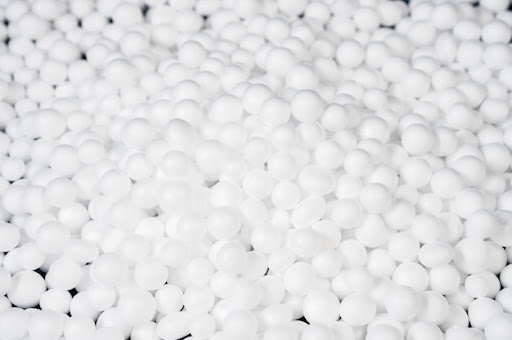
In the world of plastics manufacturing, innovations continue to drive efficiency and cost-effectiveness. One such innovation is the use of Calcium Filler Masterbatch, a game-changer that offers a range of benefits to plastic manufacturers. This article explores the advantages of incorporating Calcium Filler Masterbatch into plastic production processes, shedding light on how it can enhance the final product's quality and the bottom line.
Enhanced Cost Efficiency:
- Calcium Filler Masterbatch primarily comprises calcium carbonate, a cost-effective and abundant mineral.
- Using Calcium Filler Masterbatch, plastic manufacturers can significantly reduce the consumption of expensive polymer materials while maintaining product quality.
- This cost-efficient approach contributes to higher profit margins and a competitive edge in the market.
Improved Mechanical Properties:
- Calcium Filler Masterbatch enhances the mechanical properties of plastics, such as tensile strength, stiffness, and impact resistance.
- Including calcium carbonate particles reinforces the plastic matrix, making it suitable for applications that require durability and strength.
Reduced Environmental Impact:
- Incorporating Calcium Filler Masterbatch reduces the reliance on virgin polymer materials, which are derived from Petrochemical Sources.
- This eco-friendly alternative decreases the carbon footprint of plastic production and promotes sustainability by utilizing readily available natural resources.
Enhanced Processing Stability:
- The addition of a Calcium Filler Masterbatch improves the processing stability of plastics during extrusion, molding, and other manufacturing processes.
- The consistent dispersion of calcium carbonate particles helps prevent issues like melt fracture and reduces processing downtime.
Controlled Shrinkage and Warpage:
- Calcium Filler Masterbatch helps control plastic products' shrinkage and warpage tendencies during cooling and solidification.
- This results in more accurate dimensional stability, especially in applications where precise measurements are critical.
Opportunities for Lightweighting:
- Lightweighting is a strategy aimed at reducing the weight of plastic products without compromising their performance.
- Calcium Filler Masterbatch enables plastic manufacturers to achieve light-weighting goals by maintaining structural integrity while using fewer polymer resources.
Improved Heat Resistance:
- Calcium carbonate possesses excellent heat-resistant properties.
- By incorporating Calcium Filler Masterbatch, plastic products become better equipped to withstand high-temperature environments without losing their integrity.
Versatility in Applications:
- Calcium Filler Masterbatch is versatile and can be tailored to suit various plastic applications, from packaging materials to automotive components.
- This adaptability expands the scope of industries that can benefit from its usage.
Reduced Material Costs:
- One of the key attractions of using Calcium Filler Masterbatch is its ability to reduce material costs effectively.
- The cost savings achieved by replacing a portion of polymer with calcium carbonate can be substantial over the long term.
Also read: CALCIUM FILLER MASTERBATCH: Information That You Should Know
Conclusion:
Incorporating Calcium Filler Masterbatch into plastic manufacturing processes brings many benefits that can significantly impact product quality and cost-effectiveness. The advantages are numerous, from improved mechanical properties to reduced environmental impact and enhanced processing stability. Manufacturers looking to optimize their plastic production processes, increase profit margins, and contribute to a more sustainable industry should consider embracing Calcium Filler Masterbatch as an essential tool in their toolkit.
For more insights into the world of plastic innovations and manufacturing, visit Kandui. As a platform dedicated to promoting knowledge and advancements in the plastics industry, Kandui provides valuable resources for manufacturers, researchers, and enthusiasts alike.