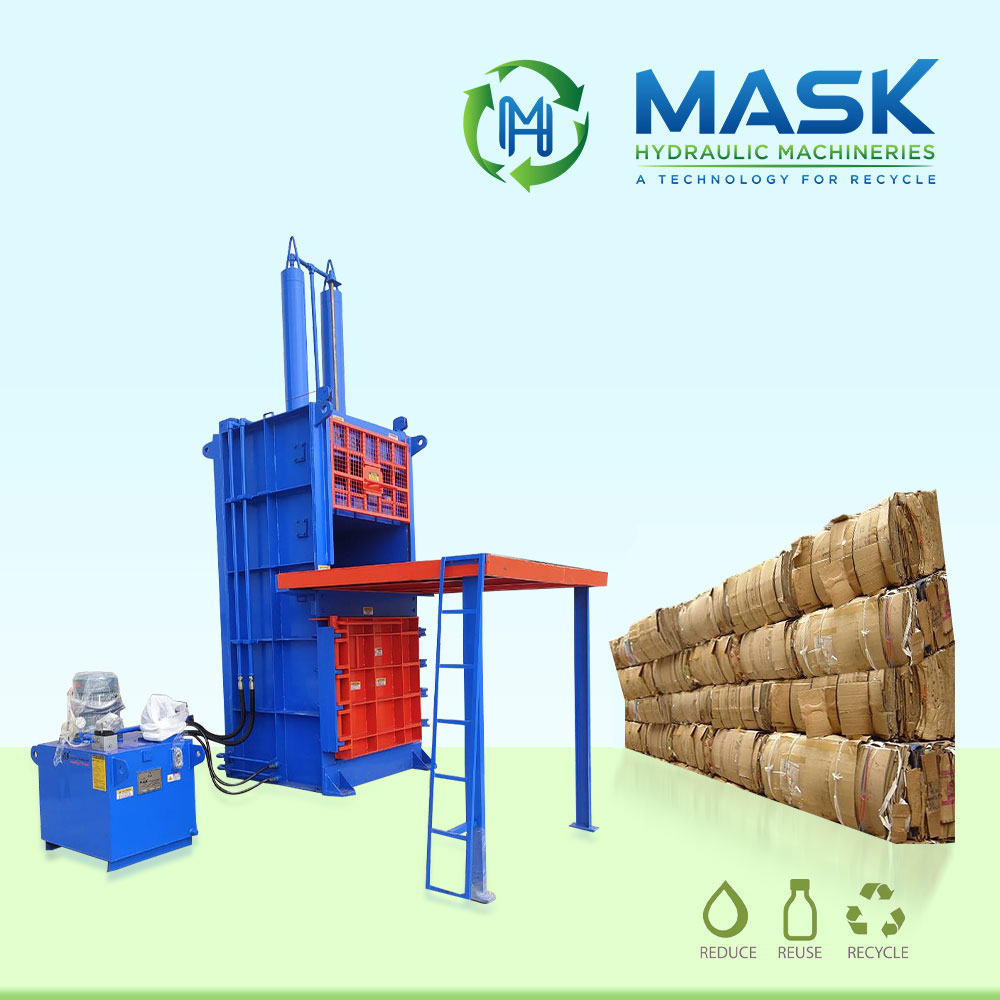
Hydraulic balers are machines used in waste management and recycling industries. They play a crucial role in compressing and packing various recyclable materials like cardboard, plastics, metals, and paper. These machines utilize hydraulic pressure to create dense, manageable bales that are easier to handle, transport, and recycle. Here’s a comprehensive look at How hydraulic baler works, their components, and their operational process.
Components of a Hydraulic Baler
Hydraulic System: This is the core of the baler, comprising a hydraulic pump, fluid reservoir, valves, and cylinders. The system uses hydraulic fluid to generate pressure and drive the compression process.
Bale Chamber: The area where the material is loaded and compressed. It is designed to withstand high pressure and is often lined with hardened steel to prevent wear.
Platen/Ram: A heavy, flat surface attached to the hydraulic cylinder. The platen moves up and down (or side to side in some designs) to compress the material within the chamber.
Control System: A set of controls and sensors that manage the baler’s operation. Modern balers often feature programmable logic controllers (PLCs) for precise control.
Bale Tying Mechanism: This includes various methods such as wires, strapping, or twine to tie and secure the compressed bales.
Feed Opening: The opening through which materials are loaded into the bale chamber. This can be a manual feed door or an automated conveyor system.
Operational Process
Loading: The process begins with loading the recyclable material into the bale chamber through the feed opening. Depending on the design, this can be done manually or via an automated conveyor belt.
Compression: Once the chamber is adequately filled, the operator activates the hydraulic system. The hydraulic pump pushes fluid into the cylinder, causing the ram to move. The ram exerts a force on the material, compressing it against the chamber walls. The pressure continues to build until the material is densely packed.
Pressure Maintenance: During compression, the hydraulic system maintains consistent pressure to ensure the material is adequately compacted. Sensors monitor the pressure levels to prevent overloading and potential damage to the machine.
Tying: After compression, the bale needs to be secured. Depending on the baling machine type, this can involve manually threading wires or an automated system that ties the bale with wire, plastic, or twine. This step is crucial to maintain the bale’s integrity during handling and transportation.
Ejection: Once tied, the bale is ejected from the chamber. Some balers have automatic ejectors that push the bale out, while others may require manual intervention. The bale is now ready for transport and further processing.
Types of Hydraulic Balers
Hydraulic balers come in various types, each suited for specific applications:
Vertical Balers: These are often used in retail and smaller recycling operations. They require less floor space and are typically manually operated.
Horizontal Balers: Ideal for larger operations, these balers offer higher capacity and can be semi-automated or fully automated. They handle larger volumes of material and are suitable for continuous operation.
Auto-Tie Balers: These advanced balers automatically tie the bales after compression, increasing efficiency and reducing labor costs.
To Finish
Hydraulic balers are recycling equipments that transform loose recyclable materials into dense, manageable bales. These machines efficiently compress various materials by leveraging hydraulic pressure, making them easier to handle, transport, and recycle. Businesses can choose the one that best suits their operational needs as there are different types of balers available including customized options.