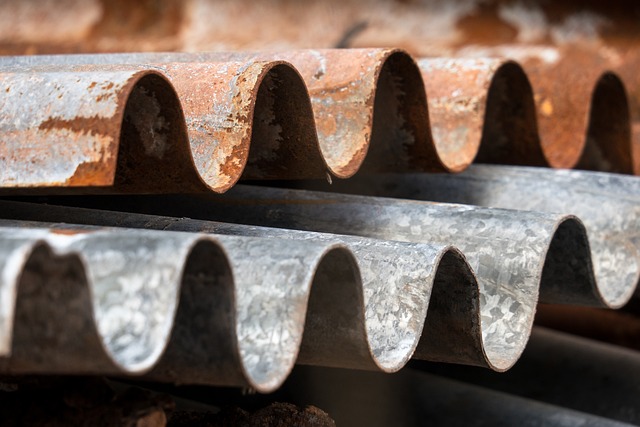
Sheet Metal Forming Processes
One of the primary fabrication processes used in automotive sheet metal production is sheet metal forming. This involves shaping sheet metal blanks into desired geometries through operations like punching, stamping, embossing, bending, and coining. For passenger vehicles, the sheet metal components commonly produced this way include body panels, hoods, roofs, doors, fenders, wheels, and more.
A variety of presses are used for Automotive Sheet Metal Components forming depending on the component geometry and production volumes. For high-volume production parts, gigantic hydraulic presses or mechanical presses are used to stamp complex 3D shapes in single hits from coils of coil-steel or aluminum blanks. These mega-presses can exert pressures over 1000 tons and produce thousands of parts per hour.
For smaller production runs or prototypes, small hydraulic or mechanical presses may be sufficient. These presses can form simple 2D components or assemble multiple stamped parts. When extreme accuracies or complex freeform shapes are required, more specialized presses like transfer presses or servo presses are utilized. Transfer presses use a series of progressive dies to stamp, trim, pierce and bend the blank in multiple stages. Servo presses leverage computer-controlled motors and position sensors for unmatched precision and flexibility.
Advances in Material Science and Technology
Significant advances in materials technology have enabled lighter and stronger automotive body designs. Premium vehicles now feature complex multi-material structures to maximize performance and efficiency. For example, some high-end models employ an aluminum-intensive spaceframe with magnesium or carbon fiber reinforcements.
New grades of advanced high-strength steels (AHSS) have tensile strengths over 1000 MPa, nearly triple that of ordinary steel. Tailor-rolled blanks (TRB) consist of different thickness and strengths strategically embedded within the blank to optimize stiffness and absorption at critical locations. New aluminum alloys have higher formability and dent resistance compared to traditional 6xxx and 7xxx series alloys. Magnesium continues to gain ground in applications like front end closures, thanks to its light weight and energy absorption ability. Even plastics and composites are playing a bigger role as class-A surfaces and load-bearing structures.
Virtual Prototyping and Data Analytics
To design complex body structures made from these advanced materials, vehicle engineers leverage CAE simulation techniques and virtual prototyping software. FEM analysis allows structural evaluation of potential designs under realistic loads before any physical prototypes are made. Sheet metal CAD programs digitally model the forming process through techniques like finite element forming analysis to predict material flow, thinning, and error prone zones. Some even simulate the kinematics of actual stamping presses to validate tool/die designs.
Advanced analytics on collected manufacturing data helps engineers optimize the production process as well. Data from press sensors, vision systems and factory operations can reveal opportunities to improve tooling, reduce cycle times, minimize material waste, and ensure consistent part quality. When combined with digital models, this data finds correlations between process parameters and end-results to enable design adjustments that make parts easier and less expensive to manufacture.
Future Trends in Automotive Sheet Metal Fabrication
additive manufacturing will start playing a bigger role by enabling rapid tooling for prototype validations or spare/replacement parts with low volumes. Technologies like binder jetting or laser sintering would allow fabricating sheet metal forming tools or lightweight structural components directly from 3D CAD data without complex tooling lead times.
To achieve higher levels of customization, the evolution of smart connected vehicles will drive more just-in-time and on-demand manufacturing concepts. Sheet metal components may be tailored, fabricated and assembled based on the evolving needs of individual vehicle owners or changing market segments over the lifetime of a vehicle platform. Digital part records tracking design evolutions and revisions will minimize duplicate engineering efforts.
Sustainable manufacturing practices using renewable energy sources, closed-loop recycling processes, and zero-waste strategies will gain prominence. New approaches like thermoforming of recycled content resins offer opportunities to reuse sheet metal scrap in high-volume production. Advances in equipment electrification, robotics, AI safety, and next-gen adhesives will enhance workplace ergonomics and further automate complex sheet metal joining operations. Overall, automotive sheet metal fabrication will continue down the path of increased flexibility, precision and sustainability to enable more affordable future mobility solutions.
Get This Report In Japanese Language
Get This Report In Korean Language
About Author:
Vaagisha brings over three years of expertise as a content editor in the market research domain. Originally a creative writer, she discovered her passion for editing, combining her flair for writing with a meticulous eye for detail. Her ability to craft and refine compelling content makes her an invaluable asset indelivering polished and engaging write-ups.
(LinkedIn: https://www.linkedin.com/in/vaagisha-singh-8080b91)