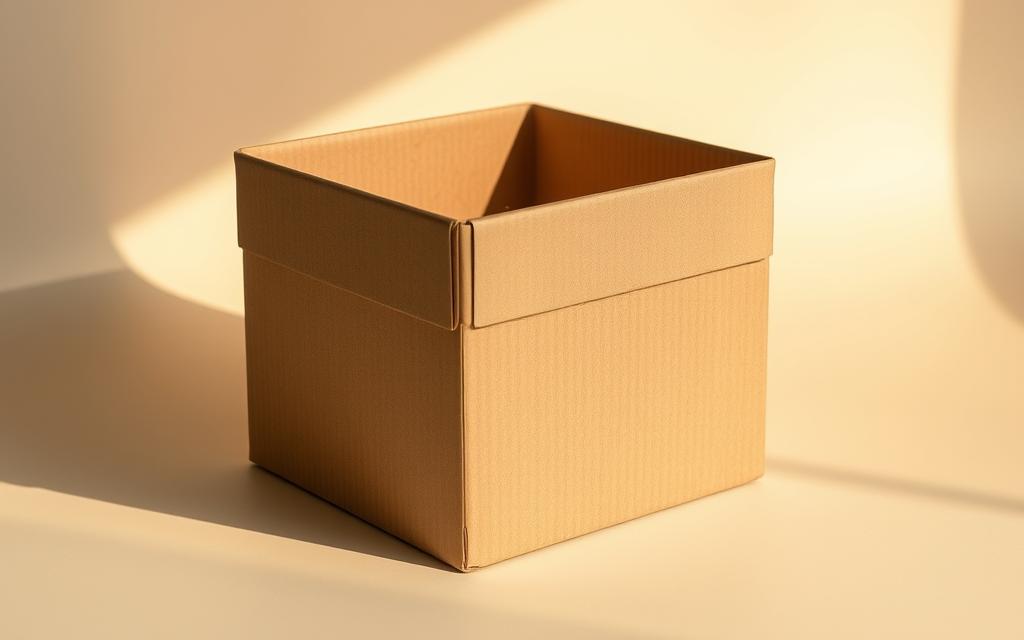
Understanding the Basics of Cardboard Box Manufacturing
Cardboard box manufacturing is a multifaceted process that involves numerous stages, each contributing to the overall strength and durability of the final product. The journey begins with the careful selection of raw materials, primarily wood pulp, which is processed to create paper. This paper is then crafted into the layers of cardboard. The manufacturing process is a marvel of precise engineering, ensuring that the cardboard can withstand a variety of pressures and environmental conditions. Grasping these initial steps is essential for appreciating the complexities involved in producing a reliable packaging solution.
The selection of wood pulp is critical, as it determines the quality and characteristics of the paper produced. Different types of wood pulp can result in varying degrees of strength and flexibility. Once the pulp is selected, it undergoes a series of treatments to remove impurities and enhance its properties. The refined pulp is then transformed into paper through a process of pressing and drying, creating the foundation for the cardboard layers.
As the paper is prepared, it is rolled into large sheets, ready to be cut and shaped into the desired dimensions. The engineering precision in cutting these sheets is paramount, as it affects the uniformity and performance of the final cardboard product. Each sheet is meticulously measured and cut to ensure consistency, allowing for seamless integration into the subsequent stages of manufacturing.
In-Depth Look at Corrugated Box Production
Corrugated box production is an intricate process that transforms raw materials into robust shipping and storage solutions. It involves creating a fluted or corrugated sheet sandwiched between two flat linerboards, a structure that imparts the characteristic strength to corrugated boxes. The production process encompasses several key steps: corrugating the paper, applying adhesive, joining the layers, and cutting the sheets into the desired dimensions. Each step is carefully monitored to maintain quality and consistency, ensuring the boxes can protect their contents during transit.
The corrugating process begins with the formation of the fluted medium. This involves passing the paper through a series of heated rollers that shape it into a wavy pattern. The flutes are the backbone of the corrugated structure, providing cushioning and rigidity. Once the flutes are formed, they are glued between two linerboards using a strong adhesive. This sandwich-like construction is what gives corrugated boxes their extraordinary strength.
After the layers are joined, the corrugated sheets are cut into specific sizes and shapes to form the box blanks. These blanks are then scored and slotted to facilitate easy folding and assembly. The precision in cutting and scoring is crucial, as it ensures that the boxes fit together perfectly and maintain their structural integrity during use.
Exploring the Essentials of Corrugated Boxes Manufacturing
Corrugated boxes manufacturing is a detailed process that demands precision and expertise. The process begins with the creation of the corrugated medium, which involves passing paper through corrugating rolls to form the flutes. These flutes are then glued between two layers of linerboard, creating a single-wall corrugated board. Depending on the application, additional layers may be added to form double or triple-wall boards. The manufacturing process also includes quality checks to ensure the boxes meet industry standards for strength and durability.
The choice of materials plays a significant role in the manufacturing process. Linerboards are typically made from kraft paper, known for its strength and resistance to tearing. The corrugated medium can be crafted from various types of paper, depending on the desired properties of the final product. The combination of these materials is critical in achieving the optimal balance of strength, weight, and cost.
Throughout the manufacturing process, quality control measures are implemented to ensure consistency and reliability. These measures include regular inspections and testing at various stages, from raw material selection to final assembly. By adhering to strict quality standards, manufacturers can produce corrugated boxes that meet the rigorous demands of shipping and storage applications.
Step-by-Step Guide to Corrugated Box Making
Corrugated box making is a step-by-step process that involves several stages, each crucial to the final product's integrity. The process starts with the selection of high-quality paper, which is then corrugated and glued to form the board. The board is cut into blanks, which are then scored and slotted to create the box shape. Finally, the boxes are folded and glued or stitched together, ready for use. Each step in this process is essential for ensuring that the corrugated boxes are capable of withstanding the rigors of shipping and storage.
The initial step of selecting the right paper is vital, as it sets the foundation for the entire manufacturing process. The paper must possess the necessary strength and flexibility to endure the corrugating process and provide adequate protection for the contents of the box. Once the paper is selected, it is fed through a corrugating machine, where it is shaped into flutes and bonded with linerboards to form the corrugated board.
After the corrugated board is formed, it is cut into box blanks. These blanks are then scored and slotted to create the fold lines and slots necessary for assembling the box. The precision in scoring and slotting is crucial, as it determines the ease of assembly and the structural integrity of the final product. The boxes are then folded along the scored lines and glued or stitched together, completing the manufacturing process.
Innovations and Trends in Corrugated Box Manufacturing
The corrugated box industry is continuously evolving, with new technologies and trends shaping the way boxes are manufactured. Innovations such as digital printing and automated production lines have streamlined the manufacturing process, allowing for greater efficiency and customization. Additionally, there is a growing emphasis on sustainability, with manufacturers exploring eco-friendly materials and processes to reduce their environmental impact. These advancements are not only improving the quality and functionality of corrugated boxes but also making the industry more sustainable and adaptable to changing consumer demands.
Digital printing technology has revolutionized the corrugated box industry, enabling manufacturers to produce high-quality, customized designs with ease. This technology allows for greater flexibility in production, as designs can be altered quickly and efficiently without the need for costly printing plates. As a result, manufacturers can offer personalized packaging solutions that cater to the unique needs of their clients.
Automation is another trend that is transforming the corrugated box manufacturing process. Automated production lines can operate at higher speeds and with greater precision than traditional methods, reducing production times and minimizing errors. This increased efficiency allows manufacturers to meet the growing demand for corrugated boxes while maintaining high standards of quality.
Quality Control in Corrugated Box Production
Quality control is a critical aspect of corrugated box production, ensuring that each box meets the required standards for strength and durability. The process involves rigorous testing at various stages of production, from the selection of raw materials to the final assembly of the boxes. Tests may include compression testing, burst strength testing, and edge crush testing, among others. By adhering to strict quality control measures, manufacturers can guarantee that their corrugated boxes are capable of protecting their contents during transportation and storage.
Compression testing is performed to assess the box's ability to withstand stacking during storage and transit. This test measures the force required to crush a box, providing valuable data on its load-bearing capacity. Burst strength testing evaluates the box's resistance to punctures and tears, ensuring that it can protect its contents from external forces.
Edge crush testing is another vital component of quality control, measuring the box's resistance to crushing along its edges. This test is particularly important for boxes that will be stacked during transportation, as it determines their ability to maintain structural integrity under pressure. By conducting these tests, manufacturers can ensure that their corrugated boxes meet the highest standards of performance and reliability.
The Future of Corrugated Box Manufacturing
The future of corrugated box manufacturing looks promising, with advancements in technology and a growing emphasis on sustainability driving the industry forward. As consumer demands continue to evolve, manufacturers are exploring new materials and production methods to enhance the performance and environmental friendliness of their products. The integration of smart technology, such as RFID tags and sensors, is also on the horizon, offering new possibilities for tracking and managing shipments. With these innovations, the corrugated box industry is poised to meet the challenges of the future, providing reliable and sustainable packaging solutions for a wide range of applications.
One of the most exciting developments in the industry is the exploration of biodegradable and recyclable materials. As environmental concerns continue to rise, manufacturers are seeking alternatives to traditional materials that can reduce the environmental impact of corrugated boxes. These efforts are paving the way for a more sustainable future, where packaging solutions are both effective and environmentally responsible.