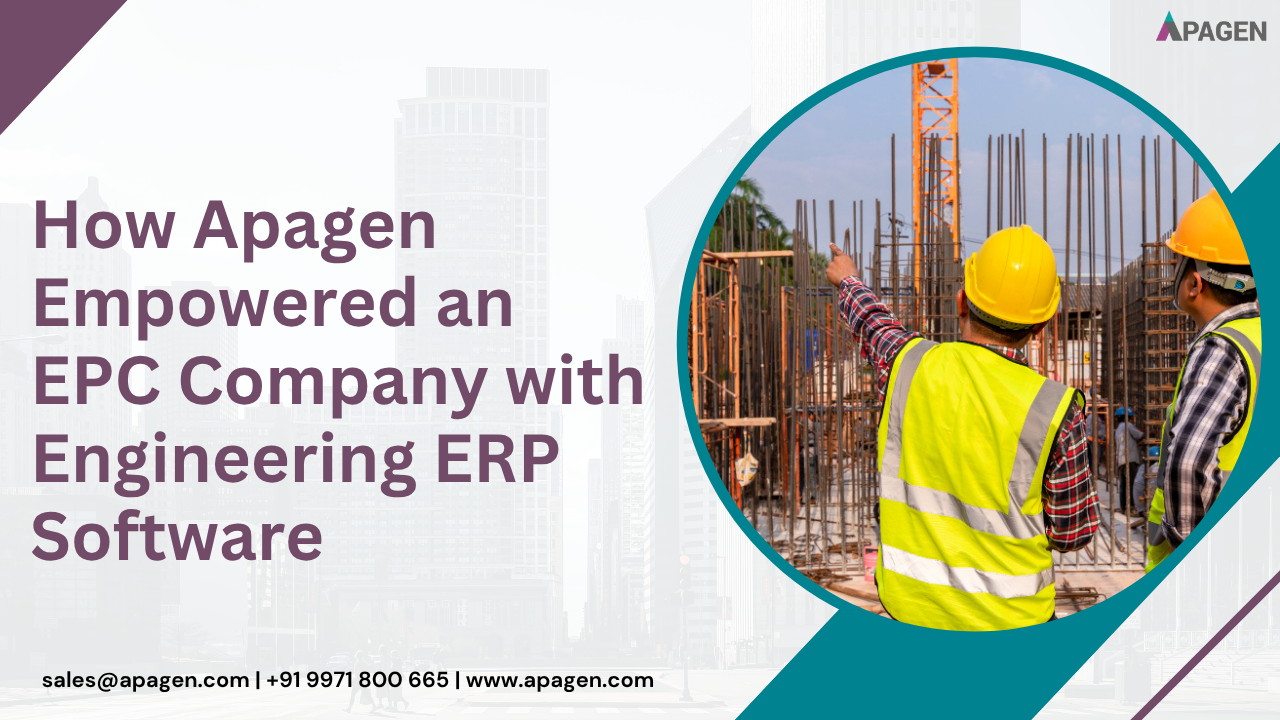
Introduction: Building Better with ERP for Engineering
In the competitive and deadline-driven world of EPC (Engineering, Procurement, and Construction), precision and planning are everything. Our client, a growing mid-sized EPC contractor headquartered in India with multiple project sites across Asia and the Middle East, was struggling with project delays, cost overruns, siloed data, and a lack of real-time visibility into project performance.
With over 200 employees across engineering, procurement, project management, and finance departments, their operations had grown too complex for traditional tools like spreadsheets and standalone software. They needed a centralized, scalable, and customizable engineering ERP software — one that could connect all functions and provide a single source of truth.
That’s where Apagen Solutions came in.
Our team of Odoo ERP specialists took on the challenge, and what followed was a complete business transformation. This case study outlines how we helped the client improve efficiency, control project budgets, streamline procurement, and manage engineering workflows more effectively with ERP for engineering — all within a single, integrated system.
Client Overview
- Industry: EPC (Engineering, Procurement, and Construction)
- Location: Headquartered in India, with projects in the Middle East and Southeast Asia
- Team Size: 200+ staff including engineers, procurement officers, project managers, and finance teams
- Annual Turnover: INR 200 Cr+
- ERP Objective: Replace siloed systems with a unified, end-to-end engineering ERP software that supports multi-site project execution
The Challenge: Operational Chaos and Lack of Visibility
Before partnering with Apagen, the EPC firm faced several operational hurdles:
Disconnected Systems Each department used separate tools: engineers used AutoCAD and MS Project, procurement relied on Excel, while finance tracked payments manually. There was no unified system, leading to double entries, data mismatches, and hours wasted in coordination.
Procurement Bottlenecks Procurement teams struggled to track vendor RFQs, price comparisons, and purchase order histories. Delays in material delivery led to project halts, while poor vendor management increased procurement costs.
Project Budget Overruns Due to the lack of real-time cost tracking, projects frequently went over budget. Managers couldn’t track budget vs actuals during execution, only discovering discrepancies after financial reporting.
Inefficient Resource Allocation Workforce and equipment were assigned manually. There was no clear overview of which teams or resources were deployed where, leading to under-utilization and scheduling conflicts.
Why They Chose Apagen & Odoo ERP
The client evaluated multiple engineering ERP software providers, including proprietary options and local ERP vendors. But they needed:
- Flexibility to customize modules for engineering workflows
- Affordable total cost of ownership
- Integration with tools like AutoCAD, Primavera, and email
- Multi-project and multi-site support
- A partner who understood EPC domain challenges
Apagen’s strong track record in ERP for engineering firms, deep Odoo expertise, and consultative approach stood out.
We conducted detailed business requirement workshops across departments, mapped their pain points, and demonstrated how Odoo could be molded into an EPC-specific ERP — without the heavy cost and complexity of traditional ERP systems.
The Solution: Engineering ERP Software Built with Odoo
Modules Implemented:
- Project Management — Gantt views, task dependencies, milestones, multi-level WBS
- Purchase Management — RFQ automation, vendor price comparison, PO tracking
- Inventory & Warehouse — Multi-site inventory, GRNs, stock movement, location tracking
- Accounting — Budget planning, project-wise cost centers, vendor invoicing
- HR & Timesheet — Resource allocation, time tracking by project and role
- Document Management — Drawing submissions, RFI logs, revision controls
- Custom Integrations — AutoCAD drawing version tracking and project site reporting via mobile app
Deployment Phases:
- Phase 1: Core ERP modules (Project, Purchase, Inventory, Accounting) for HO and one pilot project site
- Phase 2: HR, Timesheet, Document Control, and integration with Primavera
- Phase 3: Rollout across all ongoing projects and regional offices
The entire rollout took 5 months, with key process owners trained and adoption supported through live workshops and weekly check-ins.
Key Benefits & Business Impact
After going live with the Odoo-powered engineering ERP software, the client began seeing improvements almost immediately.
Project Execution Efficiency
- Real-time visibility into project progress, pending tasks, and engineering deliverables
- Delays flagged early, corrective actions taken proactively
- Tasks linked to BOQs, enabling progress-based billing
Smarter Procurement
- Vendor RFQs are now auto-generated based on BOQ demands
- Price comparisons and vendor history accessible instantly
- Material lead times tracked, avoiding last-minute rushes
Financial Control
- Live dashboards for budget vs actuals
- Alerts for cost overruns and material overconsumption
- Site engineers can raise purchase requests directly from mobile
Streamlined Resource Allocation
- Centralized visibility of manpower and equipment usage across sites
- Timesheets auto-populate project costing and payroll
- Reduces idle resources and increases site productivity
Quantifiable Outcomes
- 25% Reduction in Project Delays due to better scheduling and material availability
- 30% Procurement Cost Savings through vendor negotiations based on historic pricing data
- 40% Faster Reporting with automated dashboards replacing manual data collation
- 99% Accuracy in project billing by linking executed tasks with BOQ items
- ROI achieved in just 9 months of go-live
Client Testimonial
“Before Apagen and Odoo ERP, our departments worked in silos. Now we have a connected platform that gives us control over every aspect of our engineering projects. From procurement to execution and billing, everything is traceable and transparent. Apagen’s team made ERP adoption easy and painless.” — Project Director,
Lessons Learned and Best Practices
Implementing ERP in an EPC environment comes with its own complexities. Here’s what made this implementation a success:
- Department-Wise Rollout: Tackled the most critical pain points first (purchase and project management)
- Customization Where It Matters: Focused on industry-specific features instead of overloading with unnecessary modules
- User Involvement: Included engineers and site managers early in the process
- Mobile Support: Enabled mobile approvals and real-time site data updates
Why Odoo is the Right ERP for Engineering Firms
For EPC and engineering service providers, Odoo offers:
- Highly customizable workflows
- Project-based accounting and costing
- Seamless integration with design tools and field reporting apps
- Lower cost of ownership compared to traditional engineering ERP software
- Flexibility to adapt as the business scales
As an open-source ERP, it empowers companies to innovate and refine their processes without being tied to expensive licensing models.
Conclusion
Engineering firms don’t just need an ERP — they need an ERP for engineering that understands the dynamics of design, procurement, construction, and costing. At Apagen, we’ve made it our mission to deliver tailored solutions that help EPC firms achieve operational excellence, faster project execution, and better profitability.
The success of this EPC client is a shining example of how domain-specific ERP, when implemented with deep understanding and expertise, can create massive business impact.
Looking to implement ERP in your EPC or engineering services company? Let’s talk.
Email: sales@apagen.com Phone: +91 9971 800 665