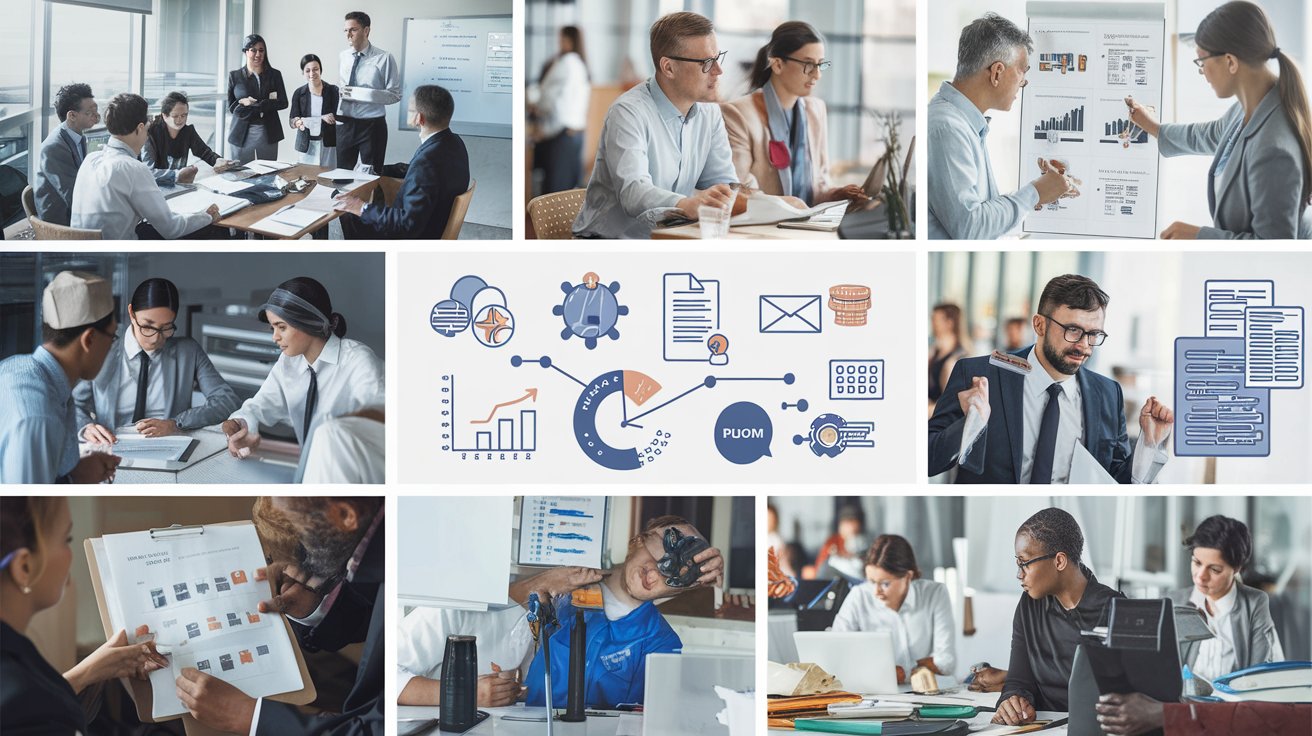
In today’s highly competitive market, the development of a comprehensive quality plan is crucial for organizations aiming to maintain high standards and achieve operational excellence. A quality plan is not merely a set of guidelines but a strategic framework designed to ensure that products and services consistently meet or exceed customer expectations and industry standards. A well-developed quality plan is vital for several reasons. Firstly, it provides a structured approach to managing quality throughout the entire lifecycle of a product or service. This structured approach helps organizations enhance their reliability, reduce defects, and improve customer satisfaction. By systematically addressing various aspects of production and service delivery, a quality plan ensures that every component of the process adheres to established standards and practices. The foundation of any effective quality plan is setting clear objectives and defining the scope. Objectives should be specific, measurable, achievable, relevant, and time-bound (SMART). These objectives guide quality management efforts, ensuring they align with the organization’s overall goals. Defining the scope involves outlining the boundaries and limitations of the quality plan, including the areas of production or service it will cover. This initial step establishes a solid framework for the quality management process. Clearly defined roles and responsibilities are essential for the successful execution of a quality plan. Each team member or department involved in the quality management process must understand their specific duties and how they contribute to the overall quality objectives. This clarity helps in coordinating efforts, avoiding overlaps, and ensuring that all aspects of quality management are addressed effectively. By delineating responsibilities, organizations can foster accountability and streamline quality management efforts. Detailed documentation of processes is vital for maintaining consistency and traceability. The quality plan should include comprehensive descriptions of processes, procedures, and standards that need to be followed. This documentation serves as a reference for employees and aids in training new staff. By documenting processes, organizations ensure that quality practices are applied consistently and that deviations from the standard are easily identifiable and correctable. Robust quality control measures are a critical component of the quality plan. Quality control involves setting up procedures for monitoring and evaluating quality at various stages of production or service delivery. Regular inspections, testing, and audits are integral to identifying potential issues early and taking corrective actions. These measures help maintain high standards and prevent defects or deviations from quality requirements, thereby ensuring that the final output meets the desired standards. A quality plan must be dynamic, incorporating mechanisms for continuous improvement. Continuous improvement involves regularly reviewing performance metrics, analyzing feedback, and making necessary adjustments to enhance quality outcomes. This iterative process ensures that the quality plan remains relevant and effective, adapting to changing conditions and evolving customer expectations. By fostering a culture of continuous improvement, organizations can ensure that their quality management practices evolve in line with industry advancements and customer needs. Integrating customer feedback into the quality plan is crucial for understanding and addressing client needs and expectations. Systematically collecting and analyzing feedback provides valuable insights into areas for improvement. This feedback helps refine processes and products, leading to higher quality outcomes and greater customer satisfaction. By aligning quality management efforts with customer expectations, organizations can enhance their competitive edge and build stronger relationships with their clients. Training and development are integral to maintaining high-quality standards. The quality plan should include provisions for ongoing training, ensuring that employees are well-versed in quality management practices and current industry trends. Regular training opportunities help the workforce stay updated on best practices and emerging technologies, supporting the consistent application of quality standards and fostering a culture of excellence. Effective implementation and monitoring are crucial for the success of a quality plan. Once developed, the plan must be put into action, with all components actively managed and executed. Regular monitoring using key performance indicators (KPIs) and other metrics is necessary to assess the effectiveness of the plan. This monitoring process helps identify areas for further improvement and ensures that the quality plan remains a valuable tool for achieving superior performance and enhancing customer satisfaction. In conclusion, a comprehensive quality plan is an essential asset for any organization committed to excellence. By focusing on clear objectives, defined roles, thorough documentation, robust control measures, continuous improvement, customer feedback integration, and ongoing training, organizations can build a strong foundation for maintaining high standards. Effective implementation and monitoring ensure that the quality plan remains relevant and effective, driving superior performance and enhancing customer satisfaction.
Download the Whitepaper : https://axonator.com/request-for-demo/
About Axonator Inc:
At Axonator, our vision is simple yet powerful: to enable the world on mobile. We envision a future where every aspect of business and society is seamlessly connected through mobile devices. Our mission is to empower businesses worldwide to leverage the full potential of mobile technology, transforming the way they operate, communicate, and collaborate.
Contact:
Axonator Inc. (The World On Mobile)
Austin, TX, USA
USA: +1-512-790-5120
India: +91-7038-600-600
Email: support@axonator.com
Website: https://axonator.com/