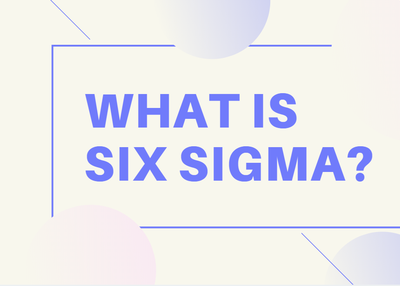
Six Sigma originates from a 19th Century numerical hypothesis, however discovered its way into the present standard business world through the endeavors of an engineer at Motorola during the 1980s. Presently proclaimed as one of the chief methodological practices for improving consumer satisfaction and improving business forms, Six Sigma has been refined and idealized throughout the years into what we see today.
Regardless of the defining, the objective continues as before: Six Sigma looks to improve business forms by expelling the reasons for mistakes that lead to deserts in an item or administration. It achieves this by setting up an administration framework that efficiently recognizes mistakes and gives techniques to killing them.
The individuals who learn Six Sigma practices accomplish assignments at each dimension of achievement, including Green Belt, Black Belt, Master Black Belt and Champion.
The Beginnings of Six Sigma:
The procedure that prompted Six Sigma was started in the Nineteenth Century with the bell curve created by Carl Fredrick Grauss. During the 1920s, analyst Carl Shewhart, an establishing individual from the Foundation of Scientific Insights, demonstrated that a procedure required amendment after it had veered off three sigmas from the mean.
Push ahead to the 1970s, when Motorola senior official Art Sundry grumbled about the absence of predictable quality in the organization's items, as per the 2006 book "Six Sigma" by Richard Schroeder and Harry Mikel.
As indicated by the acknowledged story from various sources, Motorola specialist Bill Smith in the end addressed the call to reliably fabricate quality items by working out the strategies of Six Sigma in 1986. The framework is impacted by, yet unique in relation to, other administration improvement methodologies of the time, including All out Quality Administration and Zero Imperfections.
Some of the Major Aspects of Six Sigma:
With an end goal to carry tasks to a "six sigma" level – basically, 3.4 imperfections for each one million chances – the technique calls for constant endeavours to come to the heart of the matter where they produce steady and unsurprising outcomes.
Deconstructing the assembling procedure down to its basic parts, Six Sigma characterizes and assesses each progression of a procedure, looking for approaches to improve efficiencies in a business structure, improve the nature of the procedure and increment the main concern benefit.
Toward that end, the procedure requires the preparation of workforce in Six Sigma, including learner Green Belts, Black Belts who frequently head up individual projects, and Master Black Belts who search for approaches to apply Six Sigma over a business structure to make upgrades.
A definitive objective is to improve each procedure to a "six sigma" level or better. Does it work? Motorola detailed in 2006 that the organization had spared $17 billion utilizing Six Sigma.
Methodologies of Six Sigma:
There are two noteworthy philosophies utilized inside Six Sigma, the two of which are made out of five segments, as per the 2005 book "JURAN Foundation Six Sigma Breakthrough and Beyond" by Joseph A. De Feo and William Barnard.
DMAIC: This strategy is utilized basically for improving existing business forms. The letters represent:
Characterize the issue and the undertaking objectives
Measure in detail the different parts of the present procedure
Break down information to, in addition to other things, discover the root surrenders in a procedure
Improve the procedure
Control how the procedure is done later on.
DMADV: This technique is commonly used to make new procedures and new items or administrations. The letters represent:
Characterize the undertaking objectives
Measure basic parts of the procedure and the item abilities
Break down the information and create different plans for the procedure, in the end picking the best one
Plan and test subtleties of the procedure
Confirm the plan by running reenactments and a test case program, and afterward giving over the procedure to the customer
There are additionally various administration devices utilized inside Six Sigma. While there are beyond any reasonable amount to list, here are subtleties on a couple of them.
Five Whys – This is a strategy that utilizations inquiries to get to the main driver of an issue. The strategy is basic: essentially express the last issue (the vehicle wouldn't begin, I was late to work again today) and afterward pose the inquiry "why," stalling the issue to its underlying driver. In these two cases, it may be: on the grounds that I didn't keep up the vehicle appropriately and in light of the fact that I have to go out prior to get the opportunity to take a shot at time. The procedure previously came to noticeable quality at Toyota.
CTQ Tree – The Basic to Quality Tree chart separates the parts of a procedure that delivers the highlights required in your item and administration in the event that you wish to have fulfilled clients.
Main driver Investigation – Much like the Five Whys, this is a procedure by which a business endeavors to recognize the underlying driver of an imperfection and after that right it, as opposed to just adjusting the surface "manifestation" of the issue.
At last, the majority of the devices and procedures in Six Sigma fill one need: to streamline business forms so as to deliver the most ideal items and administrations with the littlest measure of deformities. Its appropriation by enterprises far and wide is both a marker of and demonstration of its wonderful achievement in the present business condition.
For KPMG Lean Six Sigma Training registrations mail to
[email protected] or call at +91 9555688555 or +91 9022033666.
Lean Six Sigma Black Belt Training Programme
Lean Six Sigma Green Belt Training Programme