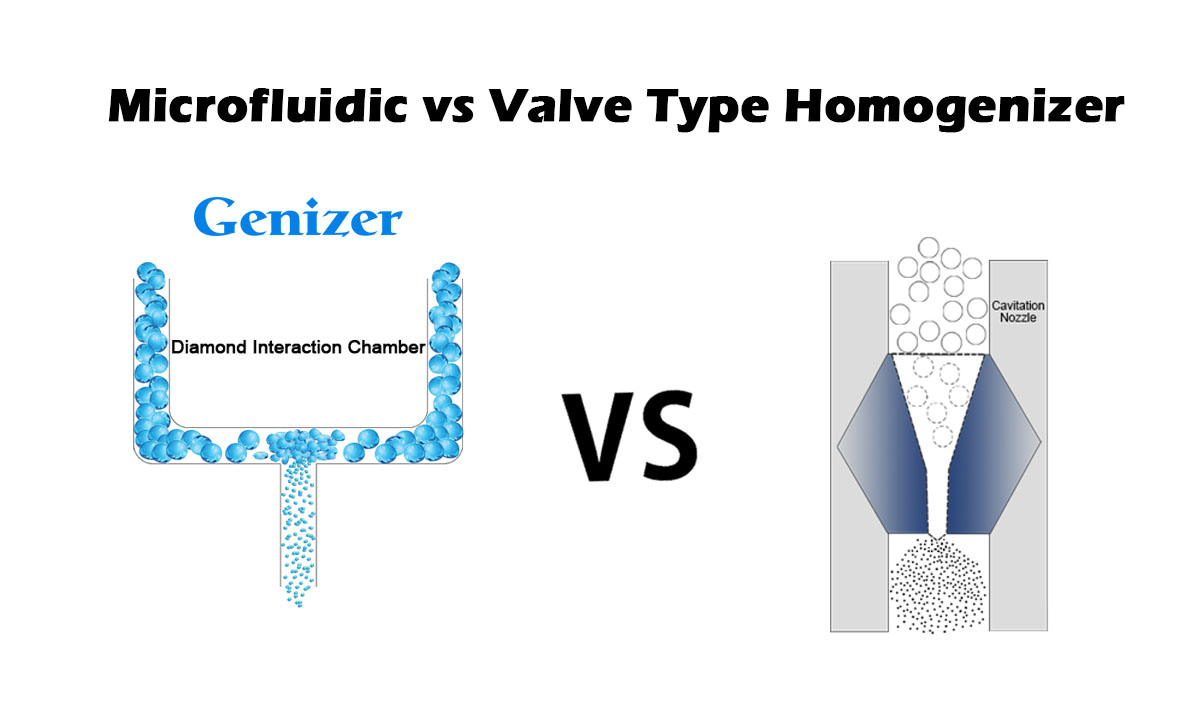
High-pressure homogenization is a vital technology used in various industries, such as pharmaceuticals, biotechnology, food processing, and cosmetics. It plays a crucial role in achieving consistent particle sizes, stable emulsions, and uniform suspensions. Among the leading technologies are microfluidic jet high-pressure homogenizers and valve-type high-pressure homogenizers. Recognizing the distinctions between these two types can help you make an informed choice for your specific needs.
Functionality of Microfluidic High-Pressure Homogenizers
Microfluidic homogenizers, like the Genizer high-pressure homogenizer, utilize a fixed geometry microchannel to maintain a consistent shear rate throughout the liquid.
This design enables precise control over the homogenization process, resulting in smaller droplets and more uniform particle size distributions.
Mechanism of Valve-Type High-Pressure Homogenizers
In contrast, valve-type high-pressure homogenizers use a valve assembly to regulate fluid flow, creating pressure that generates shear forces.
While this method is effective for larger-scale production, it may not offer the same level of precision in particle size control as microfluidic models.
Key Differences Between the Two Technologies
Shear Rate:
Microfluidic homogenizers provide a higher and constant shear rate, leading to improved mixing and dispersion, while valve-type homogenizers generate shear forces at varying velocities.
Particle Size:
Microfluidic homogenizers typically produce smaller droplet sizes and achieve more uniform particle size distributions, making them ideal for applications requiring precision.
Energy Efficiency:
Microfluidic homogenizers are more energy-efficient, converting less process energy to heat compared to valve-type homogenizers. This not only saves energy, but also helps prevent thermal effects from altering the physiochemical characteristics of any delicate materials undergoing processing.
Ease of Use and Maintenance:
Microfluidic homogenizers are user-friendly and easy to clean, requiring no specialized skills or knowledge, and they demand very little maintenance. In contrast, traditional valve-type high-pressure homogenizers require manual disassembly and cleaning of the homogenizer valves, and reinstalling the valves necessitates specialized knowledge.
Conclusion
Both microfluidic and valve-type high-pressure homogenizers have distinct advantages. Microfluidic homogenizers, like NanoGenizer Lab Scale High Pressure Homogenizer, excel in applications that demand precision, energy efficiency, and ease of operation, making them ideal for processes requiring careful control over particle size. On the other hand, valve-type homogenizers are well-suited for handling larger volumes, making them a preferred option for bulk production where precise particle size management may be less critical. Ultimately, your choice between these technologies should be guided by your specific application needs and desired outcomes.