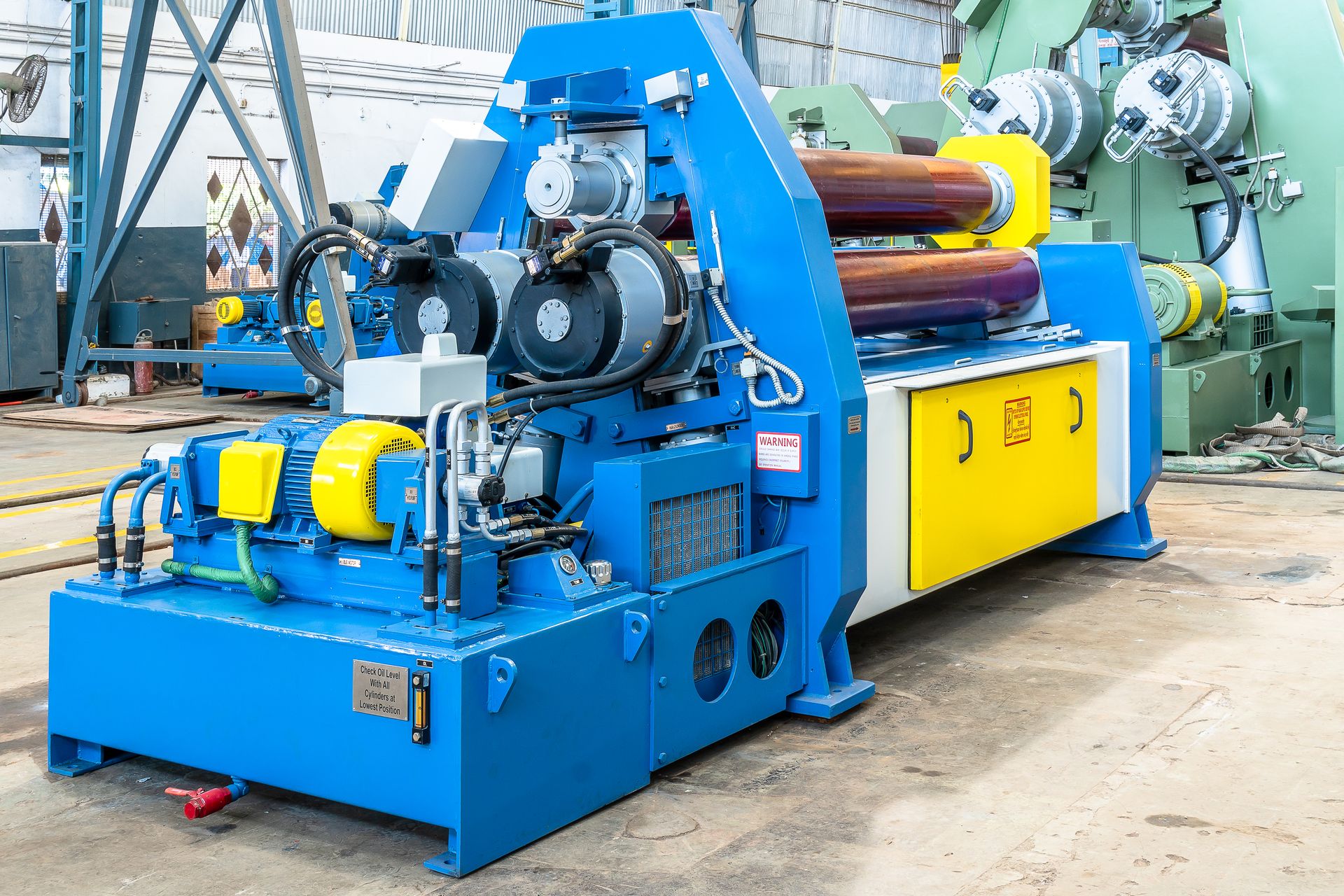
Are you looking to improve your skills in operating plate bending machines? If you’re a metal manufacturer, understanding the nuances of using these machines can significantly boost your productivity and ensure the quality of your products. In this article, we’ll explore the top techniques to master the operation of plate bending machines, including hydraulic variants and cone rolling machines. We’ll also touch on the essential aspects to consider when assessing plate bending machine prices. Let’s dive in!
Introduction
Plate bending machines are crucial in the metal manufacturing industry. Whether you're dealing with simple bends or complex shapes, mastering the operation of these machines is key to achieving high-quality results efficiently. In this guide, we'll share the top seven techniques to enhance your plate bending machine operation skills. We’ll also provide insights into the hydraulic plate bending machine, cone rolling machine, and factors affecting plate bending machine prices.
Understanding Plate Bending Machines
Before diving into the techniques, it's essential to understand what a plate bending machine is. These machines are designed to bend various types of metal plates into different shapes and angles. They come in several types, including mechanical, hydraulic, and CNC-operated machines. Hydraulic plate bending machines, for instance, use hydraulic pressure to perform precise and powerful bends.
1. Choose the Right Machine for the Job
Selecting the appropriate plate bending machine is the first step towards effective operation. The choice depends on the type of material, thickness, and desired shape. For instance, hydraulic plate bending machines are ideal for thicker and tougher materials due to their robust power and precision.
Factors to Consider:
- Material Type: Different materials require different bending forces and techniques.
- Thickness: Thicker plates need more powerful machines like hydraulic plate bending machines.
- Desired Shape: For complex shapes like cones, a cone rolling machine is more suitable.
Choosing the right machine can save time, reduce material waste, and improve the quality of your bends.
2. Proper Material Preparation
Material preparation is crucial for achieving accurate bends. This step involves ensuring the metal plate is clean, free of rust, and cut to the correct size. Proper preparation minimizes the risk of defects and ensures consistent results.
Steps for Effective Material Preparation:
- Cleaning: Remove any rust, oil, or debris from the plate.
- Cutting: Ensure the plate is cut to the correct dimensions with smooth edges.
- Inspection: Check for any imperfections that could affect the bending process.
Proper preparation sets the stage for smooth and accurate bending operations.
3. Accurate Machine Setup
Setting up your plate bending machine correctly is essential for achieving precise bends. This involves adjusting the machine parameters to match the specifications of the task at hand.
Key Setup Steps:
- Calibration: Ensure the machine is calibrated according to the material thickness and type.
- Roll Alignment: Make sure the rolls are properly aligned to avoid uneven bends.
- Pressure Settings: Adjust the pressure settings for hydraulic plate bending machines to match the material requirements.
An accurate setup is like laying a solid foundation; it ensures the rest of the process runs smoothly.
4. Safety First
Safety should always be a top priority when operating plate bending machines. These machines can be dangerous if not used correctly.
Safety Tips:
- Wear Protective Gear: Always wear gloves, goggles, and other protective gear.
- Follow Guidelines: Adhere to the machine’s operational guidelines and safety protocols.
- Regular Inspections: Frequently inspect the machine for any signs of wear or malfunction.
Remember, a safe working environment not only protects you but also enhances productivity.
5. Mastering the Bending Process
Understanding the bending process is crucial for achieving accurate results. This involves knowing the right techniques and adjustments to make during the bending operation.
Tips for Effective Bending:
- Gradual Bending: For thicker materials, perform the bend in multiple passes to avoid over-stressing the material.
- Consistent Pressure: Ensure consistent pressure throughout the bending process, especially with hydraulic plate bending machines.
- Monitor the Bend: Continuously monitor the bend to ensure it matches the desired angle and shape.
Mastering the bending process requires practice and a keen eye for detail.
6. Regular Maintenance
Regular maintenance of your plate bending machine ensures its longevity and optimal performance. Neglecting maintenance can lead to machine failures and production downtime.
Maintenance Checklist:
- Lubrication: Regularly lubricate moving parts to reduce friction and wear.
- Inspection: Perform routine inspections to identify and fix any issues early.
- Cleaning: Keep the machine clean to prevent debris from affecting its operation
A well-maintained machine runs more efficiently and produces higher-quality bends.
7. Continuous Learning and Training
The field of metal manufacturing is always evolving, and staying updated with the latest techniques and technologies is crucial.
Ways to Stay Updated:
- Training Programs: Enroll in training programs offered by machine manufacturers or industry associations.
- Workshops: Attend workshops and seminars to learn about new developments and best practices.
- Online Resources: Utilize online resources and forums to stay informed about the latest trends and tips.
Continuous learning ensures you remain proficient and can leverage new advancements to improve your operations.
Assessing Plate Bending Machine Prices
Understanding the factors that affect plate bending machine prices is essential for making an informed purchase decision. Prices can vary widely based on several factors.
Factors Influencing Prices:
- Machine Type: Hydraulic plate bending machines typically cost more due to their advanced capabilities.
- Size and Capacity: Larger machines with higher capacity command higher prices.
- Brand and Quality: Established brands like Himalaya Machinery, which is a heavy engineering company in India offer reliable and durable machines, often at a premium price.
Investing in a quality machine may have a higher upfront cost but can lead to savings in the long run due to reduced maintenance and higher productivity.
Conclusion
Mastering the operation of plate bending machines involves a combination of choosing the right equipment, proper preparation, accurate setup, and ongoing learning. By following these top seven techniques, you can enhance your bending operations, improve product quality, and increase your overall efficiency. Remember, safety and maintenance are key to sustaining optimal machine performance.
FAQs
1. What is the primary advantage of using a hydraulic plate bending machine?
The primary advantage of using a hydraulic plate bending machine is its ability to handle thicker and tougher materials with precision and ease.
2. How often should I perform maintenance on my plate bending machine?
Regular maintenance should be performed at least monthly, with daily checks for lubrication and cleanliness to ensure optimal performance.
3. What safety precautions should I take when operating a plate bending machine?
Always wear protective gear, follow the machine's operational guidelines, and conduct regular inspections to ensure a safe working environment.
4. How can I choose the right plate bending machine for my needs?
Consider the material type, thickness, and desired shape. Hydraulic machines are ideal for thicker materials, while cone rolling machines are suited for creating conical shapes.
5. What factors affect the price of a plate bending machine?
The price is influenced by the machine type, size, capacity, brand, and overall quality. Established brands like Himalaya Machinery may offer higher quality at a premium price.