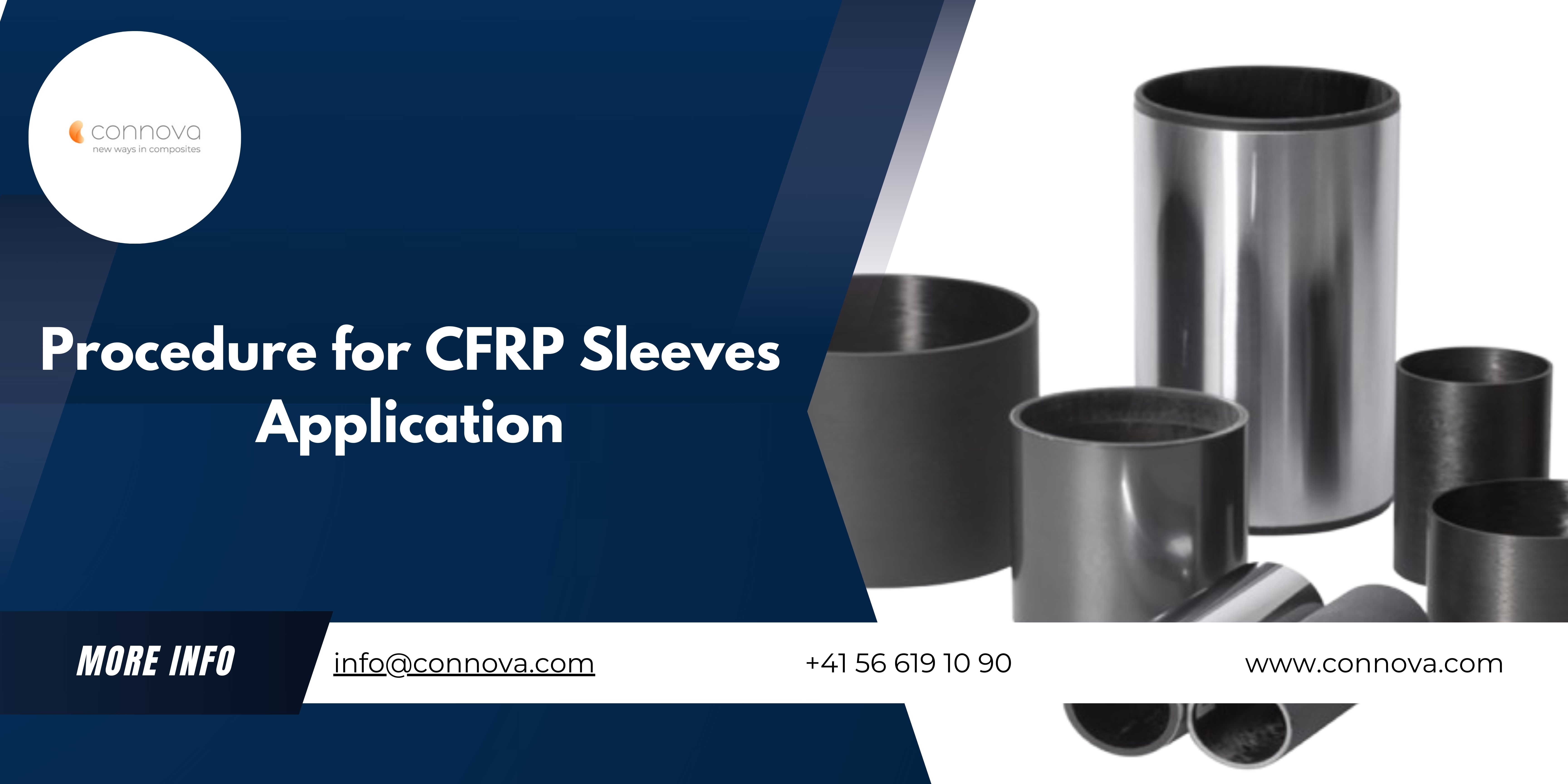
Carbon Fibre Reinforced Polymer Sleeves have today become an integral aspect of the world of electrical motors today with added durability, improved performance, and a lesser degree of weight. These sleeves are recognized across the globe for their defined strength in reinforcing and protecting motor components in ensuring long-term reliability and unwavering efficiency. The following guide steps you through applying CFRP sleeves to electric motor components in a manner that follows best practices to get the best possible results.
1. Pre-treatment of the Motor Component
For the application of a CFRP sleeve, the motor component should first be equally pretreated. By equally pretreated, one means cleaning and inspecting the surface to ensure it is totally free of any contaminants that are likely to affect the process of adhesive bonding.
Pretreatment Steps:Pretreatment Steps:
Cleaning: Clean the motor component effectively in a solvent. Ensure that the surface is completely rid of dirt, grease, and other contaminants.
Inspection: The component must be checked for damages or wear on its part; if such are found, these defects should be addressed or the part replaced before advancing.
Surface Roughening: Mildly roughen the area to be adhered with fine-grit sandpaper. This enhances the bonding surface, which will help the CFRP sleeve hold more effectively.
Final Cleaning: After roughening, clean the surface once again and get rid of dust and debris that could have been built up or created from the sanding.
2.Measurement and Cutting of the CFRP Sleeve
The second procedure should be taking an accurate measurement and cutting that CFRP sleeve with respect to the motor part. This activity is very crucial because if done correctly, it will ensure that all components fit precisely and are perfect in performance.
Measuring and Cutting:
Measurement: Measure in circles and length enough to cover the motor part through the CFRP sleeve. Ensure that there are some offsets by the use of the shrinkage overlapping.
Cutting: Since the measurements have been done, cut the CFRP sleeve at the desired size with the aid of a sharp cutting tool. Make sure the edges are clean and of a straight nature to avoid any catch during the application process.
Dry Fit: Make a dry fit by just laying the cut CFRP sleeve on the motor component before proceeding. This is to preview the final component shape; this way, touch-up, and fine-tuning are easily done before bonding.
3.Application of Adhesive
The adhesive is a very important factor in CFRP sleeve adhesive bonding to the motor component. The selection and application of the adhesive are very crucial to provide a high-strength, durable bonded interface.
Adhesive Steps:
Selecting the Adhesive: The adhesive should be compatible with both the CFRP sleeve and the material used in the motor's construction. Epoxy resins are most commonly used. It is due to its incredibly strong bond and durability.
Mixing: If it is a two-part type, it needs to be mixed as per the manufacturer's guidelines.
Applying: A thin and uniform adhesive layer should be applied over the component of the motor using a brush or roller. Care must be taken during its application, meaning that it should be applied to the entire surface that will have the CFRP sleeve.
Air Bubble Free: Prevent the adhesion from developing air bubbles while applying, as that will affect the adhesive qualities and therefore the performance of the CFRP sleeve bond.
4.CFRP Sleeve Installation
After the adhesive has been applied, the CFRP sleeves are installed onto the motor component. This operation has to be carried out carefully and accurately.
Installation Steps:
Alignment: Slide the CFRP sleeve over the motor component from one end to the other; do so carefully, ensuring that the sleeve is placed without torsion and wrinkles.
Smoothing: While applying the CFRP sleeve, one should make it smooth using their bare hands or rolling tool so that the whole area comes in contact with the adhesive. It helps to remove air pockets and eventually forms a good bond.
Overlap: If the CFRP sleeve has overlapped, then see if it is even and secure. Extra adhesive can be used for bond formation at an overlapping area.
Curing Steps:
Temperature and Time: Curing temperature and time shall be as per the manufacturer's recommendation. In general, the adhesive shall cure faster at a higher temperature, although this depends on the requirements of the adhesive and materials of the motor component.
Running Check: Every now and then, check the curing of the adhesive to ensure that the setting of the adhesive takes place uniformly. At this time, the CFRP sleeve should not be disturbed either, so that misalignment or weak spots do not occur.
5.Final Inspection and Finishing
Once the adhesive properly cures, the application of the CFRP sleeve is nearly complete. The final few steps are the inspection and necessary finishing.
Steps for Final Inspection and Finishing:
Inspection: Observe the CFRP sleeve for possible defects, e.g., air bubbles, wrinkles, or misalignment. Correct discrepancies as early as possible.
Cutting: Trim away if any part is in excess using a sharp knife or scissors. Silenced the edges with the component through the motor.
Surface Treatment: Depending on the need, it can be required to conduct a surface treatment such as a protective coat or paint on the CFRP sleeve. This will safeguard the sleeve from a number of matters and publicize it so its appearance and service life are maintained.
6.Testing and Validation
The last stage of the process is testing and validating its performance. This is to ensure proper bonding of the sleeve, after which it can be put into use for operational purposes.
Testing and Validation Steps:
Operational Testing: The component motor is to be operated to check if the CFRP sleeve performs as modeled. Monitor some signs of slip, run-out, or other defect signs.
Validation: When the motor component is part of a larger system, validate the functionality of the whole system with the CFRP sleeve already attached to the motor.
Conclusion
The application of CFRP sleeves in electric motor components is a very precise process and it usually requires good attention to detail every step of the way. Preparation, measurement, installation, and curing are all processes that are crucial to the result already from the application stage. Just follow these step-by-step instructions to make your electric motors stronger, and more durable and thus serve you for longer.
With the focus on quality CFRP sleeves and robust application processes, think of Connova AG, your number-one address for high-tech carbon fibers with ultimate performance. Development and innovation as well as top-quality priority to achieve the most sophisticated outcomes in the applications.