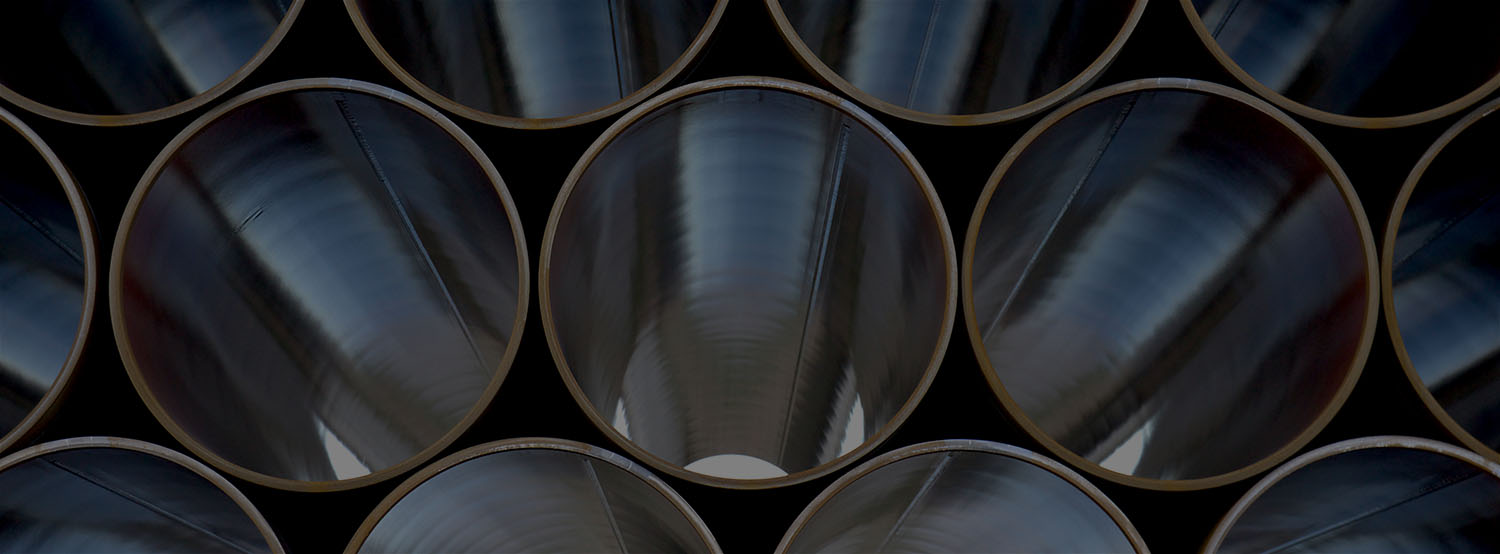
Even while stick welding is widely used, it isn't as common when considering only domestic company. It is still a common welding technique due to its adaptability, simplicity, and convenience of usage. A junction is created by fusing two or more parts together during the fabrication process of welding using heat, pressure, or both. For varied applications, there are numerous welding techniques. The two materials are typically melted together using high heat. Others choose different tactics.
A power supply, a ground connector fastened to the workpiece, a stick holder holding the welding electrode, and the arc created between the stick and the workpiece are all present. Stick Welding Lethbridge may produce excellent welds without the need of gases or regulators. It is far less expensive to start in. As a result of the shielding gas being on the electrode, it is excellent for welding outdoors.
Since the solid wire is made of metal and is devoid of flux, a shielding gas must be used. The wire may also contain silicon, titanium, and manganese in addition to the copper coating that prevents oxidation and rusting. In the process, the wire has multiple uses. It serves as both the joint's filler metal and heat source.
It's crucial to understand that aluminum demands somewhat higher temperatures to produce a high-quality weld when learning to weld. Most aluminum goods are made utilizing AC welding since it is the optimum power source for welders.
Positive and negative pole fluctuations happen quickly when using AC electricity. This reversal in electron flow is referred to as "alternating current" and does not occur with direct current (DC). As previously said, you must manage the degree of polarity balancing when using AC Aluminum Welding Lethbridge equipment.
The wire passes through a copper contact tube (the contact tip), which allows current to flow into the wire. Pulling the trigger causes an arc to form between the wire electrode and the metal being worked on, creating the weld pool.
We must be able to shift the polarity significantly toward the DCEN side. This will often average out to be around 70%. There are certain exceptions to this, such as when the foundation material is oxidized or filthy. If you're working with this kind of material, it's crucial that you have the ability to shift the balance further to the DCEP side so that the workpiece may be cleaned.
Because it needs spotless surfaces and no breeze, indoor spaces are excellent. Without it, the gas shielding will be compromised, permitting reactions and weld flaws.
When aluminum cools off in a factory, a coating of oxide naturally forms on the outside surface. Additionally, handling aluminum can leave pollutants and cleaning oils on the exterior which can be a problem.
Michael Donna is the author of this website and writes articles for a long time. For further details about Stick Welding Lethbridge and Aluminum Welding Lethbridge please visit the website.