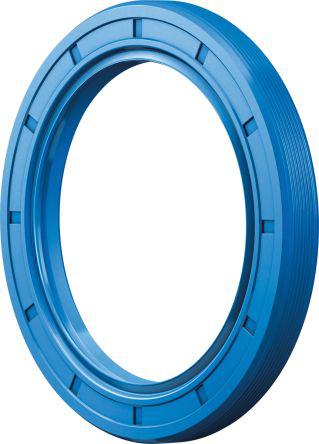
Seals play a crucial role in a wide range of industrial applications, ensuring the safety, efficiency, and longevity of machinery and components. Whether in manufacturing, automotive, aerospace, or marine industries, seals are indispensable for preventing leaks, maintaining pressure, and safeguarding equipment from environmental factors. This blog delves into the significance of seals, their types, applications, and why they are vital for any industrial setup.
Understanding the Importance of Seals in Industrial Settings
Seals are designed to prevent fluid, gas, or solid contaminants from escaping or entering a system. Their primary function is to maintain the integrity of the components they protect, ensuring that machinery operates smoothly and efficiently. Without seals, the risk of leaks, contamination, and equipment failure would be significantly higher, leading to costly downtime and repairs.
- Prevents Leakage: Seals are crucial in preventing leaks of fluids, gases, or oils, which can lead to malfunctions or accidents.
- Maintains Pressure: In hydraulic or pneumatic systems, seals help maintain the required pressure, ensuring the system operates correctly.
- Protects from Contaminants: Seals act as a barrier against dust, dirt, and other contaminants that could compromise the integrity of sensitive components.
- Enhances Equipment Longevity: By reducing wear and tear, seals contribute to the prolonged life of machinery and equipment.
- Reduces Maintenance Costs: Effective sealing solutions minimize the need for frequent maintenance, reducing overall operational costs.
Types of Seals and Their Applications
Seals come in various types, each designed for specific applications and environmental conditions. Understanding the different types of seals can help in selecting the right one for your industrial needs.
O-Ring Seals
O-ring seals are among the most common and versatile types of seals used in various industries. They are circular in shape and can be made from various materials, including rubber, silicone, and PTFE.
- Applications: O-ring seals are used in hydraulic systems, engines, pumps, and valves.
- Benefits: They provide an effective seal against liquids and gases, are easy to install, and offer a cost-effective sealing solution.
Mechanical Seals
Mechanical seals are used in systems where the rotating shaft passes through a stationary housing, such as in pumps and compressors. They are designed to prevent leaks between the shaft and housing.
- Applications: Mechanical seals are common in pumps, mixers, and reactors.
- Benefits: They offer excellent leakage control, are durable, and can handle high-pressure environments.
Lip Seals
Lip seals, also known as rotary shaft seals, are used to retain lubricants and exclude contaminants in rotary applications. They consist of a flexible lip that contacts the rotating shaft.
- Applications: Lip seals are used in automotive engines, gearboxes, and machinery.
- Benefits: They provide a reliable seal for rotating shafts, are resistant to wear, and can operate in harsh conditions.
Gasket Seals
Gaskets are flat seals that sit between two or more surfaces to prevent leakage of fluids or gases. They are commonly used in flanges, pipe joints, and engine parts.
- Applications: Gasket seals are used in piping systems, engines, and HVAC systems.
- Benefits: Gaskets offer a tight seal, are available in various materials, and can be customized for specific applications.
Hydraulic Seals
Hydraulic seals are specifically designed for high-pressure hydraulic systems. They prevent fluid leakage and maintain pressure within hydraulic cylinders.
- Applications: Hydraulic seals are used in hydraulic cylinders, presses, and machinery.
- Benefits: They provide excellent sealing performance, are resistant to high pressures, and extend the life of hydraulic components.
Key Considerations for Choosing the Right Seal
Selecting the right seal for your application is critical to ensuring optimal performance and longevity. Several factors should be considered when choosing a seal.
- Material Compatibility: Ensure the seal material is compatible with the fluids, gases, or substances it will come into contact with.
- Operating Environment: Consider the temperature, pressure, and exposure to chemicals or contaminants in the operating environment.
- Seal Type: Choose the seal type that best suits the application, whether it’s an O-ring, gasket, or mechanical seal.
- Size and Tolerance: Ensure the seal is the correct size and has the appropriate tolerance for the application.
- Durability: Select a seal that can withstand the operating conditions without degrading over time.
Innovations in Seal Technology
The seal industry is constantly evolving, with new materials and technologies being developed to meet the demands of modern industrial applications. Innovations in seal technology have led to more durable, efficient, and environmentally friendly sealing solutions.
- Advanced Materials: New materials, such as fluoropolymers and high-performance elastomers, offer enhanced resistance to chemicals, temperature extremes, and wear.
- Smart Seals: The integration of sensors into seals allows for real-time monitoring of seal performance, enabling predictive maintenance and reducing downtime.
- Eco-Friendly Seals: The development of seals made from biodegradable materials helps reduce environmental impact and aligns with sustainable manufacturing practices.
- Customized Sealing Solutions: Advances in manufacturing techniques enable the production of customized seals tailored to specific applications, ensuring optimal performance.
Why Seals Are Vital for Industrial Efficiency
Seals are an integral component of any industrial operation, playing a key role in ensuring the efficiency, safety, and longevity of machinery and systems. By preventing leaks, maintaining pressure, and protecting against contaminants, seals help reduce operational costs, minimize downtime, and extend the life of equipment.
Investing in high-quality seals and regularly inspecting and replacing them as needed is crucial for maintaining the smooth operation of industrial systems. With the continuous advancements in seal technology, industries can benefit from more durable, efficient, and environmentally friendly sealing solutions.
Conclusion: The Future of Seals in Industry
As industries continue to advance, the demand for reliable and efficient sealing solutions will only grow. The future of seals lies in the development of smarter, more durable, and sustainable sealing technologies that can meet the ever-increasing demands of modern industrial applications. By staying informed about the latest innovations in seal technology and choosing the right seals for their applications, businesses can ensure their operations remain efficient, safe, and environmentally responsible.