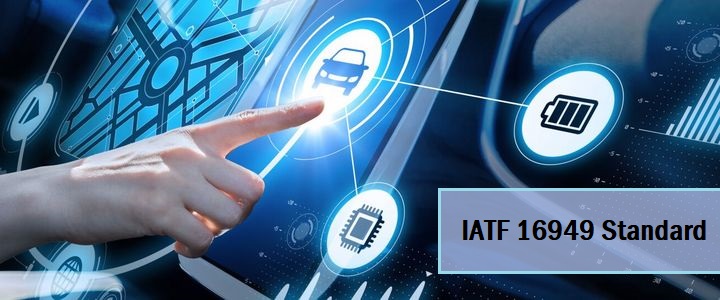
Any organization that adopts IATF 16949 is taking an enormous step forward and certainly facing a significant challenge. Making this choice and putting the standard into practice is difficult, but most of the time, organizations are motivated by client demands or a desire for improvement. It is challenging to show a connection between implementation and a gain in profit unless it is a clear necessity of a client, thus persuading the top management that this is a wise investment might be challenging. The key to securing senior management's approval for the project, if the implementation is an internal corporate initiative, is to outline the advantages that IATF 16949 will have for the business.
The advantages of IATF 16949 cannot be emphasized; organizations of all sizes have certainly benefited from implementing this standard by realizing cost and productivity savings. Here, mention the advantages as well as why they are important are described in detail:
Improvement of organization credibility and image – IATF 16949 has replaced many previously published requirements because it is an internationally recognized standard and has been used as the foundation for Quality Management Systems (QMS) all over the globe. It is frequently a necessity to have a QMS based on IATF 16949 when a business is seeking suppliers. In these situations, obtaining IATF 16949 certification is frequently required. For that, IATF 16949 consultant comes into the picture for support in preparation as well as getting quick certification.
Qualify to supply the automotive industry – It is one of the primary motivations for organizations to obtain IATF 16949 certification. To attract large consumers to the automotive business, an organization must demonstrate that it can produce high-quality, defect-free products, and an IATF 16949 certificate will verify that.
Improvement of customer satisfaction – The quality management principles behind the IATF 16949 criteria is to promote customer satisfaction by anticipating and striving to meet customer needs. The organization will retain more repeat customers if they improve according to their needs and customer satisfaction. That’s why happy consumers are the key to retaining customer loyalty. Furthermore, such customers generate additional money.
Better process integration – By looking at the total process interactions using the IATF 16949 process approach, an organization will be able to more quickly uncover improvements in efficiency and cost savings. This is accomplished by eliminating waste that can occur when processes are maintained without regard for the inefficiencies that can arise during process handoff. Better process flow can also be leveraged to push efficiencies toward fewer errors and resulting reworks, which can increase cost savings.
Improve your evidence for decision-making – The use of evidence-based decision-making is one of the IATF 16949 quality management principles. By making judgments based on evidence rather than "gut feelings," an organization may devote more resources to areas that can enhance efficiencies and increase cost savings, with less trial and error to identify the best solution. Furthermore, by tracking the process organization is improving, the organization will be able to observe how much progress has been made based on the data.
Create a continual improvement culture – One more quality management principle of IATF 16949 is continuous improvement. Adopting this culture to improve the processes and organizational output will result in efficiency and cost savings, including the adoption of systematic processes when problems occur to mitigate the impact of the problem and accelerate recovery. By making this continuous improvement year after year, the organization can reap long-term rewards.
Engagement of employees – Employees who participate in the improvement processes is more contented and more engaged. Who is better to discover opportunities for improvement than the people working on the process, and to help test and develop these improvements once they are implemented? Employees that are engaged are more productive and will help the firm improve and save money, especially if they realize how the quality of the process is dependent on them.