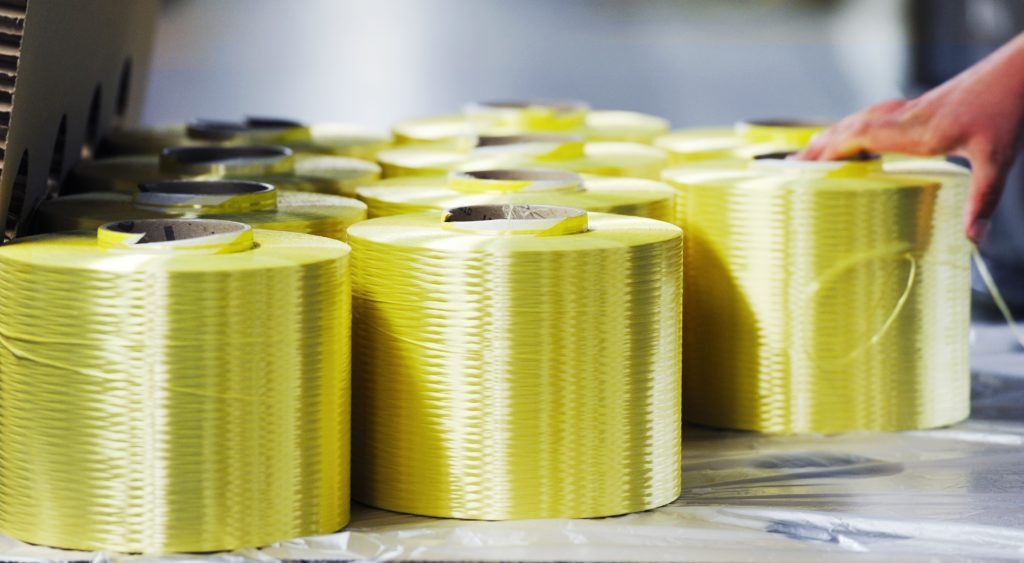
Aramid fibers are a class of heat-resistant and strong synthetic fibers. They are produced by condensation polymerization of aromatic dicarboxylic acid with aromatic diamines or diisocyanates. The resulting polyamides are characterized by relatively high tensile strength and heat resistance compared to other synthetic fibers. Structure and Properties They have a linear rigid-rod polymer structure which results in high strength and stiffness. The chain molecules are highly oriented along the fiber axis due to strong intermolecular and intramolecular hydrogen bonds. This orientation provides extraordinary tensile strength by efficiently transferring loads to the extended chain molecules. Commonly used Aramid Fibers have melting points as high as 500°C. Their strength loss is gradual above 250°C. Their high temperature stability arises from the aromatic structure and hydrogen bonding between polymer chains which restricts molecular motion at high temperatures. They are also characterized by high tensile strength, low extensibility, low specific density, bullet proof properties, and resistance to damage from fire, chemicals and rot. Production Process They are produced using fiber-spinning techniques from aromatic polyamides. The two most common aramid fibers are Kevlar and Twaron. Kevlar is produced from p-phenylenediamine and terephthaloyl chloride. The monomers first undergo polycondensation in a solution to yield low molecular weight poly(p-phenylene terephthalamide). This precursor is then spun into fibers using a wet-spinning process where it is extruded through a spinneret into a bath containing a solution of concentrated sulfuric acid and water. The acid causes the fibers to solidify and align into a liquid crystal state with high strength and modulus. The fibers are then washed, stretched, annealed and collected on a spool. Major Applications Bulletproof Vests and Body Armor The high tensile strength and low density of aramid fibers make them ideal for bulletproof vests and body armor applications. These vests utilize many woven layers of Kevlar or Twaron fabric. The fibers are able to dissipate kinetic energy from high-speed projectiles effectively through stretching. Tire Reinforcement Over 50% of all aramid fibers produced are used to reinforce car and truck tires. Kevlar and Twaron yarns and cords provide high strength and stability to tires while keeping their weight low. This allows for better vehicle control, handling, braking and fuel efficiency. Construction Materials They are used in ropes, cables, fabric and paper reinforcements for construction applications where high strength is required. Their use extends the lifespan of structures and makes them more durable against wear, tear and damage. Industrial Filtration The small diameter and inertness of them make them suitable for industrial fabric filters used in gas and liquid filtration. They are able to remove fine particles from harsh chemical environments. Personal Protective Equipment In addition to bulletproof vests, they are used in firefighter turnout gear, cut-resistant gloves, impact-resistant face shields and protective suits providing heat and cut protection. Advantages and Limitations Aramid fibers offer high tensile strength, heat and chemical resistance making them suitable for various industrial applications. However, their high cost and low ductility compared to other fibers are some limitations. The rigid molecular structure makes them susceptible to cracking and fracture if stressed beyond their elastic limit. Their production also requires harsh chemical processes. Nonetheless, they remain widely popular for applications requiring high strength and heat durability where cost is not a major constraint. Future Prospects With growing emphasis on safety, durability and fuel efficiency, demand for aramid fiber reinforced composites is expected to rise significantly across industries in the coming years. Ongoing research also aims to develop cost-effective production methods and new aramid materials with enhanced mechanical and thermal properties. Their use in new applications such as wind turbine blades and 3D printed parts holds promise. Though challenging, reducing raw material costs through bacterial fermentation could make aramid fibers more affordable and accessible on a larger commercial scale.
Explore More Related Article On- Dry Shampoo Market
About Author:
Money Singh is a seasoned content writer with over four years of experience in the market research sector. Her expertise spans various industries, including food and beverages, biotechnology, chemical and materials, defense and aerospace, consumer goods, etc. (https://www.linkedin.com/in/money-singh-590844163)