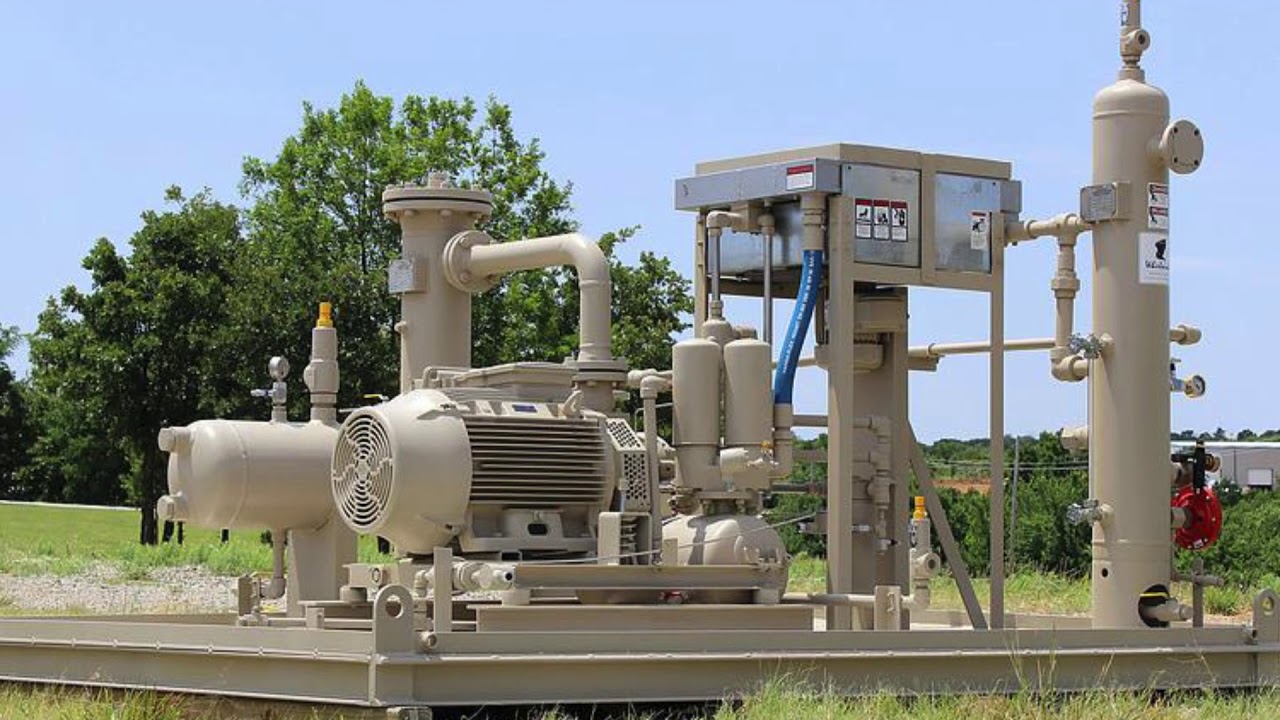
Vapor recovery units (VRUs), also commonly referred to as vapor recovery systems, are industrial pollution control devices that capture hydrocarbon vapors that would otherwise escape during the transfer and storage of volatile liquids like petroleum and related products. By capturing these hydrocarbon vapors, VRUs help reduce air pollution and prevent waste. This article discusses the importance of VRUs, how they work, key components, types of systems, and their applications.
VRUs play a crucial role in reducing air pollution from volatile organic compounds (VOCs) emitted during the transfer and storage of fuels and petroleum products. These VOCs include hazardous air pollutants like benzene that can have harmful health impacts if released untreated. Capturing these vapors with VRUs prevents them from escaping into the atmosphere.
In addition to protecting air quality and public health, VRUs help facility operators reduce product loss that would occur from evaporation and leakage during normal operations. By recapturing the vapors, the liquid products can be transferred more efficiently with little waste. Properly functioning VRU systems can recover 95% or more of hydrocarbon vapors. This recovered hydrocarbon vapor can then be returned to the storage tank or facility pipeline.
How Vapor Recovery Units Work
The basic components and functionality of vapor recovery units is fairly standardized across different models and manufacturers. During the loading or unloading of tanker trucks, railcars, marine vessels or other transport equipment, the VRU system captures hydrocarbon vapors displaced through either an upward or downward vapor flow.
Common elements include a vapor collection header which routes the displaced vapors, a blower or compressor to pull the vapors into the system, piping to transport the vapors, and sometimes an absorber tower where any final separation occurs before returning or incinerating the recovered vapors. Sensors monitor the transfer operation and turn the vapor recovery system on automatically when product transfer begins. The compressed vapors are then either routed back to the storage vessel being filled or to a co-located vapor processing system.
Types of Vapor Recovery Systems
There are two main types of vapor recovery systems - static and dynamic. Static vapor recovery systems rely on atmospheric pressure and absorption or adsorption to capture displaced vapors without the use of blowers or compressors. Dynamic vapor recovery systems actively induce a vacuum using blowers or compressors to pull hydrocarbon vapors from the vapor space into the recovery piping system.
Within these two broad categories, there are also variations depending on the specific facilities and applications. Some common dynamic vapor recovery unit configurations include balanced systems, assist systems, and vacuum-assist systems. Balanced systems use a single blower to balance vapor and liquid transfer pressures while assist systems use smaller blowers to aid the natural vapor flow.
There are also systems tailored for specific applications like marine vessel loading, storage tank degassing, and others. Proper system selection depends on factors like throughput volumes, facility layout, product characteristics, and regulatory requirements.
Applications
Vapor Recovery Units are found across many industries that involve the transfer and storage of volatile organic liquids. Some common applications of VRU systems include:
- Petroleum product terminals: Used for loading tanker trucks and railcars receiving gasoline, diesel, jet fuel and other petroleum products.
- Refineries: Capture displaced vapors during marine vessel loading, pipeline transfer and storage tank activities.
- Chemical plants: Recover vapors from chemicals with high vapor pressures like certain solvents.
- Oil and gas production: Capture vapors at well sites, tank batteries and along midstream pipelines.
- Landfill gas: Collect methane and other landfill gases to be used for energy generation or combustion.
- Wastewater treatment: Capture volatile organic compound emissions from wastewater treatment processes.
Properly designed and maintained VRUs are crucial pollution control equipment across many industrial sectors that involve volatile organic liquid transfers to help recover product, reduce emissions and comply with air quality regulations.
Key Considerations for Vapor Recovery Systems
When specifying, installing and operating vapor recovery units, several factors must be considered to ensure optimal performance over the long run:
- Component Selection: Choosing blowers, piping, sensors and other hardware rated for the chemical composition and throughput volumes involved.
- Preventive Maintenance: Strict adherence to maintenance plans like filter changes helps prevent breakdowns and leaks.
- Monitoring: Installation of instrumentation allows remote monitoring of operations and leak detection.
- Recordkeeping: Thorough documentation of performance metrics, maintenance activities and any issues that arise.
- Operator Training: Educating personnel on safe and proper operation is essential to prevent accidents.
- Emissions Verification: Regular testing ensures systems continuously meet emissions reduction goals.
- Regulatory Compliance: Understanding and fulfilling all applicable local, state and federal air quality rules.
Careful attention to design, maintenance and compliance helps vapor recovery units function as intended to minimize VOC emissions and product losses over many years of service.
Get More Insights Here
https://www.pressreleasebulletin.com/vapor-recovery-units-revolutionized-industries/