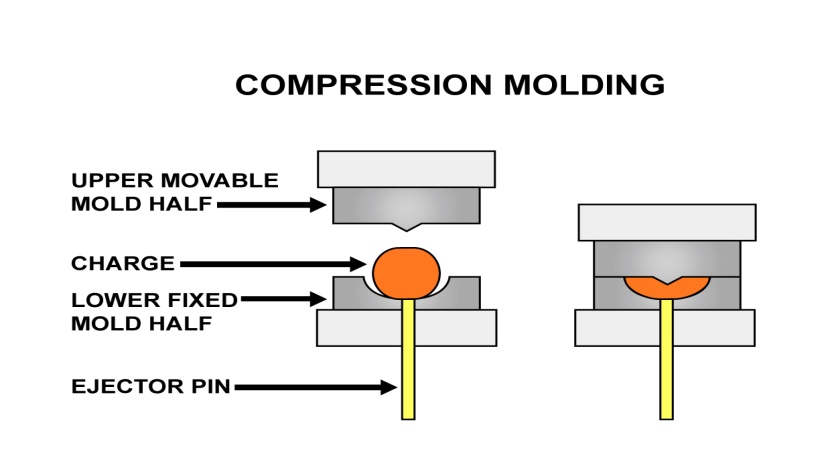
Compression molding is a manufacturing process where a material is placed into an open, heated mold cavity. It is the perfect choice for the manufacture of complex shapes that require tight tolerances. Its versatility also makes it an ideal choice for the production of a variety of parts. For more information, read on:
Process
The Process of Compression Molding is a method for manufacturing bonded Nd permanent magnets. During the molding process, several materials are injected into the mold at the same time. The resulting compound is then cooled and shaped in the mold. This process eliminates secondary processes, including material scrap and inspection, and allows the manufacturer to save on labor and capital equipment costs. The Process of Compression Molding is also adaptable to automation.
Once the product is molded, the process of ejection begins. This phase limits the geometry of the product. This phase makes it challenging to produce products with threads, holes, or grooves. Typically, the process is manual, but can be automated as well. Vibration tumbling is another option. De-flashing determines whether the component is vertical or horizontal. It also depends on the geometry of the parting line.
Materials
The primary consideration in setting compression molding process parameters is material composition. The material choice will determine the pre-heating temperature, molding temperature, blank holder force and cooling rate, among other parameters. Thermoplastics and thermosets are largely similar in chemical and physical properties, but there are differences in the process required to form each type of material. Thermoplastics have higher melting points than thermosets. They also differ in the glass transition temperature.
To produce a high-quality compression mold, the material used in the process must be uniform in temperature and density. The material must be pliable enough to fill the crevices of the mold, resulting in a perfect product. Then, the material is heated and pressed by a hydraulic tool. Unlike traditional injection molding, compression molding produces very few waste materials and is the most economical mass-production method. Some products are ready to use instantly after being injected into a mould.
Process parameters
Compression molding is a highly versatile molding process. Compression temperature, pressure, and mold opening temperature all affect the end product. To optimize production, it is important to understand the process parameters of compression molding. Below are some guidelines that will help you choose the most appropriate process parameters. For maximum results, use an automatic process control system. These automated systems will make adjustments to these processes as necessary. Listed below are the most important compression molding process parameters.
The three key process parameters to consider for compression molding are temperature, pressure, and time of application. Each of these factors affect the end result, so determining the ideal combination of these parameters is essential to optimize your end product. Process experts can help you select the right parameters for your project. Listed below are some of the factors that determine process parameters and how they impact the final product. When choosing process parameters, consider the application process, and contact a compression molding specialist for more information.
Parts produced
When parts produced by compression molding are sized and weight, they are typically a single piece, but they can be made into a range of shapes. For instance, a cylinder can be molded into a cylindrical shape, but a bottle cannot be produced in this manner. The material used in compression molding is generally a thermoset composite, and the most common materials used are Bakelite, polyester, polyurethane, urea-formaldehyde, melamine, epoxy, and alkyd resins. Materials used for this process are selected based on their properties, their associated costs, and the application for which they are produced.
When determining the best material for compression molding, consider the cost of tooling. Plastics are much less expensive than metal, and aluminum can be a great choice. Both processes require cavities and molding tools that are made of different materials. Aluminum and steel are both inexpensive, and molds can be reused, so the cost of tooling is minimal. Additionally, the longer cycle time makes both processes cost-effective, since molds can last a long time.
Labor cost
While both compression molding and injection molding are similar processes, they do not require the same infrastructure. Injection molding involves creating complex molds while compression molding uses simpler molds. This method is preferred when a product must be produced in high volumes. It also allows quick quality assurance checks because the components used are usually inexpensive. Injection molding has a lower labor cost than compression molding, but requires more knowledge about the process. The cost of tools and labor vary with the process.
Compression molding requires the use of heated steel tooling in high-pressure presses. This process produces complex, high-volume parts at high temperatures. Compression molding is also very time-efficient, resulting in reduced labor costs. Nevertheless, the process is not appropriate for all designs. For example, some components are too thin for compression molding. Therefore, companies may want to consider the labor cost of different parts. Further, this process requires less equipment, resulting in lower capital expenditure.
Environmental impact
The environmental impact of compression molding is primarily related to the deterioration of molds and their use in the production of molded parts. The uncured compound used in compression molding processes often picks up dirt particles that then deteriorate the part's surface and creates an unsightly aesthetic appearance. This results in an increased reject rate and poor cosmetic appearance. The following points provide an overview of the environmental impacts associated with compression molding.
Compression molding is often considered a more sustainable manufacturing process than other processes, which may be more expensive. One of the biggest advantages of compression molding is that the process is relatively simple. It does not require expensive molds or complex tooling. In addition, it is also less expensive than other methods because it requires less capital investment and less mold maintenance. Because the process produces thick, uniform parts, it is an excellent option for high-volume production.