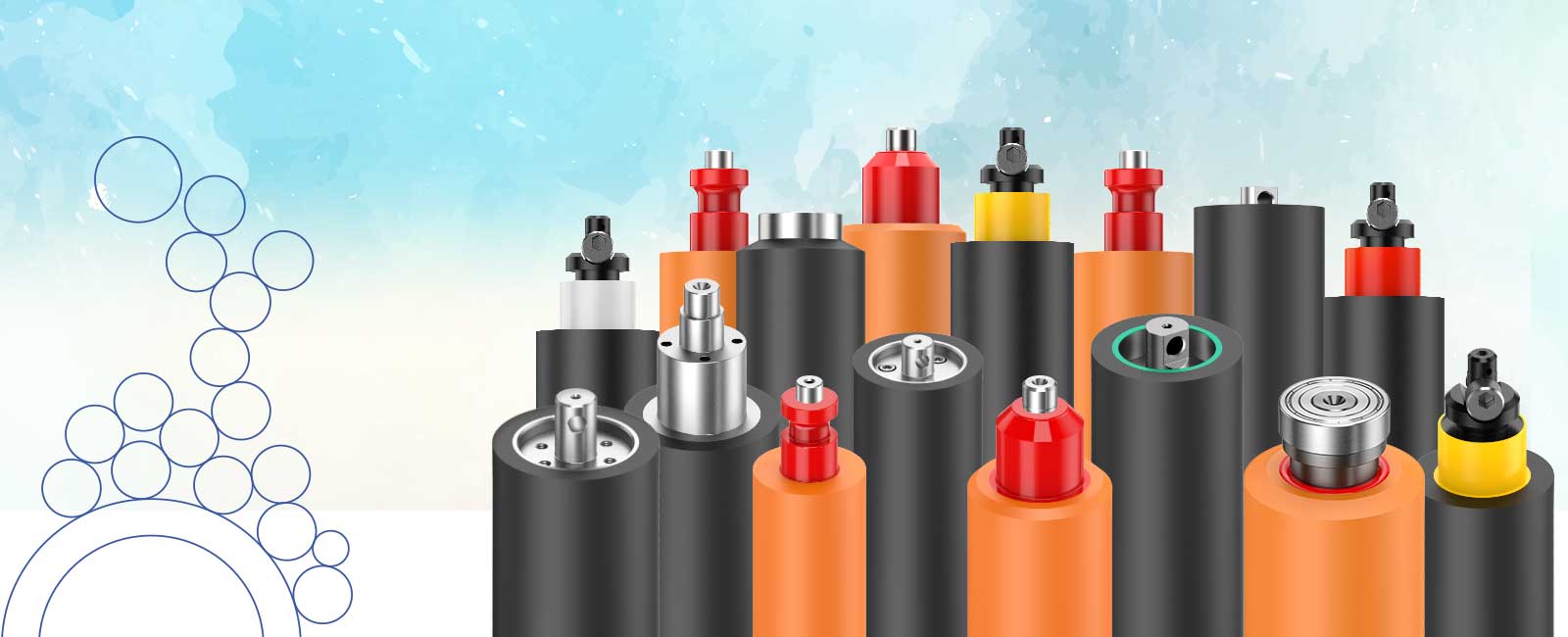
Rubber conveyor rollers are vital components in many industries, from manufacturing to food processing and mining. They help transport materials smoothly and efficiently, allowing operations to run continuously. However, over time, these rollers can wear out due to friction, load-bearing pressure, and exposure to environmental factors. To maximize their lifespan and reduce downtime, implementing a routine maintenance program is essential. Here are some key maintenance tips to help extend the life of rubber conveyor rollers and keep your operations running efficiently.
1. Regular Cleaning and Inspection
Dirt, dust, and debris can accumulate on the rollers over time, affecting their performance and causing premature wear. Regular cleaning is essential to remove any buildup, as debris can lead to friction, slippage, and damage to the rubber surface. Use a soft brush or compressed air to clean the rollers without damaging the rubber. In some cases, mild cleaning agents may be used, but ensure they are compatible with the type of rubber to avoid deterioration. Additionally, inspect the rollers for any signs of wear, cracks, or deformities. Pay special attention to areas that are more prone to damage, such as roller edges. Identifying wear early allows you to address issues before they worsen, saving you from costly repairs or replacements down the line.
2. Lubricate Bearings Regularly
The bearings within the rollers play a crucial role in ensuring smooth rotation. Without adequate lubrication, the bearings can wear out quickly, leading to increased friction and reduced efficiency. Routine lubrication with the appropriate grease or oil is necessary to keep the bearings in good condition. When lubricating, follow the manufacturer’s recommendations regarding the type and amount of lubricant to use. Over-lubrication can be just as harmful as under-lubrication, as excess grease can attract dirt and dust, leading to further issues. A consistent lubrication schedule will help prevent breakdowns, extend the life of the rollers, and ensure optimal performance.
3. Ensure Proper Alignment of Conveyor Rollers
Misalignment of rubber conveyor rollers can cause uneven wear and lead to a host of operational issues. Proper alignment minimizes stress on the rollers and prevents them from being subjected to unnecessary friction and load. Misaligned rollers not only wear out faster but can also cause material spillage and decrease efficiency. Conduct routine alignment checks and make adjustments as necessary. When setting up the conveyor system, ensure that all rollers are level and aligned with the belt path. Using a laser alignment tool can help achieve more precise alignment, reducing the likelihood of human error.
4. Adjust Belt Tension Appropriately
Excessive or insufficient belt tension is one of the main causes of premature roller wear. If the belt is too tight, it can put unnecessary strain on the rollers, leading to faster deterioration. On the other hand, a loose belt may cause slippage, which also contributes to roller wear and tear. Regularly check and adjust the belt tension according to the manufacturer’s specifications. Keep in mind that tension may need to be adjusted over time as belts can stretch with use. A balanced tension ensures that the load is distributed evenly, reducing stress on the rollers and extending their lifespan.
5. Protect Rollers from Environmental Elements
Environmental factors, such as exposure to moisture, extreme temperatures, and chemicals, can have a significant impact on rubber rollers. For instance, constant exposure to high temperatures can cause the rubber to harden or crack, while moisture can lead to rust on the roller’s metal components. Consider using protective covers, especially if your conveyor system is located outdoors or in a harsh environment. UV-resistant materials are essential if the conveyor is exposed to sunlight, while moisture-resistant coatings can help prevent rust. Additionally, ensure that the area around the conveyor is well-ventilated to prevent excessive heat buildup.
6. Rotate or Replace Rollers Regularly
Rotating or switching out rollers periodically can help distribute wear more evenly. This technique is particularly useful in systems where certain rollers bear more weight or endure more friction than others. Rotating the rollers allows you to prevent excessive wear on one part of the conveyor system and extends the overall lifespan of each roller. Keep an inventory of spare rollers and set a schedule for routine replacement, especially for high-wear areas. Although replacing rollers might seem costly upfront, it can be more cost-effective than dealing with unexpected breakdowns that halt production.
7. Monitor Load Capacity and Avoid Overloading
Each conveyor roller is designed to handle a specific load capacity. Exceeding this capacity can lead to excessive wear, deformation, and even breakage. Overloading the conveyor system puts undue stress on the rollers, causing them to wear out more quickly than they would under normal conditions. Be mindful of the load your conveyor system is handling, and avoid exceeding the roller’s weight limits. If your operation has grown or the load has increased, consider upgrading to heavier-duty rollers that are suited to the higher capacity. Monitoring and managing load capacity is one of the simplest yet most effective ways to prolong the life of your rollers.
8. Conduct Routine Preventive Maintenance Checks
Preventive maintenance is essential for ensuring the longevity and optimal performance of rubber covered conveyor rollers. Regularly scheduled maintenance allows you to detect issues before they become critical, reducing the likelihood of unexpected breakdowns. During preventive maintenance checks, ensure that all components are functioning correctly, bolts are tightened, and there are no signs of excessive wear. Consider implementing a preventive maintenance checklist that includes tasks such as cleaning, lubricating, alignment checks, and visual inspections. Keeping detailed records of these checks can also help identify patterns of wear, allowing you to make informed decisions about repairs and replacements.
Conclusion
Proper maintenance is key to maximizing the lifespan and efficiency of rubber conveyor rollers. By incorporating regular cleaning, lubrication, alignment, and load monitoring into your maintenance program, you can ensure that your rollers remain in top condition, minimizing costly downtime and extending their usable life.
Additionally, protecting rollers from environmental elements, rotating them periodically, and adhering to load limits are simple yet effective ways to enhance their durability. Establish a proactive maintenance plan, and you’ll see improvements in both operational efficiency and cost savings, making your conveyor system more reliable and productive over the long term.