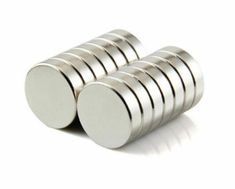
What Are the Properties of NdFeB Pot Magnets?
NdFeb pot magnets are a relatively new type of magnet that has a lot of advantages over other types of magnets like Bonded NdFeB magnets. These include a full density and a relatively simple shape. They are also known to last longer than other types of magnets, which makes them a great option for high-temperature applications.
Source:https://i.pinimg.com
High-energy product (30-50 MGOe), full density, and a relatively simple shape
The high-energy product is a term frequently used when discussing the performance of a magnet. It refers to the smallest magnetic volume needed to generate a given flux density. There are several ways to achieve this. One of the most common methods is to produce the magnet using chemical synthesis. Another method involves a relatively simple sintering process.
For a permanent magnet, the high-energy product is most likely to be achieved through the use of a rare-earth compound. In fact, all current magnets with this attribute are based on a rare-earth compound. However, these compounds have a number of limitations, including limited thermal stability.
On the other hand, magnetic nanoparticles have been receiving a lot of attention recently. These particles are ideal building blocks for future magnets, with the ability to offer high energy density and thermal stability. They can be used to build thin film magnets, bonded magnets, or consolidated magnets.
A recent study of Nd-M alloys suggests that they can serve as grain boundary diffusion sources. This may have an impact on their magnetic properties. Several investigations have been conducted, and coercivity enhancement was seen for most alloys. As a result, it is possible to produce useful magnets by combining ferrite powder with a polymer.
Although this study focused on Nd-M alloys, there is potential for making useful magnets from Sr or Ba ferrite powder. Bonding these powders to polymers or natural rubber produces a magnetic composite that can offer a range of useful magnet properties.
The neodymium-iron-boron (NdFeB) magnet is an excellent candidate for high-energy products. It is known as the strongest magnet material, but it is also subject to corrosion and mechanical brittleness. Therefore, care should be taken when handling it.
A recent study suggests that a Co nanowire with an average length of 200 nm can produce an impressive room-temperature coercivity of 10.3 kOe. Furthermore, a scanning transmission electron microscope (TEM) image of the sample shows that it contains a nonferromagnetic intergranular phase.
Regardless of the specific materials, the high-energy product is most likely derived from a number of factors, including the crystalline structure, shape, and morphology of the magnet such as Alnico magnets. Compared to rare-earth compounds, it is unlikely that the energy product would exceed 5.5 kJ/m3.
Source:https://i.pinimg.com
Resist demagnetization
NdFeB pot magnets have a high resistance to demagnetization. This means that they can be used for a variety of applications. In fact, NdFeB is one of the most common types of permanent magnets. These are typically used in the home and in many industrial applications.
They are made from an alloy of Iron and Neodymium. The atoms of Neodymium have a very high saturation magnetization. During the manufacturing process, the spins of four unpaired electrons in the neodymium atoms will align with the same direction. However, once the magnet is exposed to an external magnetic field, the neodymium atoms lose their ferromagnetism.
The temperature at which the neodymium magnet loses its ferromagnetism is called the Curie temperature. For neodymium magnets, this is usually around 220 degrees Celsius. When the temperature exceeds this, the magnet becomes completely demagnetized.
Demagnetization can be caused by a variety of factors. These include shock, temperature, and mechanical disturbance. If the magnet is a very thin one, the irreversible losses can occur at temperatures lower than the maximum working temperature. Depending on the environment, it may be advisable to use an alternative magnet.
Neodymium magnets are the strongest and most powerful types of permanent magnets available in the market. However, they are also slightly more expensive than other types of magnets. Besides, they do not have the same degree of corrosion resistance as samarium-cobalt magnets.
If you are interested in using NdFeB pot magnets, you should know the minimum recommended operating temperatures of each grade. You should also understand how to measure the flux permeance of the material. Using this measurement, you can find out the number of maxwells per gilbert that the magnet can resist.
In order to avoid demagnetization, you should make sure that the NdFeB magnet such as Sintered NdFeB magnets is not exposed to a strong magnetic field. It should also not be placed in a corrosive environment. Especially, if you will be working in a marine environment, it is a good idea to choose an alternative material.
In addition, you should know that neodymium magnets can be damaged by radiation. This is because the neodymium metal is a component of a rare-earth metal.
Last longer than other magnets
If you want your NdFeb pot magnets to last longer, you need to take care of them. They should be protected from strong external magnetic fields, and not be exposed to too much heat. You should also make sure that they aren't subjected to radiation.
Neodymium magnets are known to be the strongest permanent magnets available. However, their corrosion resistance is relatively poor. It is important to remember that they should not be stored in an environment where they will come into contact with strong acid or alkali. In addition, they should be covered with a protective coating, or else they could become corrosive.
Alternatively, you can use a different type of magnet for your application. These include zinc plus rubber, encasing, or even a steel plus rubber combination. However, if you want to avoid corrosion, you should always select a permanent magnet that is constructed from a solid neodymium core.
Another option is to use a neodymium pot magnet. These are usually used for heavy-duty holding and fixing, and they can also be fitted with hooks or fasteners.
There are many types of neodymium pot magnets, with each one having a different adhesive force. You can also choose between a deep pot magnet or a shallow pot magnet. Deep pot magnets are designed with a permanent magnetic core. The magnetic cores are made of neodymium or samarium-cobalt. They have brass or stainless steel housings and are suitable for mechanical engineering, electrical technology, or tool making. Shallow pot magnets are commonly used in the metalworking industry, and are also made with a permanent magnetic core.
KIPP deep pot magnets are used in the automotive and electrical technology industries. Various designs are available, including round and square deep pot magnets with Neodymium or Samarium-Cobalt magnetic cores. Some models are also available with machined magnetic faces.
Neodymium pot magnets with internal threaded stems are very powerful mounting magnets. They can hold up to 250 pounds. A screw-on type magnet with a female thread is also available.
Moreover, you can customize the NdFeB pot magnets for the desired adhesive force and holding power. Deep pot magnets are usually used for mounting or fixing, and are ideal for industrial applications.
Suitable for high-temperature applications
Most high-temperature applications require a specific type of resistive material. For these applications, the type of material can make a huge difference in how well the circuit performs. Knowing the characteristics of each type can ensure you make the right choice.
The most common types of resistive material for high-temperature applications include thin film and formed metals. Thin film resistors are manufactured using a process where a metal is deposited onto a ceramic substrate. These materials have a variety of advantages. They can be manufactured to a wide range of temperatures and can be sold in a variety of package configurations.
High-temperature composites using polymer matrices have become more widespread in recent years. These composites combine low weight, high strength, and excellent electrical insulation.
Polymer matrices are made from a variety of materials, including liquid crystalline polymers and bismaleimides. Recent advances in processing technology and improved performance have made these materials more practical. Using polymer matrices for high-temperature applications has led to a number of innovations. In particular, new fillers have been developed for these types of applications.
The thick-film resistor has gained significant attention as a possible solution for high-temperature applications. It is produced by firing at a high temperature. This is then followed by the depositing of a metal and particles on the ceramic substrate. After a certain period of time, the metal/particles form a conductive cermet matrix with Axial Flux Permanent Magnet Generator.
A common thick-film conductor formulation for high-temperature use is platinum-silver. This material has a number of advantages, including the low forward voltage drop and the high metal semiconductor barrier. However, its disadvantage is the increase in leakage current.
Another type of resistor that is suitable for high-temperature applications is the metal-strip resistor. These resistors can be made in a variety of sizes and terminations. Metal-strip resistors are typically encapsulated, and are often combined with a glass insulator for environmental protection.
Other types of resistors for high-temperature applications include composition resistors and foil resistors. While these resistors have a low cost, they are less suitable for precise applications.
Finally, high-temperature insulators are also a viable option. They offer a combination of good vibration dampening, mechanical strength, and low thermal conductivity.