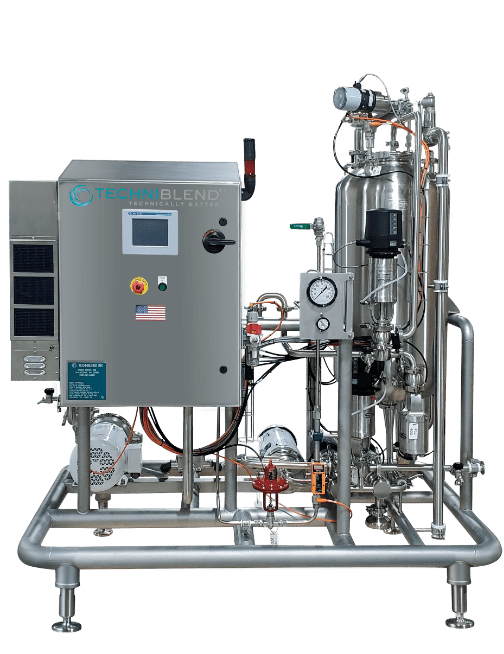
Whether you’re drinking a soda, a beer, a seltzer, or a cider, you’re sure to notice the fizzy, effervescent zip created by carbonation. Consumers seemingly can’t get enough of these funky little bubbles of carbon dioxide. Carbonation rules the beverage aisle, and as a result, beverage carbonation systems play an essential role in the beverage manufacturing industry.
What is Carbonation?
Carbonation is completely commonplace. You can find and purchase a carbonated beverage almost anywhere; but what is carbonation? Carbonation is the name we use to describe the result of the carbonation process. The carbonation process is carried out when carbon dioxide is dissolved into a given liquid. Once the carbonation process is complete, the liquid in question (generally a beverage) will be filled with little gas bubbles that produce the familiar fizzy effect we associate with carbonation.
How do Beverage Carbonation Systems Work?
Carbonating a beverage is not a simple task. Beverage carbonation systems have to be quite complex to effectively introduce carbon dioxide into a given beverage. Beverage carbonation systems work by pumping the beverage that is slated for carbonation into a special, pressurized tank. Once the beverage is in the tank, inert carbon dioxide is added into a reserve tank through some type of injection line. The beverage is then chilled until it reaches a certain temperature, at which point the carbon dioxide is released from the reserve tank. The beverage and the gas meet, and the gas is dissolved into the liquid.
Beverage carbonation systems make it possible for beverage producers to bring the texture of their products from flat to full. Without them, sodas wouldn’t have their signature sparkle, and beer would lack its famous foam. It is hard to imagine what the beverage industry would be without beverage carbonation systems to add a bit of pep to our drinks of choice.