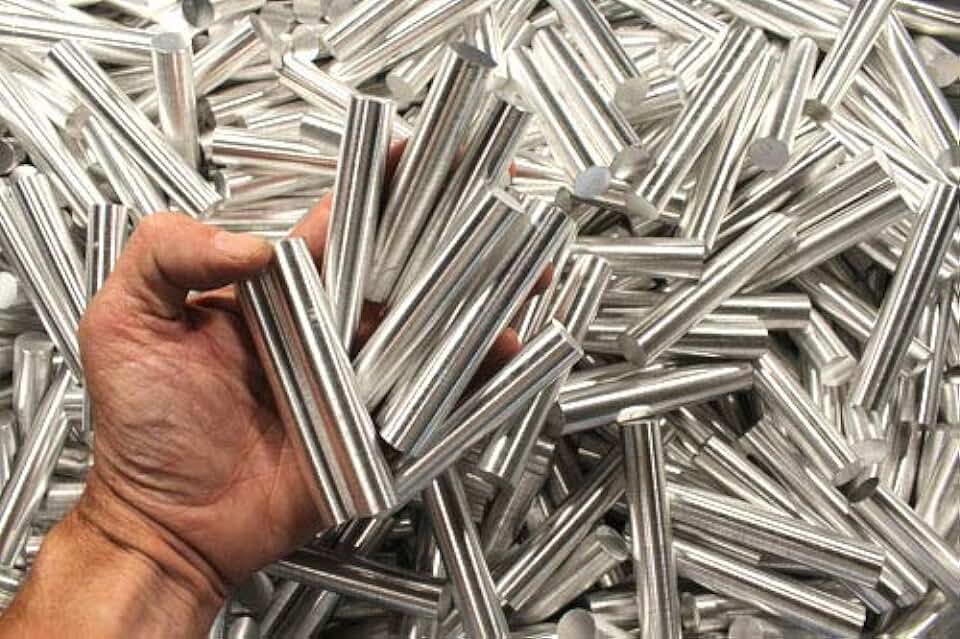
Magnesium is a silvery-white metal that is light in weight and fire-resistant. It has an atomic number of 12 and a melting point of 650°C. Magnesium has a density of 1.738 g/cm3 which is much less than other metals such as aluminum, iron and copper. This lightweight property has made magnesium attractive for various applications where weight savings are important. Chemically, magnesium is quite reactive. It readily catches fire in air and burns with a brilliant white flame. It reacts with oxygen at high temperatures to form magnesium oxide. It also reacts with water at high temperatures to form magnesium hydroxide and hydrogen gas. These reactions make magnesium a challenging material to work with and require protective atmospheres during processing operations.
Production and Reserves of Magnesium Metal
While magnesium ranks eighth among elements in abundance on Earth, it is not commonly found in nature in its pure form. The major commercial source of magnesium is dolomite ore which contains both magnesium and calcium carbonates. Other magnesium-bearing ores include magnesite, carnallite and serpentine. Globally, the annual production capacity of magnesium is around 1 million metric tons. Major Magnesium Metal producing countries are China, Russia, Israel, Ukraine, and Kazakhstan. China leads the world production and accounts for over 50% of global magnesium output. Sea water also contains large reserves of magnesium but its extraction from seawater is not economically viable currently. Total identified magnesium reserves are estimated to be enough to meet demand for at least 100 years at current production rates.
Alloying and Processing of Magnesium
Pure magnesium is rarely used in its unalloyed form due to low strength and ductility. Various alloying additions such as aluminum, zinc, manganese and rare earth elements are commonly used to enhance the mechanical properties of magnesium. Magnesium-aluminum alloys contain 1-5% aluminum and exhibit higher strength compared to pure magnesium. Magnesium-zinc alloys are used where corrosion resistance is important. Powder metallurgy and die-casting are commonly used manufacturing processes for fabrication of magnesium components. Powder metallurgy allows producing near-net shape parts directly from metal powders. Die-casting offers the ability to shape liquid magnesium alloys into complex geometries at high production rates. Other fabrication techniques include sand casting, thixoforming and extrusion.
Applications in Aerospace Industry
With its light weight and high specific strength, magnesium finds widespread use in the aerospace industry for weight savings. Magnesium alloy components find application in structural assemblies, engine components and airframes of commercial and military aircraft. Some examples include wing and fuselage skins, landing gear components, air ducts, frames and cases. Weight reduction through use of magnesium translates to lower fuel consumption and reduced carbon emissions. Helicopter transmission housings and engine frames also utilize magnesium alloys. Spacecraft structures and launch vehicles employ magnesium due to its reduced mass characteristics. Applications in missiles and surveillance drones realize performance benefits from low part weights. Overall, the aerospace sector accounts for major portion of global magnesium demand and usage.
Usage in Automotive Sector
Magnesium alloy components are increasingly being adopted in passenger cars and commercial vehicles to reduce weight and improve fuel efficiency. Current automotive applications include interior and exterior body panels, steering wheels, seat frames and wheel covers. Replacement of cast iron or steel components with magnesium alloys can result in part weight savings exceeding 50% in some cases. This significantly lowers the curb weight and improves acceleration and braking performance of vehicles. Reduced weight also enhances handling, ride quality and driving range of electric vehicles. Magnesium intake manifolds, oil pans and transmission cases also help reduce overall vehicle mass. Many leading automakers have augmented use of magnesium alloys to meet corporate average fuel economy (CAFE) norms.
Other Industrial Applications
Besides aerospace and automotive, magnesium finds diverse usage in other industries as well. Electronics applications involve laptop and computer housings, cellular phone frames and camera bodies that employ lightweight magnesium alloys. Power tools utilize magnesium die-cast components for handle housings. Sports equipment manufacturers produce magnesium alloy rackets, bicycle frames and golf club heads. Defense equipment including small arms, artillery shells and bullet-proof armors integrate magnesium for strength-to-weight benefits.
Marine products such as outboard motor frames, speed boat hulls and outdrives employ die-cast magnesium alloys. Medical implants like bone screws, orthopedic joints, dental frames and surgical instruments harness magnesium's biocompatibility. Miscellaneous uses also encompass flashlights, camera flashes and desktop accessories where low mass is preferred. Overall, magnesium alloys constitute an important lightweight structural material across diverse industrial domains due to excellent strength-density ratio.
Get more insights on Magnesium Metal
About Author:
Money Singh is a seasoned content writer with over four years of experience in the market research sector. Her expertise spans various industries, including food and beverages, biotechnology, chemical and materials, defense and aerospace, consumer goods, etc. (https://www.linkedin.com/in/money-singh-590844163)