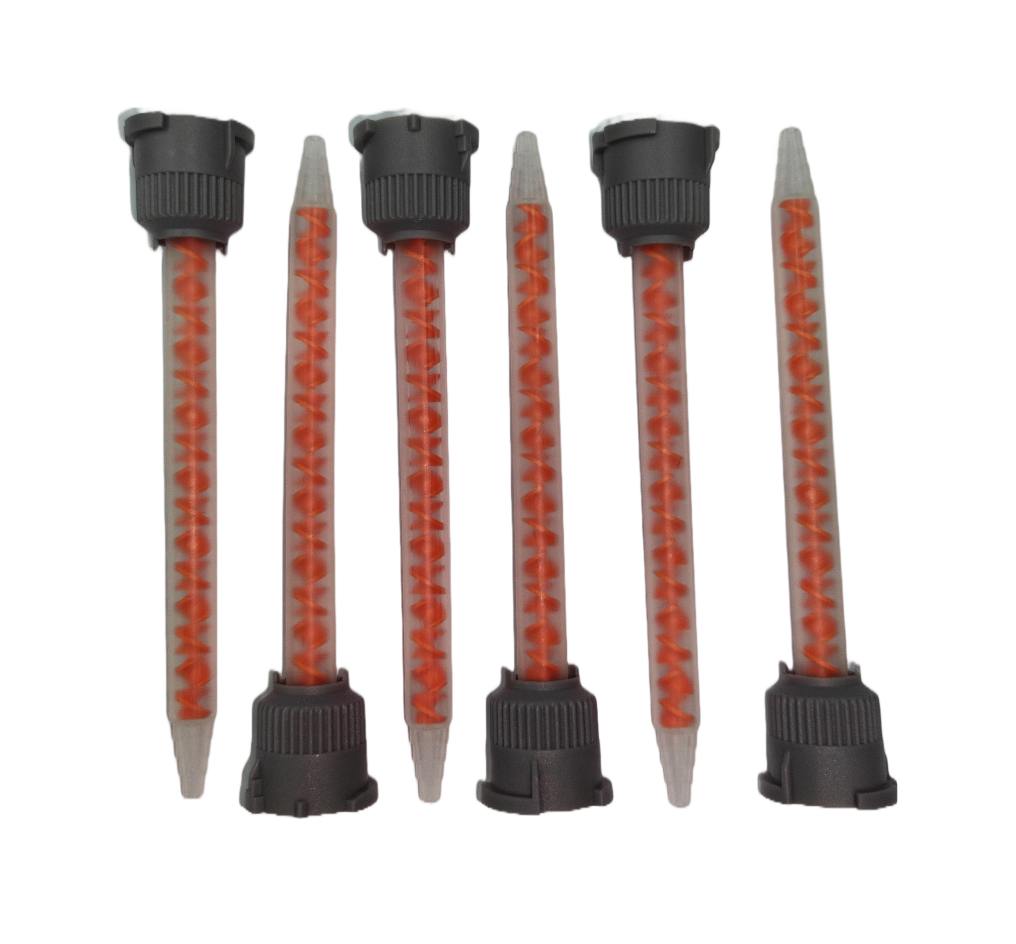
In various industrial sectors, achieving consistent and thorough mixing of fluids or components is of utmost importance. Traditional methods relying on mechanical agitation have their limitations, prompting the development of alternative solutions. Enter static mixing nozzles, innovative devices that have revolutionized the field of fluid blending. In this article, we will explore the concept, features, applications, and benefits of static mixing nozzles, highlighting their role in enhancing precision and efficiency in mixing processes.
Understanding Static Mixing Nozzles:
Static mixing nozzles are specialized devices designed to facilitate the efficient blending of two or more components without the need for external agitation. Unlike mechanical mixers, static mixing relies on the energy of fluid flow to induce thorough mixing. These nozzles consist of intricate geometrical elements or channels that divert and redirect the fluid stream, promoting turbulent flow and intermingling of the components.
Geometric Designs:
Static mixing nozzles come in various geometries, each tailored for specific applications. Helical elements, with their twisted and intertwined channels, are commonly used to induce fluid folding and intermixing. Another popular design is the square static mixing nozzle, featuring multiple intersecting channels that create a complex matrix for intense blending. Each geometry offers unique characteristics and advantages based on the desired mixing outcomes.
Applications:
Static mixing nozzles find applications in a wide range of industries and processes. They are commonly used in chemical processing, adhesives and sealants manufacturing, water treatment, pharmaceutical production, food and beverage processing, and many more. Static mixing nozzles can effectively mix liquids, gases, and even viscous materials, making them versatile tools in diverse industrial settings.
Advantages of Static Mixing Nozzles:
a. Enhanced Mixing Efficiency: Static mixing nozzles provide efficient and uniform blending by maximizing fluid contact and promoting thorough mixing in a shorter timeframe.
b. Precise Ratios: These nozzles enable accurate and consistent mixing ratios, ensuring the desired proportions of components are maintained throughout the process.
c. Reduced Waste: By achieving more efficient mixing, static mixing nozzles minimize material waste and enhance process sustainability.
d. Simplified Equipment: The use of static mixing nozzles eliminates the need for external agitators or mixing equipment, simplifying the setup and reducing maintenance requirements.
e. Scalability: Static mixing nozzles can be adapted to different flow rates and volumes, allowing for scalability in various production scenarios.
Material Compatibility:
Static mixing nozzles are available in different materials, such as stainless steel, polypropylene, PVC, and more. The choice of material depends on factors such as chemical compatibility, temperature resistance, and application requirements. Various material options make it easier to find a static mixing nozzle suitable for specific industrial processes.
Customization and Integration:
Manufacturers offer a wide range of static mixing nozzles with customizable features, including size, connection types, and additional accessories. This allows for seamless integration into existing equipment and enables tailored solutions for specific applications.
Conclusion:
Static mixing nozzles have significantly transformed the field of fluid blending, offering precise and efficient mixing solutions across a multitude of industries. Through their innovative geometries and reliance on fluid dynamics, static mixing nozzles ensure consistent and thorough blending without the need for external agitation. The advantages they offer, such as enhanced mixing efficiency, accurate ratios, reduced waste, and simplified equipment, make them indispensable tools in modern manufacturing processes. With their versatility, scalability, and customizable options, static mixing nozzles continue to play a crucial role in improving precision and efficiency in mixing operations.