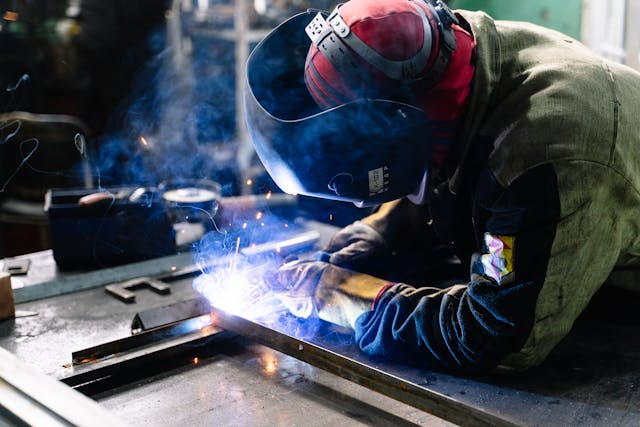
Wholesale MIG Welder
When it comes to welding, choosing the right tools makes all the difference. Among the various welding techniques, MIG (Metal Inert Gas) welding is one of the most popular for its versatility, ease of use, and ability to produce high-quality welds across a range of materials. But if you're in the market for a wholesale MIG welder whether for a manufacturing business, workshop, or fabricator shop—how do you ensure you're selecting the best equipment to meet your needs?
This guide is here to break down the essential features you should be looking for in a wholesale MIG welder. From power output to portability, we’ve got you covered.
Why a Quality MIG Welder Matters
MIG welding is renowned for its efficiency and adaptability, making it a valuable tool for both beginners and seasoned welders. But not all MIG welders are created equal. Choosing the right model ensures:
- Improved welding precision for professional-quality results.
- Durability to handle tough jobs and last for years in demanding environments.
- Cost-efficiency, saving you time and money in both purchase and operation.
Whether you're looking to upgrade your equipment or make your first wholesale investment, understanding the key features is paramount.
Top Features to Look for in a Wholesale MIG Welder
1. Adjustable Power and Voltage Settings
MIG welding requires precise control over heat and voltage to ensure quality welds. Look for machines with adjustable settings to accommodate a variety of materials like mild steel, stainless steel, and aluminum.
Why it Matters:
- Flexibility to work on thin or thick materials by increasing or decreasing voltage.
- Prevents issues like burn-through or weak welds.
Pro Tip:
Opt for a welder with a range of voltage settings (e.g., from 110V to 220V) to cover both light-duty and heavy-duty projects.
2. Wire-Feeding Mechanism
The wire-feeding system is the heart of a MIG welder. Consistent feeding is critical for smooth and uniform weld beads.
What to Check:
- A stable wire feed speed control system for precision.
- Dual-drive rolls for reliable wire movement without slipping.
Why You’ll Appreciate It:
An efficient wire-feeding mechanism reduces downtime and eliminates issues like tangling or jerking, ultimately giving you cleaner welds.
3. Portability and Build Quality
If you’re constantly moving between job sites or workspace stations, portability is a crucial factor. Look for lightweight but sturdy models.
Key Features:
- Welders with wheels or carrying handles for mobility.
- Compact designs without sacrificing power output or performance.
Build Quality Recommendations:
Choose a machine made with heavy-duty, durable metal casings to withstand daily wear and tear, especially in industrial setups.
4. Duty Cycle
The duty cycle is a measure of how long a welder can operate at maximum power before it needs to cool down. A higher duty cycle is critical for heavy-duty or high-volume projects.
Ideal Stats:
- Opt for a duty cycle of at least 40% at maximum amperage for industrial usage.
- For lighter tasks, a lower-duty cycle (25%-30%) may suffice.
Why it’s Important:
A high-duty cycle ensures fewer interruptions, higher productivity, and the ability to take on extended welding sessions with ease.
5. Amperage Range
The amperage range determines the amount of heat the welder can produce. Different welding projects require different amperage levels.
Example:
- Light projects (like automotive repairs): 30–130 amps.
- Heavy fabrication (like structural steel): 200+ amps.
Final Tip:
Choose a MIG welder with a sufficient amperage range to match your current needs while remaining versatile for future, more demanding work.
6. Ability to Operate on Gas/No-Gas Mode
Some MIG welders can operate in both gas-shielded and flux-cored welding modes, adding versatility to your investment.
Why Dual Mode Matters:
- Gas Mode provides greater control and is ideal for indoor use, where clean and precise welds are essential.
- No-Gas Mode is perfect for outdoor projects, as flux-cored wires self-shield against wind.
This flexibility allows your team to tackle diverse welding applications.
7. Ease of Use
MIG welding is already considered one of the easiest processes to learn, but a user-friendly interface can further enhance efficiency and reduce errors.
Look For:
- Digital control panels with clear displays for settings.
- Machines with pre-set modes for common welding tasks.
Time-Saving Benefit:
Simpler machines reduce the learning curve, allowing your team or clients to get up to speed quickly, maximizing investment returns.
8. Spool Gun Compatibility for Aluminum Welding
Aluminum welding requires specialized tools. A spool gun helps deliver smooth feeding of aluminum wire without tangling or snagging.
Features to Check:
- MIG welders with built-in spool gun compatibility.
- Models that allow seamless switching between materials for hybrid projects (e.g., steel and aluminum).
9. Accessibility to Replacement Parts
Even top-tier welders need occasional maintenance or part replacements. Choose a welder from a reputable brand that provides easy access to spare parts.
Brands to Consider:
Miller, Lincoln Electric, ESAB, and Hobart are known for reliable equipment and support.
Bonus Tip:
Check if the vendor offers long warranties or low-cost replacement programs for critical components like drive rolls or nozzles.
10. Cost Efficiency and Warranty
When purchasing wholesale, you’ll likely buy multiple units. Balancing affordability with high performance and durability is key.
What Makes it Cost-Effective:
- A model with energy-efficient features to lower operational costs.
- Optional service plans for extended support.
The Safety Net:
A solid warranty (typically 3–5 years) reflects brand confidence in their product and provides peace of mind for your investment.
Additional Factors to Consider
Industry-Specific Needs
Are you purchasing a welder for automotive repairs, heavy construction, or artistic creations? Make sure your purchase aligns with your industry’s unique needs.
Supplier Reputation
Ensure your wholesale supplier offers transparent deals, machine demos, and excellent customer support. Look for trusted suppliers who specialize in welding equipment.
Choosing the Right MIG Welder for Your Business
With the right information at hand, selecting a quality MIG welder doesn't have to be overwhelming. Focus on key features such as adjustable settings, portability, and a reliable wire feed system. Consider your industry-specific needs and future growth when deciding which wholesale options best suit your business.
Upgrading your equipment isn’t just a financial investment—it’s an investment in efficiency, quality, and your team’s ability to deliver top-notch results.