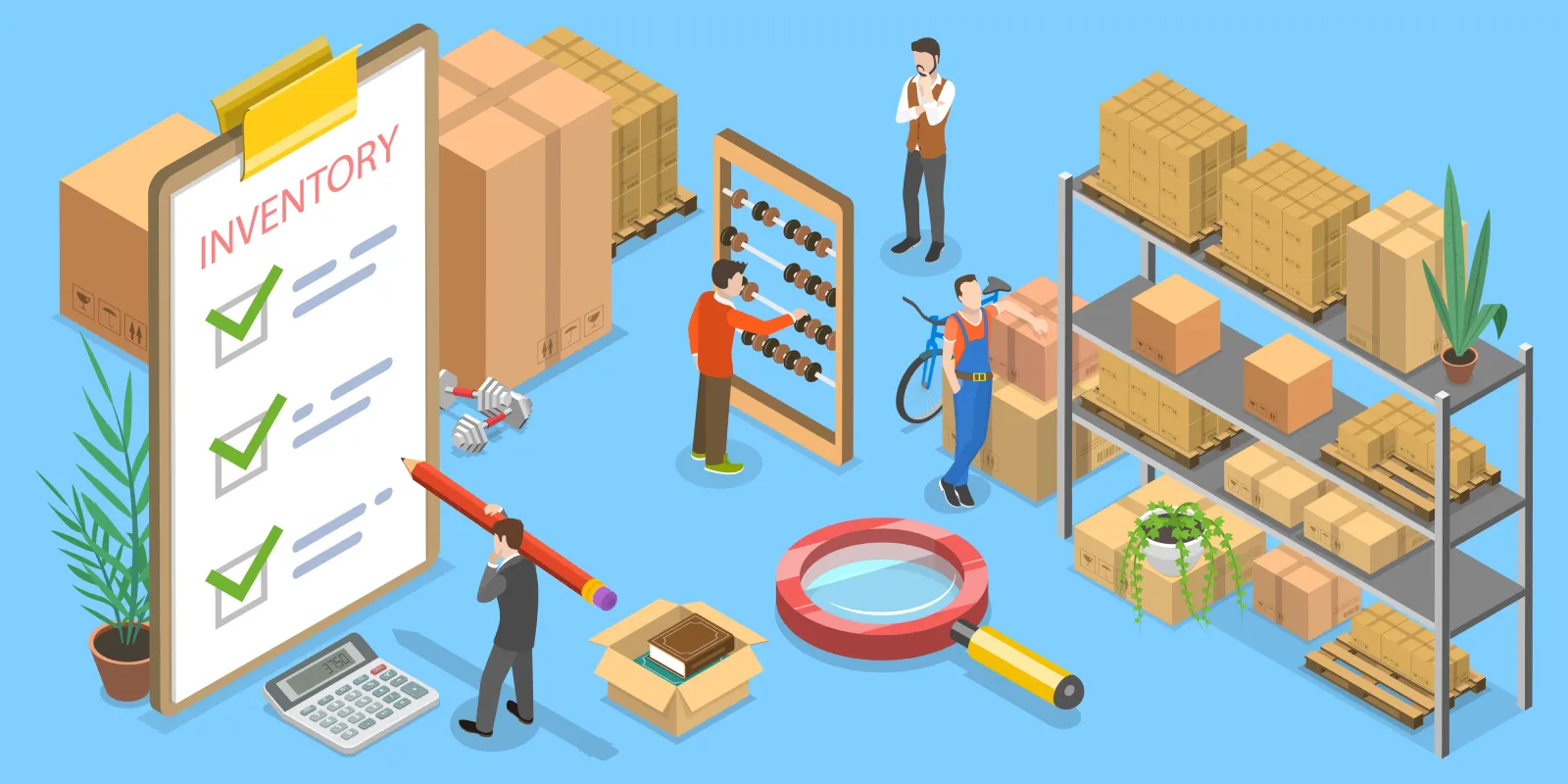
In today’s hyper-competitive market, where consumer expectations are higher than ever, businesses can no longer afford inefficiencies in their supply chain. One of the most critical, yet often overlooked, areas that directly impacts customer satisfaction and delivery speed is Warehouse Management. Whether you're running an e-commerce business, retail chain, or manufacturing unit, how well you manage your warehouse operations can make or break your customer experience.
The Role of Warehouse Management in the Supply Chain
Warehouse Management refers to the processes involved in running a warehouse smoothly, including inventory control, order fulfillment, storage optimization, labor management, and more. A well-managed warehouse ensures that products are stored efficiently, easily located, and shipped out with precision and speed.
It’s not just about storing goods—it's about ensuring the right product gets to the right place, at the right time, in the right condition.
Inventory Accuracy = Customer Trust
Inventory accuracy is one of the foundational pillars of Warehouse Management. If a customer places an order only to later find out that the item is out of stock, it erodes trust and damages your brand reputation. On the other hand, accurate inventory allows you to confidently promise delivery timelines, enhancing customer satisfaction.
Using automated systems like Warehouse Management Systems (WMS) can help reduce human error, provide real-time visibility of stock levels, and enable better decision-making in inventory replenishment and allocation.
Faster Order Fulfillment
Speed is a top priority for modern consumers. According to multiple industry surveys, customers now expect next-day or even same-day delivery. To meet these demands, your warehouse needs to operate like a well-oiled machine.
Efficient Warehouse Management streamlines order picking, packing, and shipping processes. With optimized storage layouts, barcode scanning, and automation, staff can locate and dispatch items faster. Techniques like batch picking, wave picking, and zone picking are strategies used to accelerate order fulfillment while minimizing errors.
The faster the order is fulfilled, the sooner it reaches the customer—resulting in higher satisfaction and repeat purchases.
Reducing Errors = Enhancing Reliability
Mis-picks and shipping the wrong items are costly—not just financially, but also in terms of customer satisfaction. Every returned item not only increases operational costs but also delays the customer’s gratification and damages the brand image.
A strong Warehouse Management strategy reduces such errors through validation checkpoints, barcode verification, and integrated systems that sync with order management and customer relationship platforms. When customers consistently receive the right products on time, their trust in your brand grows.
Real-Time Visibility and Communication
Modern customers appreciate transparency. They want to know when their order has been processed, shipped, and when it will arrive. An advanced Warehouse Management system provides real-time tracking and updates to customers, increasing their confidence in your business.
Moreover, if any issue arises—such as a delay or shortage—real-time visibility allows customer service teams to proactively communicate with the customer, offering alternatives or new timelines. This level of communication can turn a potentially negative experience into a positive one.
Efficient Returns Management
No matter how efficient your operations are, returns are inevitable. What matters is how effectively you manage them. A streamlined reverse logistics process enabled by good Warehouse Management can turn returns into opportunities.
Quickly processing returns, updating inventory in real-time, and refunding or replacing items without hassle ensures a smooth experience for the customer. This builds loyalty and encourages repeat business.
Cost Control That Benefits Customers
Operational inefficiencies in warehouses lead to increased costs due to wasted labor, excess inventory, or poor space utilization. These costs often trickle down to the customer in the form of higher prices or slower service.
Effective Warehouse Management helps optimize labor, space, and inventory, reducing unnecessary overheads. These savings can be reinvested into better delivery services, lower product prices, or customer loyalty programs—benefits that ultimately enhance the overall customer experience.
Scalability for Seasonal Demand
A flexible Warehouse Management strategy allows businesses to scale operations during peak seasons without compromising on speed or accuracy. Whether it’s a holiday surge or promotional campaign, the ability to handle high volumes efficiently is crucial for maintaining customer satisfaction during critical periods.
Advanced forecasting, automation, and resource planning ensure that your warehouse can cope with demand spikes without operational hiccups.
Sustainability and Brand Perception
Today’s customers are also more environmentally conscious. Efficient Warehouse Management can contribute to sustainability by reducing energy consumption, optimizing packaging, and minimizing waste. When your brand is seen as both efficient and eco-friendly, it enhances customer perception and brand loyalty.
Conclusion
In an age where customer expectations are constantly rising, businesses can no longer afford to treat warehouse operations as a backend function. Warehouse Management plays a pivotal role in influencing delivery speed, accuracy, and overall customer satisfaction.
From order accuracy and fast shipping to seamless returns and real-time tracking, every touchpoint in the warehouse process affects the customer experience. Investing in modern warehouse management systems, adopting best practices, and continually optimizing your logistics can give you a competitive edge—and more importantly, happier, loyal customers.
If you're looking to improve customer satisfaction and delivery speed, start by taking a hard look at your warehouse operations. It might just be the game-changer your business needs.