, comparing high-temperature bearing materials and the practical use of full ceramic, and hybrid ceramic/steel and other types of steel used for high-temperature bearings.
Types of High-Temperature Bearings
When conventional bearings reach their thermal limits, high-temperature Full or Hybrid ceramic bearings are available. Depending upon load and speed requirements either type can be selected offering exceptional performance and longevity in extreme environments. High Temperature bearings may require a special clearance, ball type, lubrication and race material. Many distributors like Pacific International Bearing Inc can offer bearings from stock to meet your needs.Full Ceramic bearings utilize ceramic rolling elements and races manufactured from nitride (Si3N4) or zirconia (ZrO2).
Advantages:
- Heat Resistance
Ceramic materials boast exceptional thermal stability, allowing ceramic bearings to withstand temperatures of up to 1600°C, far exceeding the capabilities of bearing steel. This increased level of heat resistance makes ceramic bearings ideal for applications in furnaces, kilns, and other high-temperature environments. Please keep in mind full ceramic bearings do not have the load capacity of steel bearings and must be sized properly before using them.
- Minimal Thermal Expansion
Unlike steel, which expands significantly with increasing temperature, ceramic materials exhibit minimal thermal expansion. This characteristic ensures consistent performance across a wide temperature range, reducing the risk of seizure and dimensional deformation.
- Inherent Corrosion Resistance
Ceramic materials are naturally resistant to corrosion, making them highly suitable for operation in harsh environments where exposure to chemicals or moisture would quickly degrade conventional bearings. This property is particularly valuable in chemical processing and other corrosive applications.
- Hardness and Wear Resistance
The inherent hardness and wear resistance of ceramic materials contribute to extended bearing life and reduce maintenance requirements.
While high-temperature ceramic ball bearings offer significant advantages, it’s important to consider their higher cost compared to conventional bearings. Additionally, ceramic materials can be more brittle than steel, requiring careful handling and installation to prevent damage.
Also full ceramic bearings offer about 30%-50% of the load rating of standard steel bearings. You must be aware of the reduced load ratings of full ceramic bearings versus Hybrid ceramic ball bearings which meet or exceed steel ball bearing speeds but are about equal for load ratings.Please contact Pacific International Bearing Sales Inc at info@pibsales.com for further assistance.
Full Ceramic and Hybrid bearings perform well in extreme environments like cleanrooms, vacuum, high temperature and corrosive conditions. Be sure to check with Pacific International Bearing to size the bearing for correct loads and speed ratings. Contact us at info@pibsales.com.
Clean Environments
Bearings made of 440C bearing stainless steel are suitable for operation in clean environments when the preservative oils are removed. Additionally replacing the steel balls with ceramic balls enhances performance and longevity. Adding grease or oil is possible as long as it has low particle emissions. Many times a small amount of fluorinated oil can be applied to the bearing for safe use in clean environments.
Vacuum Environments
For a vacuum environment we suggest the outer/inner rings and balls are made of martensitic stainless steel. For corrosion resistance we suggest precipitation hardening steel be used. You should specify high speed tool steel for the best heat resistance. As in most Vacuum applications cleanliness is important so we suggest using polymeric lubricants or fluorinated grease.
High Temperature Environments
Pacific International Bearing offers Hybrid Ceramic bearings for many high temperature applications. The inner and outer ring material can be made from 440C stainless or for higher temperature high speed tool steel. Bearings with steel rings and ceramic balls are Hybrid bearings and are often of higher precision than standard. When selecting a lubricant the temperature of the application is your guide:
- Up to 200 degrees Celsius, fluorinated grease should be considered
- Over 200 degrees Celsius, layer lattice material should be considered
- Over 500 degrees Celsius, an unlubricated full ceramic bearing should be considered
SKF Single Row Deep Groove Ball Bearings in High-Temperature Applications
SKF offers a range of single row deep groove ball bearings specifically designed to withstand high temperatures. These bearings are engineered to deliver increased reliability, reduced complexity, and decreased environmental impact in operating temperatures up to 350°C.
These bearings are particularly well-suited for applications in kiln trucks, roller hearth furnaces, and bakeries, where high temperatures are common. The robust design and specialized materials used in SKF high-temperature bearings ensure reliable performance and extended service life, even under demanding thermal conditions.
Key Features and Benefits:
- SKF high-temperature bearings are designed to operate reliably in temperatures up to 350°C, making them suitable for a wide range of demanding applications.
- These bearings adhere to ISO dimensions, allowing for easy interchangeability with standard grease-lubricated bearings and simplifying the design and implementation process.
- SKF high-temperature bearings are designed to be robust and reliable, reducing the need for complex lubrication systems and maintenance procedures.
- By utilizing specialized materials and optimized designs, SKF high-temperature bearings contribute to reduced energy consumption and environmental impact.
Specific Examples:
SKF Explorer High-Temperature Bearings.This series of bearings features optimized internal geometry and special heat-stabilized steel, making them suitable for high-speed applications and temperatures up to 350°C.
SKF Food Line High-Temperature Bearings. These bearings are specifically designed for the food and beverage industry, featuring food-grade lubricants and materials that comply with strict hygiene regulations.
Conclusion
Selecting the best high-temperature bearing for your specific application requires careful consideration of various factors. Understanding operating temperature, load, speed and lubrication requirements helps in selecting the best bearing options. Hybrid bearings and Full ceramic bearings offer the best options for use in special environments. Our hope from this article is that Engineers can make informed decisions to ensure reliable and efficient bearing operation in even the most demanding environments.
Please visit www.pibsales.com to place an order online or call us to discuss.