Freeze-Drying Equipment: An Overview of the Freeze-Drying Process and Machinery What is Freeze-Drying? Freeze-drying, also known as lyophilization, is a low-temperature dehydration process that involves freezing the material, reducing pressure, and removing the ice by sublimation. During freeze-drying, liquids such as water are removed directly from the solid phase to the gas phase without passing through the liquid phase, thus preventing the product from getting damaged. This makes freeze-drying suitable for heat-sensitive materials like food items, pharmaceuticals, and biologics that cannot withstand high temperatures. Main Components of Freeze-Drying Equipment Freeze-drying Equipment equipment typically consists of the following main components: Freezer: Used to freeze the material by lowering its temperature to or below the freezing point. This retains the structure of the material while ice is removed in the later stages. Drying Chamber: The frozen material is placed on a shelf inside the vacuum chamber and the pressure is reduced to facilitate sublimation. Different chamber types are available based on the required scale. Condenser: Used to collect the ice from the material through sublimation in the form of water vapor. The vapor condenses on the cooled surfaces of the condenser. Vacuum Pump: Maintains the low pressure inside the drying chamber for ice to sublime from the frozen material. Different pump types like rotary vane pumps are used depending on the needed vacuum level. Pressure Gauge: Monitors and displays the vacuum level inside the chamber. Temperature Controller: Regulates the temperature inside the chamber throughout the drying process. Defrosting System: Optional component that slowly raises the shelf temperature after drying to remove residual water vapor from the material. Loading Systems: Optional but useful additions for automated loading and unloading of products into and from the freeze dryer. Main Stages of Freeze-Drying Freeze-drying equipment is designed to carry out the three main steps of the lyophilization process: 1. Freezing: Material is loaded and quickly frozen at temperatures below its freezing point using the freezer component. This is usually done at atmospheric pressure. 2. Primary Drying: Frozen material is transferred under vacuum into the drying chamber. Pressure is reduced using the vacuum pump causing water to sublime directly from frozen form (ice) into water vapor. 3. Secondary Drying: After primary drying is complete, the material is further dried by slowly increasing its temperature to remove bound water. Temperature and vacuum level are carefully controlled throughout. Types of Freeze-Dryers Based on Scale of Operation Freeze-drying equipment is available in different configurations based on the required scale of operation: Pilot-Scale: Used for smaller quantities in research, development, and process validation. Chamber volume ranges from 0.5 to 10 liters. Laboratory or Benchtop-Scale: For small sample sizes, uses condenser temperature of -50°C or below. Chamber volume is less than 1 liter. Production or Manufacturing-Scale: Larger freeze dryers used for routine production in the pharmaceutical and biotech industries. Chamber volumes range from 10s of liters to 100s of liters. Bulk or Large-Scale: Very large freeze dryers to handle bulk product volumes for commercial manufacturing. Chamber volumes exceed 1000 liters. Require specialized design. Key Factors Considered in Freeze-Dryer Design There are several critical factors that equipment designers consider to optimize freeze-dryer performance: Shelf Design: Includes properties like material, temperature control, and spacing between shelves for vapor flow. Chamber Design: Factors include insulation, placement of condenser and shelf supports, port placement etc. Vacuum System: Selection of pump size, vacuum level needed, and inlet piping configuration. Condensation System: Design of condenser coils/plates for optimal heat transfer and vapor collection. Process Sensors: Selection of appropriate sensors to measure parameters like temperature, pressure, vacuum. Control System: Hardware and software for automated operation and real-time process monitoring. CIP/SIP Capability: Design for clean-in-place (CIP) and steam-in-place (SIP) validation and sterilization. Qualification Standards: Conformance to cGMP, 3A, ASME, and other applicable standards. Advantages of Freeze-Drying When designed and operated properly, freeze-drying offers several advantages over traditional drying methods: - Retains heat-sensitive properties: Sensitive compounds do not undergo thermal degradation. - Porous structure: Creates porous, light structure that regenerates quickly upon addition of water. - Long shelf life: Freeze-dried materials have excellent shelf life stability without need for refrigeration. - Low moisture content: Final moisture content of 1-2% allows for easy rehydration and storage. - No thermal degradation: Absence of heat prevents compromising nutritional value, flavors, fragrances etc. - Sterilization: Freeze-drying under vacuum sterilizes the final product, increasing shelf life further. Applications of Freeze-Drying With these advantages, freeze-drying is extensively used across industries like: - Pharmaceuticals: Processing of antibiotics, vaccines, biologics and other active pharmaceutical ingredients (APIs). - Food processing: Preservation of coffee, fruits, vegetables, dairy products etc. without loss of quality. - Biotechnology: Freeze-drying impacts viability of bacterial/yeast cultures, enzymes and other biologics. - Cosmetics: Freeze-drying helps long term stability and reconstitution of delicate cosmetic formulations. - Other uses: Includes preservation of plants/tissues, instant coffee/tea, water purification, and more. Conclusion Freeze-drying is a low-temperature dehydration technique uniquely suited for processing heat-sensitive materials due to absence of high heat. Proper freeze-drying equipment design coupled with optimized process parameters help maximize product quality attributes and stability. Advancements continue to make freeze-drying more efficient and economically viable across multiple industries that require high-quality preservation methods.
Here is an 1157 words long article on Freeze-drying Equipment

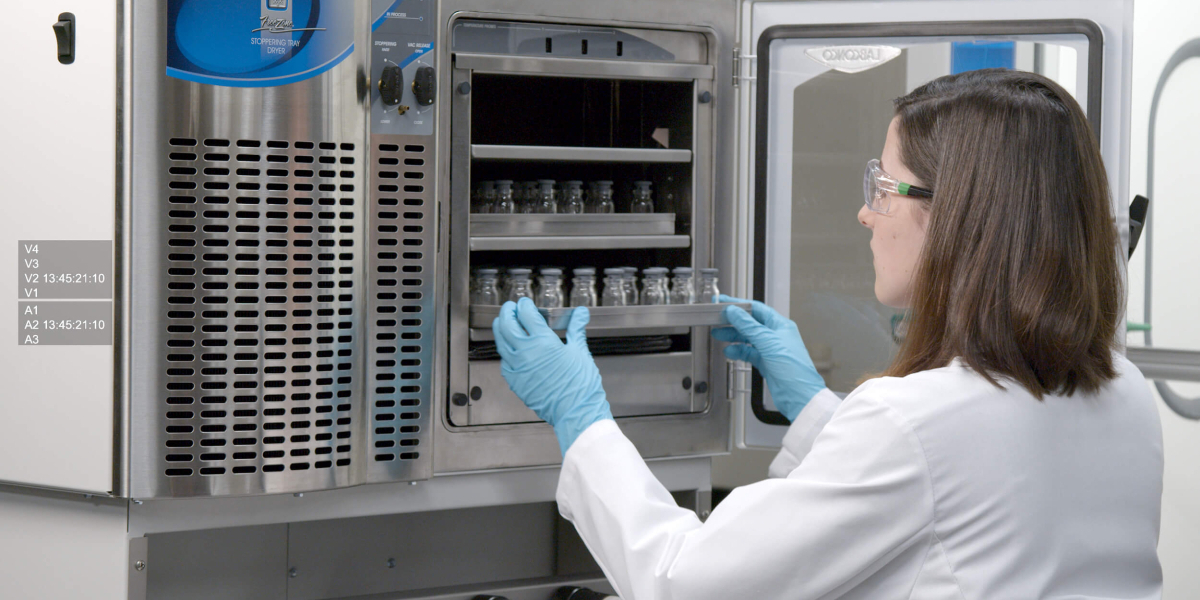
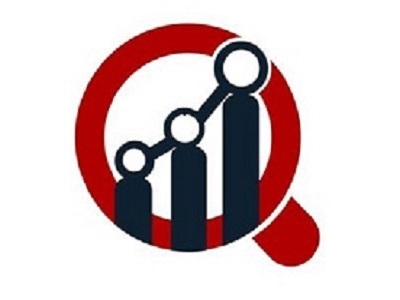
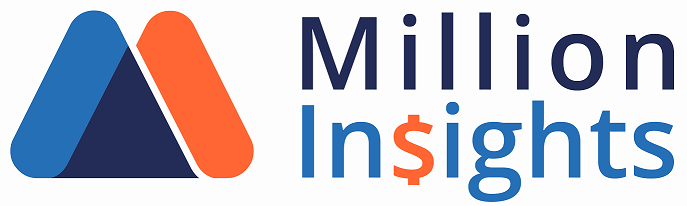
The global Freeze Drying Equipment Market size is estimated to reach USD 2.77 billion, by the end of 2025, and is projected to grow at a CAGR of 8.7% over the forecast years, 2019 to 2025, as per a new report published by Million Insights.
In addition, growing biotechnology sector and rising focus on emerging market by pharmaceutical companies are also supporting market growth.
Request a Sample PDF Copy of This Report @ https://www.millioninsights.com/industry-reports/freeze-drying-equipment-market/request-sample Market Synopsis of Freeze Drying Equipment Market: Furthermore, the increasing focus of biotechnology participants on drying equipment across Latin America, and Asia Pacific is driving market growth.
In addition, the development of vaccine & bio similar product in developed and developing countries is projected to positively impact on market growth.
Key players in the global market engage in the strategic acquisition of small manufacturers to gain an edge over their competitors.
Mobile freeze dryers are projected to register significant growth over the next few years mainly due to easy portability options.
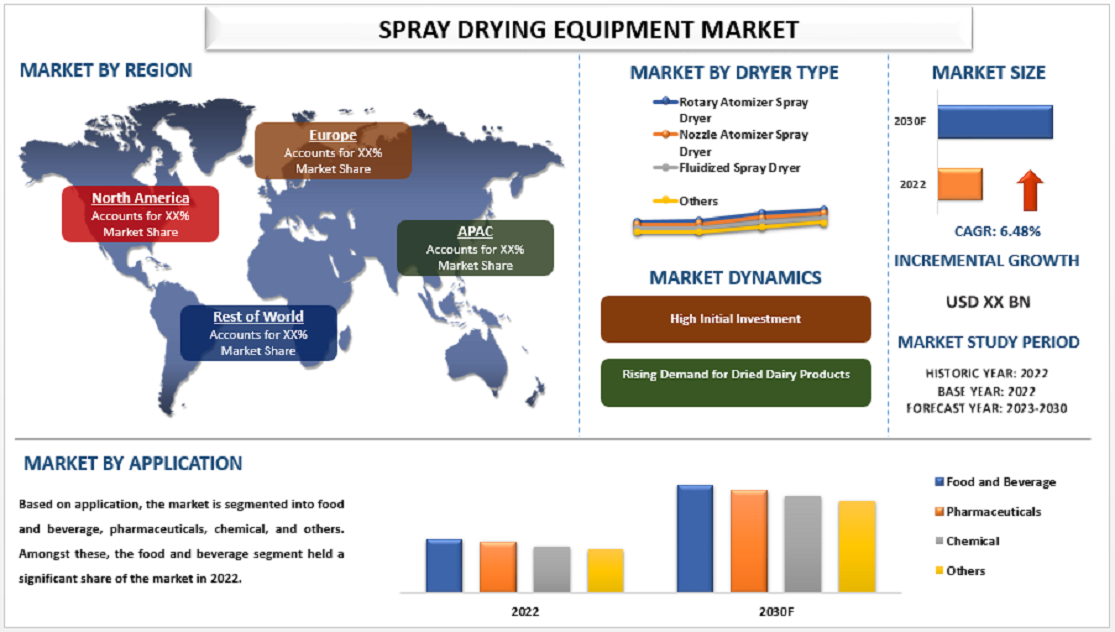
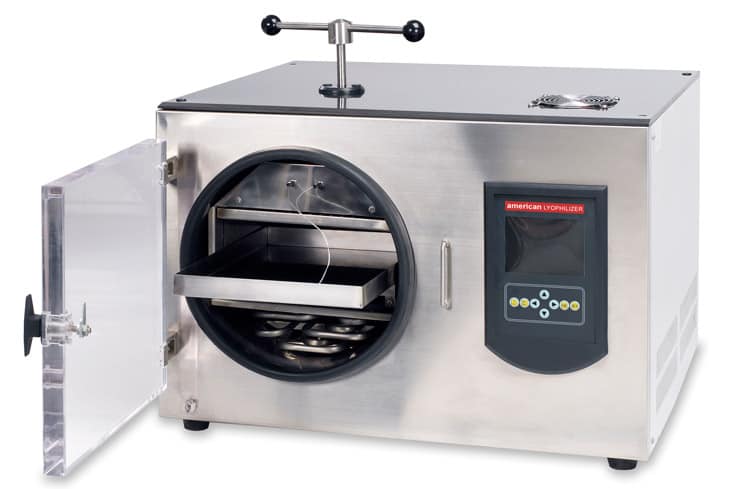
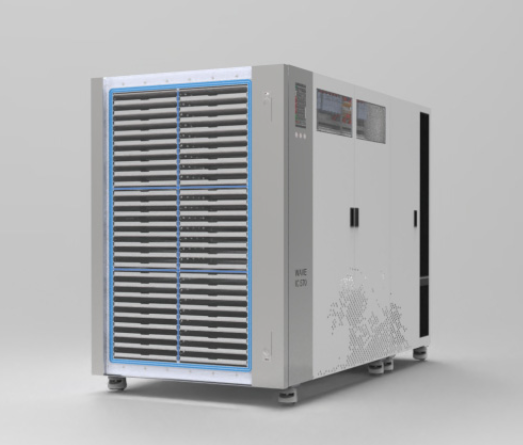
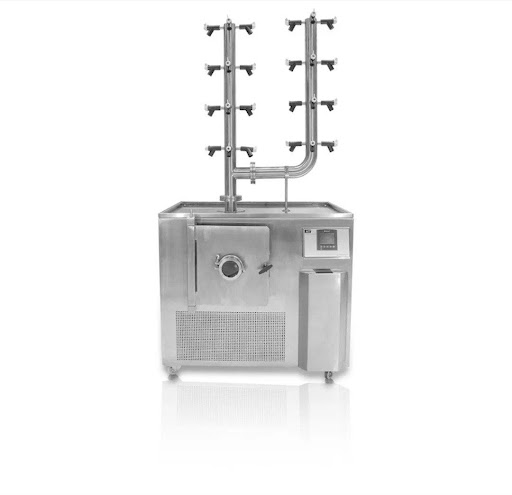
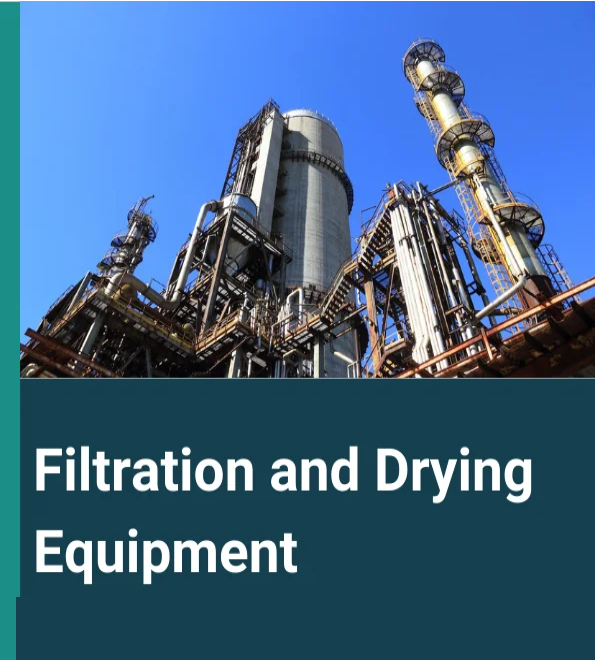
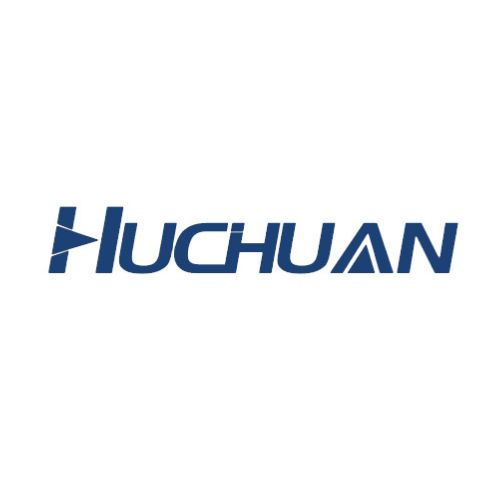
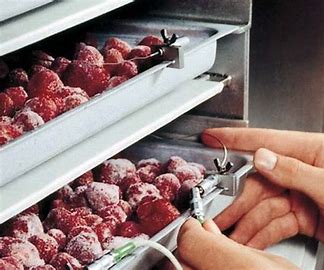
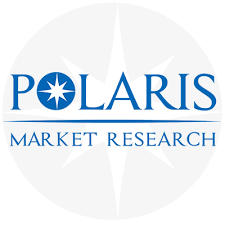
The global freeze drying equipment market size is expected to reach USD 3.11 Billion by 2026 according to a new study by Polaris Market Research.
This process preserves the quality, taste and texture of wide range of products.
The rapidly growing food processing industry is expected to be one of the major reasons for the augment in demand for freeze drying equipment over the forecast period.
Request a sample this report by clicking the link below: https://www.polarismarketresearch.com/industry-analysis/freeze-drying-equipment-market/request-for-sample Industrial freezers hold a major share in the global market.
This is mainly due to its usage in various industrial areas because of its high efficiency.
Pharmaceuticals and food processing industries are anticipated to hold a massive share in the global showcase.
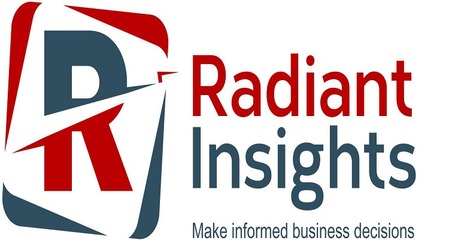
May 06, 2019: The global freeze drying equipment market size is anticipated to reach USD 2.77 billion by 2025, according to a study conducted by Grand View Research, Inc., progressing at a CAGR of 8.7% during the forecast period.
Furthermore, the market is also driven by expansion of the biotechnology industry and growing focus of pharmaceutical manufacturers on emerging markets.Growing interest of biotechnology industry participants in freeze drying equipment in regions such as Asia Pacific and Latin America is projected to drive the market.
Additionally, development of biosimilar and vaccines in developing regions and shift of various biopharmaceuticals manufacturing industries from developed to developing regions is poised to drive the market in these regions.
Additionally, various key players are aiming towards marking their market presence by acquiring small scale equipment manufacturers present in developing countries to gain a competitive edge.
This is also stoking the growth of the market.Download sample Copy of This Report at: https://www.radiantinsights.com/research/freeze-drying-equipment-market/request-sample Furthermore, mobile freeze dryers are poised to witness significant growth over the forecast period owing to their portability & ease of use.
Thus, the market is likely to witness lucrative growth in the biotechnology sector due to increasing demand for storage of umbilical cords which are further used in surgeries.
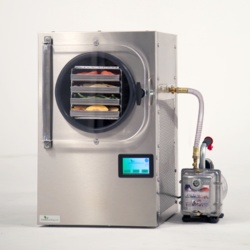
March 11, 2019: The global freeze drying equipment market size is anticipated to reach USD 2.77 billion by 2025, according to a study conducted by Radiant Insights Inc, progressing at a CAGR of 8.7% during the forecast period.
Furthermore, the market is also driven by expansion of the biotechnology industry and growing focus of pharmaceutical manufacturers on emerging markets.Growing interest of biotechnology industry participants in freeze drying equipment in regions such as Asia Pacific and Latin America is projected to drive the market.
Additionally, development of biosimilar and vaccines in developing regions and shift of various biopharmaceuticals manufacturing industries from developed to developing regions is poised to drive the market in these regions.
Additionally, various key players are aiming towards marking their market presence by acquiring small scale equipment manufacturers present in developing countries to gain a competitive edge.
Thus, the market is likely to witness lucrative growth in the biotechnology sector due to increasing demand for storage of umbilical cords which are further used in surgeries.
Additionally, key players are engaged in introducing innovative products in the market to maintain their market presence and shares.
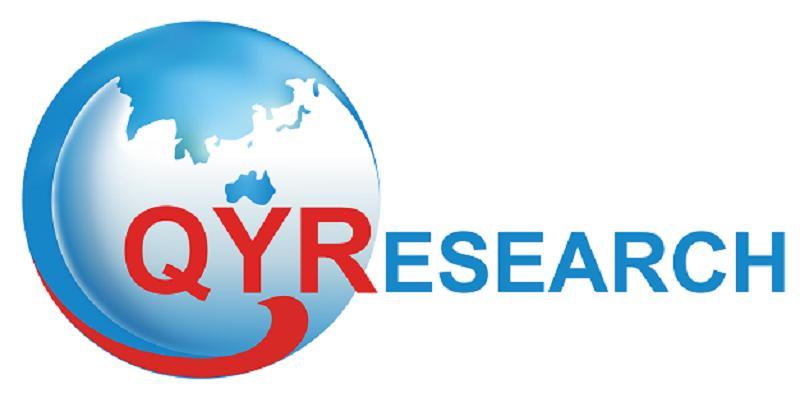
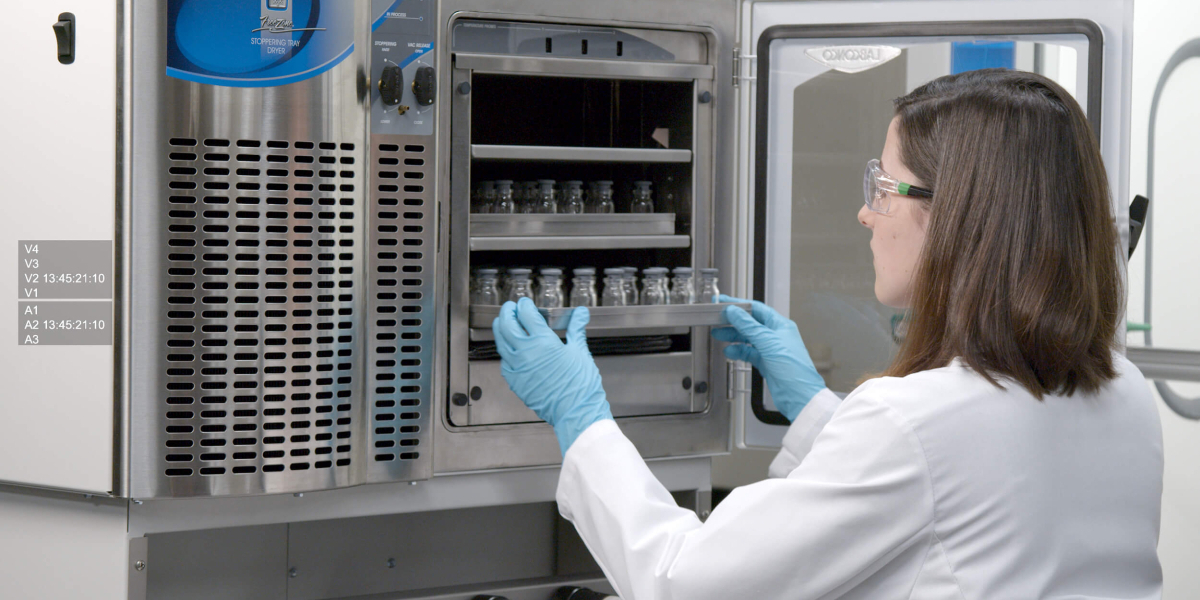
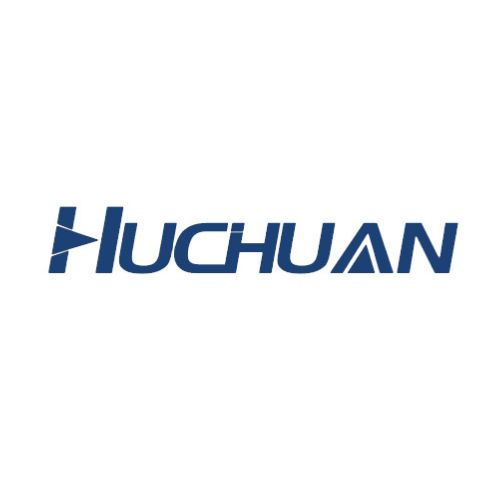
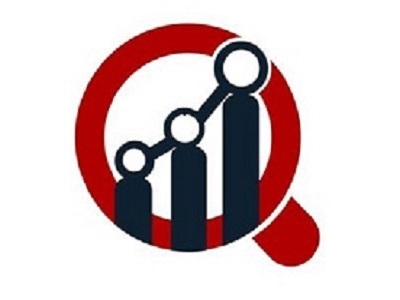
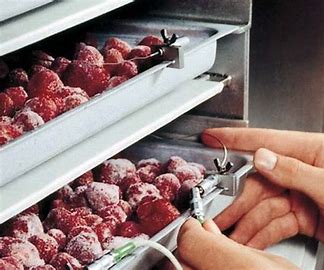
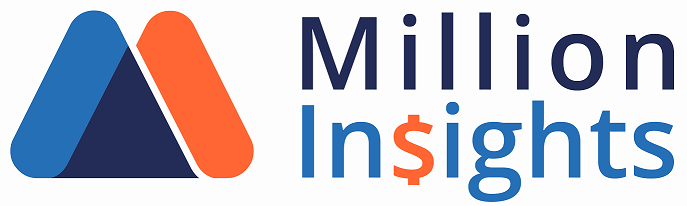
The global Freeze Drying Equipment Market size is estimated to reach USD 2.77 billion, by the end of 2025, and is projected to grow at a CAGR of 8.7% over the forecast years, 2019 to 2025, as per a new report published by Million Insights.
In addition, growing biotechnology sector and rising focus on emerging market by pharmaceutical companies are also supporting market growth.
Request a Sample PDF Copy of This Report @ https://www.millioninsights.com/industry-reports/freeze-drying-equipment-market/request-sample Market Synopsis of Freeze Drying Equipment Market: Furthermore, the increasing focus of biotechnology participants on drying equipment across Latin America, and Asia Pacific is driving market growth.
In addition, the development of vaccine & bio similar product in developed and developing countries is projected to positively impact on market growth.
Key players in the global market engage in the strategic acquisition of small manufacturers to gain an edge over their competitors.
Mobile freeze dryers are projected to register significant growth over the next few years mainly due to easy portability options.
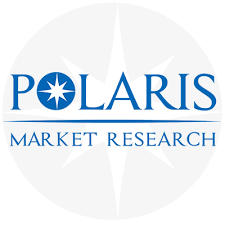
The global freeze drying equipment market size is expected to reach USD 3.11 Billion by 2026 according to a new study by Polaris Market Research.
This process preserves the quality, taste and texture of wide range of products.
The rapidly growing food processing industry is expected to be one of the major reasons for the augment in demand for freeze drying equipment over the forecast period.
Request a sample this report by clicking the link below: https://www.polarismarketresearch.com/industry-analysis/freeze-drying-equipment-market/request-for-sample Industrial freezers hold a major share in the global market.
This is mainly due to its usage in various industrial areas because of its high efficiency.
Pharmaceuticals and food processing industries are anticipated to hold a massive share in the global showcase.
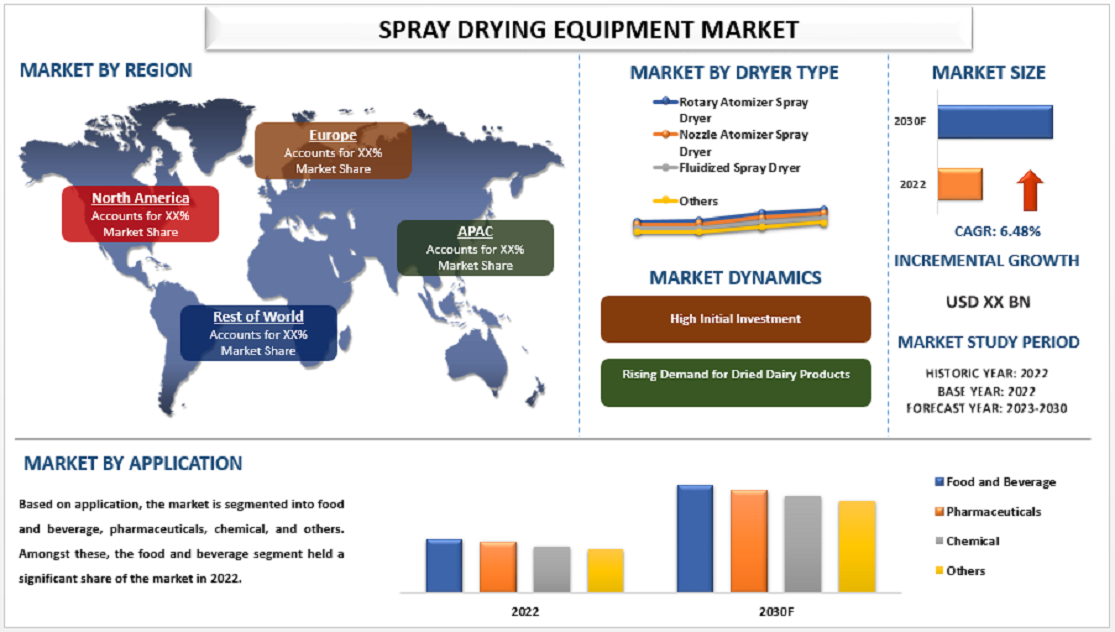
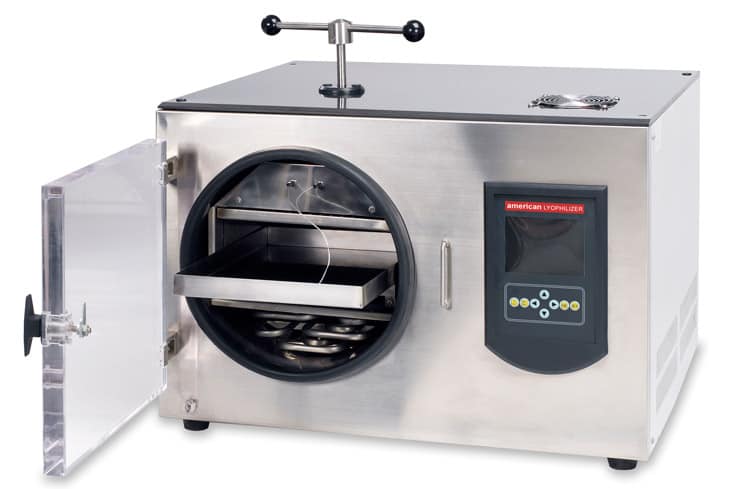
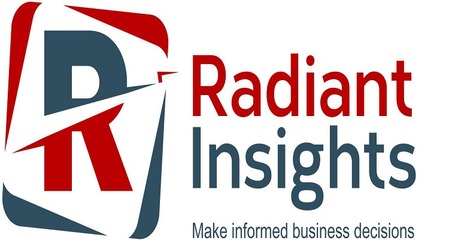
May 06, 2019: The global freeze drying equipment market size is anticipated to reach USD 2.77 billion by 2025, according to a study conducted by Grand View Research, Inc., progressing at a CAGR of 8.7% during the forecast period.
Furthermore, the market is also driven by expansion of the biotechnology industry and growing focus of pharmaceutical manufacturers on emerging markets.Growing interest of biotechnology industry participants in freeze drying equipment in regions such as Asia Pacific and Latin America is projected to drive the market.
Additionally, development of biosimilar and vaccines in developing regions and shift of various biopharmaceuticals manufacturing industries from developed to developing regions is poised to drive the market in these regions.
Additionally, various key players are aiming towards marking their market presence by acquiring small scale equipment manufacturers present in developing countries to gain a competitive edge.
This is also stoking the growth of the market.Download sample Copy of This Report at: https://www.radiantinsights.com/research/freeze-drying-equipment-market/request-sample Furthermore, mobile freeze dryers are poised to witness significant growth over the forecast period owing to their portability & ease of use.
Thus, the market is likely to witness lucrative growth in the biotechnology sector due to increasing demand for storage of umbilical cords which are further used in surgeries.
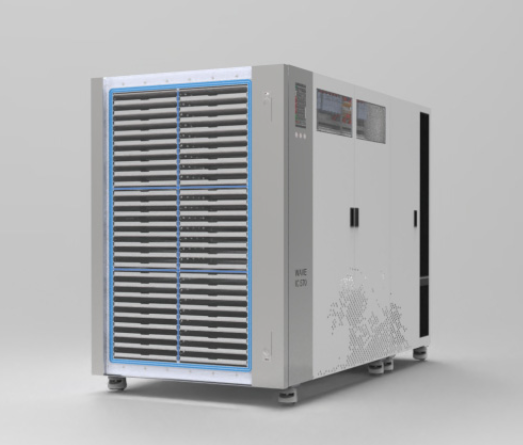
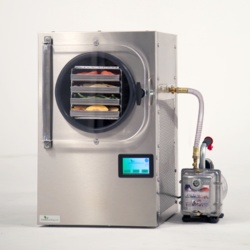
March 11, 2019: The global freeze drying equipment market size is anticipated to reach USD 2.77 billion by 2025, according to a study conducted by Radiant Insights Inc, progressing at a CAGR of 8.7% during the forecast period.
Furthermore, the market is also driven by expansion of the biotechnology industry and growing focus of pharmaceutical manufacturers on emerging markets.Growing interest of biotechnology industry participants in freeze drying equipment in regions such as Asia Pacific and Latin America is projected to drive the market.
Additionally, development of biosimilar and vaccines in developing regions and shift of various biopharmaceuticals manufacturing industries from developed to developing regions is poised to drive the market in these regions.
Additionally, various key players are aiming towards marking their market presence by acquiring small scale equipment manufacturers present in developing countries to gain a competitive edge.
Thus, the market is likely to witness lucrative growth in the biotechnology sector due to increasing demand for storage of umbilical cords which are further used in surgeries.
Additionally, key players are engaged in introducing innovative products in the market to maintain their market presence and shares.
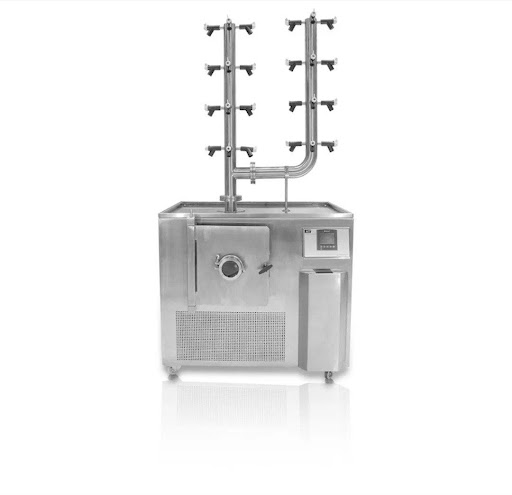
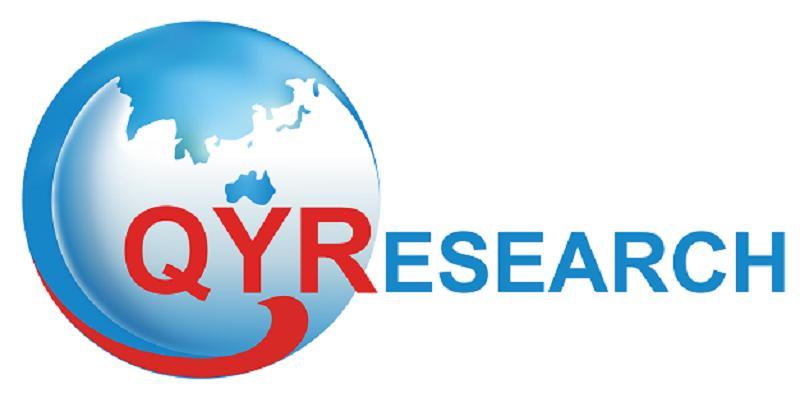
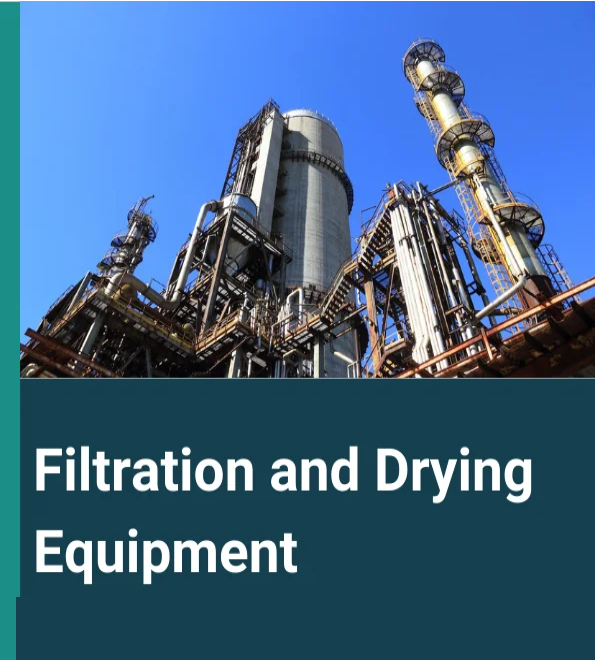