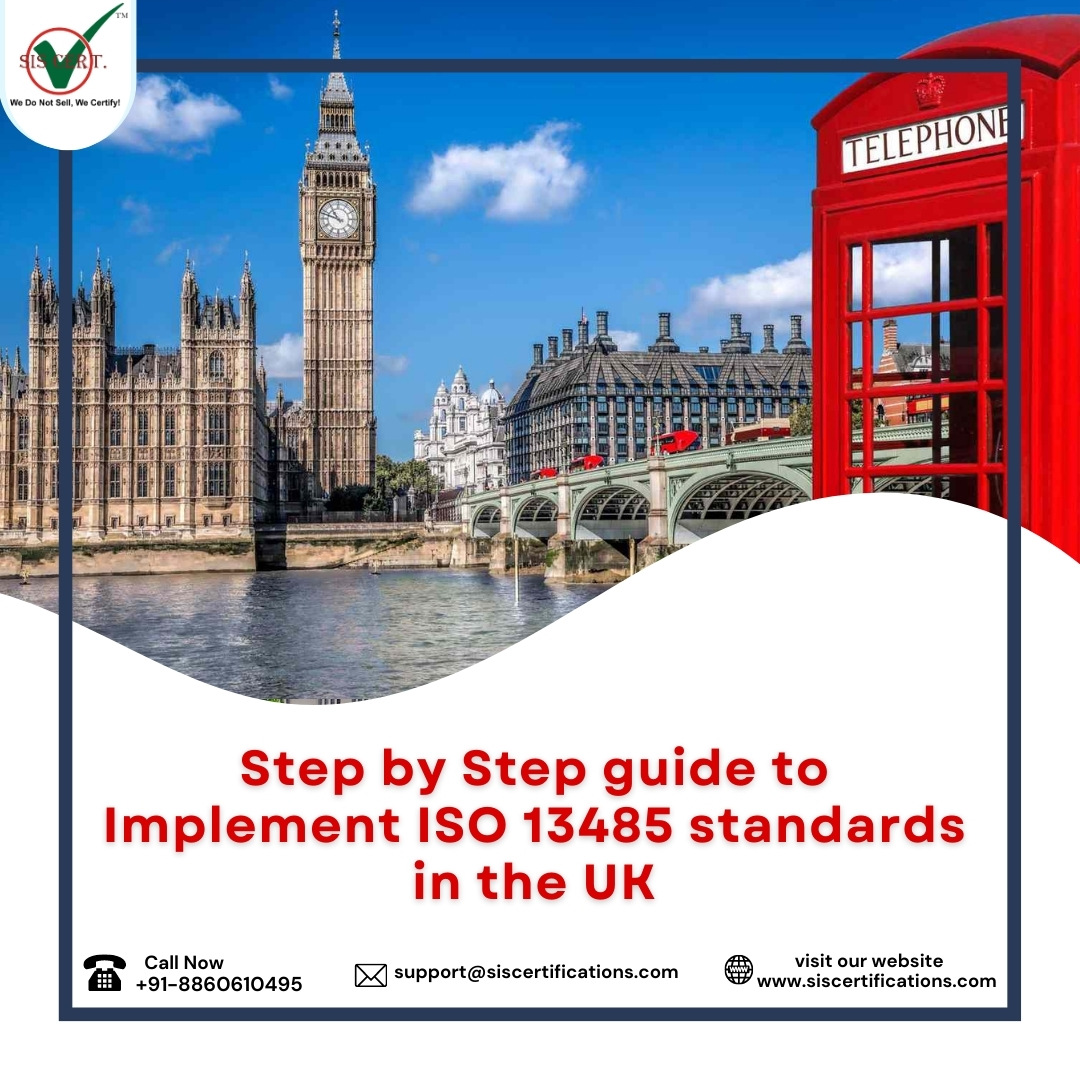
Implementing ISO 13485 standards in the UK involves a systematic approach to ensure compliance with the requirements for a quality management system for medical devices. Below is a step-by-step guide to help you through the process:
Understand the Standard: Familiarize yourself with the ISO 13485 standard to comprehend its requirements fully. This will help you prepare for the implementation process and identify gaps in your current system.
Commitment from Top Management: Get buy-in and commitment from top management to ensure that the implementation process receives the necessary resources and support.
Gap Analysis: Conduct a gap analysis to identify the areas where your current quality management system differs from the ISO 13485 requirements. This analysis will form the basis of your implementation plan.
Form an Implementation Team: Create a dedicated team responsible for the implementation. This team should have representatives from different departments, including quality, regulatory affairs, R&D, production, and other relevant stakeholders.
Create an Implementation Plan: Develop a detailed plan that outlines the steps, responsibilities, and timeline for achieving ISO 13485 compliance.
Document Control and Management: Implement a robust document control system to manage all documentation required by the standard. This includes policies, procedures, work instructions, and records.
Training and Awareness: Ensure that all employees are aware of the ISO 13485 requirements and receive appropriate training on the quality management system and their specific roles in maintaining compliance.
Risk Management: Implement a risk management process as required by ISO 14971 to identify and mitigate risks associated with medical devices.
Product Realization: Establish procedures for product realization, including design and development controls, verification, validation, and product release processes.
Supplier Management: Implement a supplier control system to ensure that all suppliers and contractors providing products or services related to medical devices meet ISO 13485 requirements.
Validation and Monitoring: Conduct validation activities and implement a system for monitoring and measuring processes to ensure their effectiveness and compliance with ISO 13485.
Corrective and Preventive Actions: Develop a system for handling non-conformities, implementing corrective actions to address issues, and taking preventive actions to avoid potential problems.
Internal Audits: Conduct regular internal audits to assess the effectiveness of your quality management system and identify areas for improvement.
Management Review: Organize management reviews to evaluate the performance of the quality management system and make necessary changes to ensure its continuous improvement.
Obtain Certification: Once you believe your quality management system is fully compliant with ISO 13485, engage an accredited certification body to conduct an external audit and grant you the ISO 13485 certification.
Maintain and Continuously Improve: ISO 13485 compliance is an ongoing commitment. Continuously monitor and improve your quality management system to meet the evolving needs of the medical device industry and regulatory requirements.
Remember that each organization's implementation process may vary based on its size, complexity, and existing quality management practices. Seek professional guidance if needed, and be prepared to adapt the steps according to your unique situation.