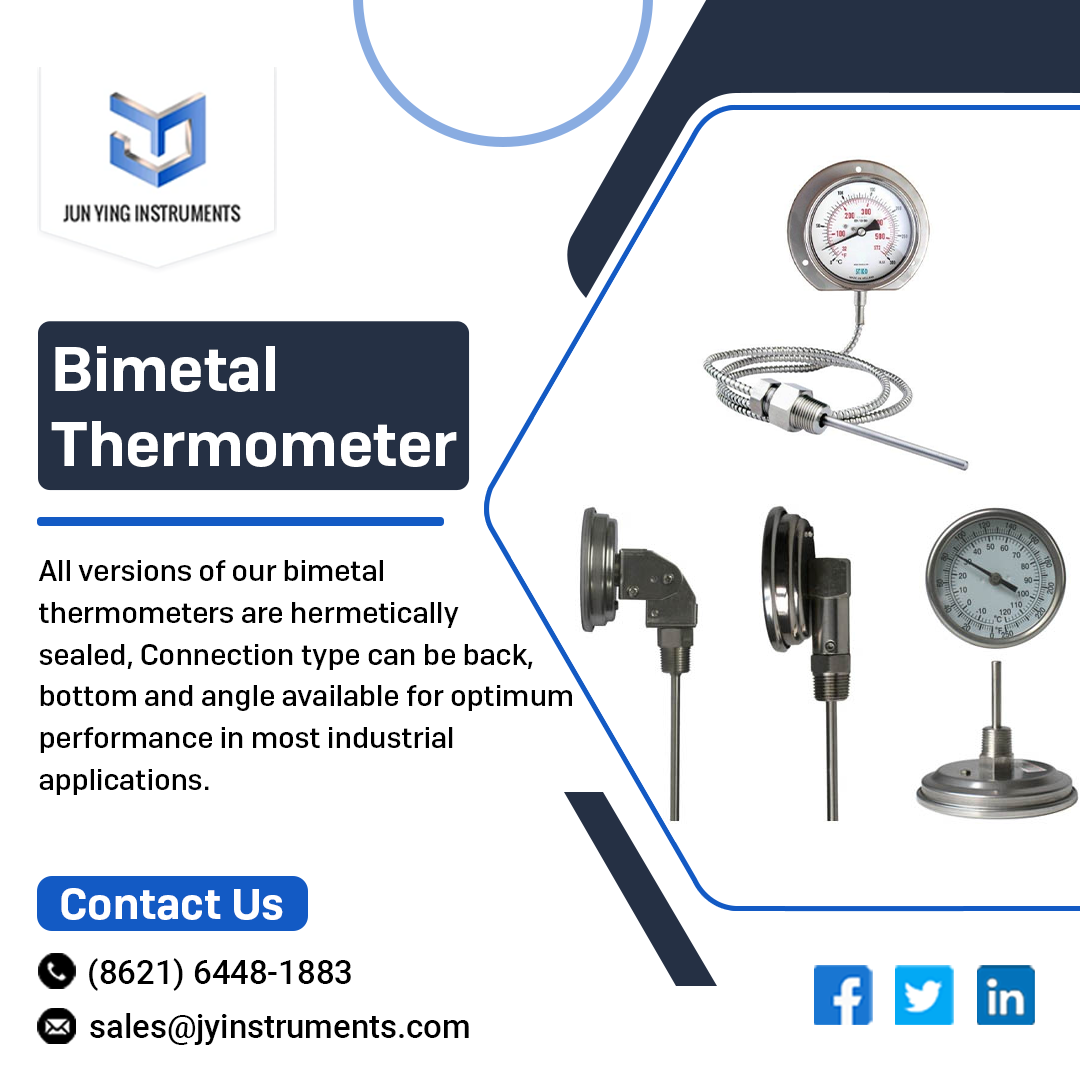
Pressure gauges are crucial tools in many industrial, commercial, and residential systems, especially those involving fluids or gases under pressure. These gauges help monitor system performance, prevent over-pressurization, and ensure safety. However, to maintain their accuracy and function, pressure gauges must be regularly tested and calibrated. This is where test plugs come into play.
A test plug & Sanitary pressure gauge is a small but essential component that allows for quick, safe, and efficient pressure readings or system bleeding without disrupting the process flow. Whether used in HVAC systems, hydraulic equipment, or plumbing applications, understanding how test plugs work and why they matter can make a significant difference in system performance and safety.
What is a Test Plug?
A test plug is a fitting installed into a pressure line or vessel, designed to provide access for pressure readings or testing. It typically consists of a body, a self-sealing valve (often with a rubber or elastomer insert), and a removable cap. Technicians can insert a probe or needle through the self-sealing portion to take a reading without shutting down the system or releasing pressure.
Some test plugs are designed for temporary testing, while others are meant for permanent installation. They come in various sizes and materials to accommodate different pressure ranges and system requirements.
Why Test Plugs are Important
1. Safety
One of the main reasons to use test plugs is to enhance safety. Without a test plug, Bimetal thermowell taking a pressure reading could involve loosening fittings or disrupting pressurized lines—actions that carry the risk of fluid leaks, bursts, or injury. A properly installed test plug minimizes this risk by allowing access to the system in a controlled, contained manner.
2. Efficiency
Test plugs save time during maintenance and troubleshooting. Instead of disassembling parts of the system, technicians can insert a test probe directly into the plug and obtain immediate readings. This significantly reduces downtime and labor costs.
3. Accuracy
Over time, pressure gauges can drift from their calibrated settings due to constant use, environmental conditions, or mechanical wear. Test plugs provide a reliable access point for calibration checks, ensuring that pressure gauges remain accurate and trustworthy.
Common Applications of Test Plugs
Test plugs are used across a range of industries and systems, including:
These plugs can be found in systems dealing with water, air, oil, refrigerant, and various industrial fluids.
Types of Test Plugs
While the general function remains the same, test plugs come in different designs to suit specific needs:
Selecting the right type depends on the application, pressure range, and required frequency of testing.
Installation and Use Tips
Best Practices for Safety
Conclusion
Test plug for pressure gauge may be small components, but their role in pressure gauge safety is vital. They provide a safe, efficient, and reliable means to monitor and maintain pressurized systems. By allowing for quick diagnostics and calibration, they help prevent costly downtime and ensure system safety.
Whether you're a facility manager, technician, or engineer, incorporating test plugs into your regular maintenance routine can go a long way in preserving equipment performance and protecting personnel. Make them a standard part of your safety and efficiency toolkit.