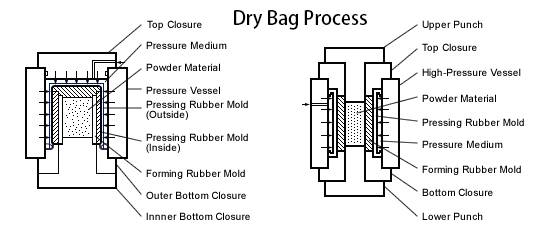
Precision farming has become a revolutionary technology in the manufacturing sector known for being dependable, strong, and efficient. With these state-of-the-art compression processes, industries can achieve high-quality production and qualify for strict tests. This process has been used in various sectors, such as aerospace, medicine, and automotive, and remains a significant part of material formation with the help of advanced technology.
Maintaining a uniform density and superior strength has become achievable with the help of the advanced method of compression invented by mankind. It is hard to find a place where Dry Bag Isostatic Pressing is used as it helps achieve good quality results, whether the component is complicated or just a simple piece.
How It Works
Isostatic Compression employs the mechanism of isotropic equal stress, which inhibits the nonuniform density and microstructure of the material. Instead of the conventional techniques of pressing from only one side, this process molds the top and bottom by pushing each other directly from a distance and, eliminating defects, leading to the production of more powerful and more durable products. Due to the formation of unblemished complex configurations, it has become the first option for many industrial sectors.
Versatility in Applications
This technique is not exclusive to a single industry—it is a significant contributor in multiple sectors. Be it aerospace or medical devices, producers depend on this method to fabricate high-precision components with better resilience. Dry Bag Isostatic Pressing adds value to lightweight and robust components, and electronics by forming complicated, precise parts.
Benefits That Stand Out
The application of this technique has a lot of benefits, mainly due to the offer of the same value. Homogeneity in the material density leads to the long life of the product and its faultless work, hence the lower rate of defects. Besides, it is also very flexible because it can be used with different materials such as metals and ceramics.
Why Precision Matters
In fields that require high exactness, a dependable forming process is a necessary determinant. Just a density flaw alone is enough to make the part vulnerable and possibly unreliable to the operation it is supposed to perform. Isostatic Compression makes sure that all the products receive the same pressure distribution. Thus, they meet strict quality standards and can be used in high-performance sectors.
Choosing the Right Approach
This forming method is chosen based on parameters such as the kind of material, the intended use, and the required precision. Weighing the benefits of different strategies helps makers formulate the right option, leading to the overall rational stem. Relying on good ways of going ahead not only leads to a quick increase in turnover of quality production but also leads to the steady achievement of the company.