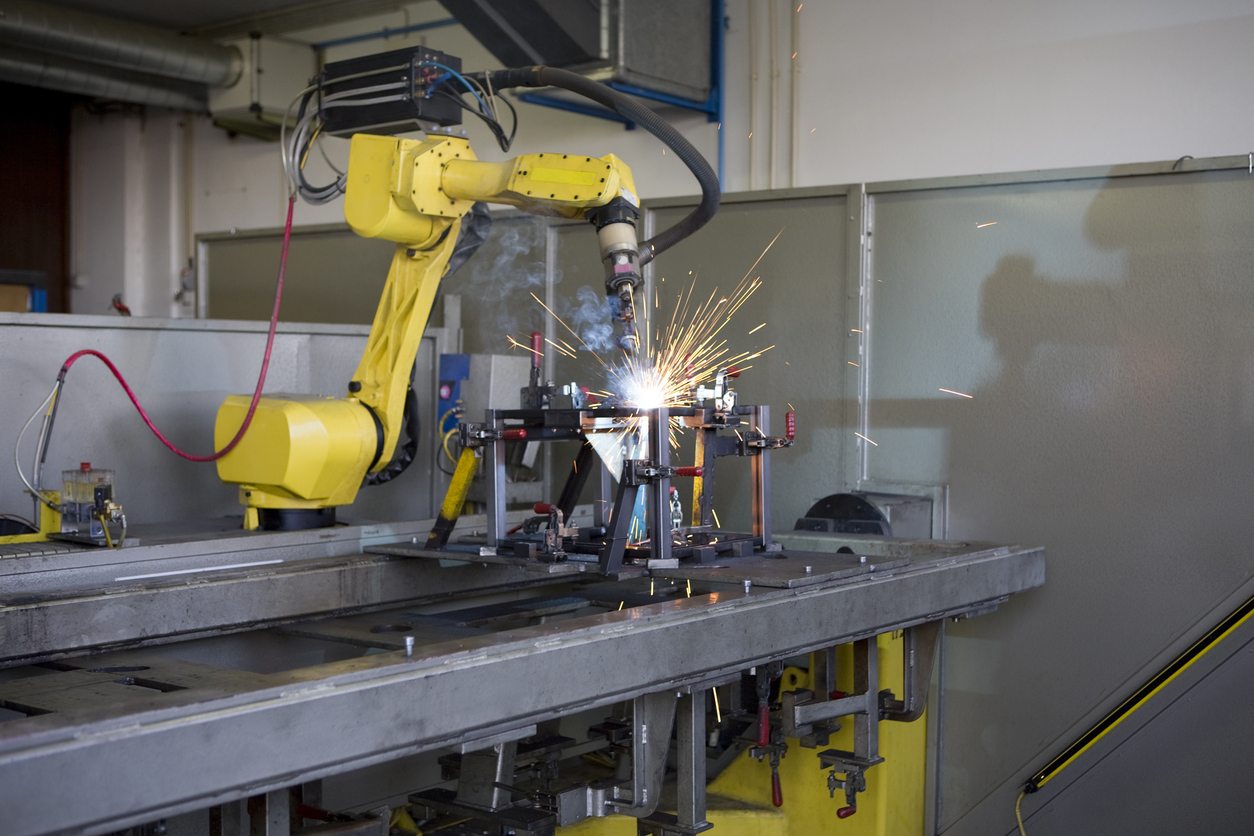
The robotic welding market encompasses a range of automated welding systems designed to perform precise joining operations in industries such as automotive, aerospace, shipbuilding, and heavy equipment manufacturing. These systems integrate programmable robots with advanced welding power sources, vision-guided systems, and sensor feedback loops to deliver consistent weld quality and repeatability. Advantages of Robotic Welding Market solutions include higher throughput, reduced rework rates, improved workplace safety, and lower total cost of ownership over time. As manufacturers face increasing demand for complex assemblies and stringent quality standards, automated welding cells offer the ability to tailor welding parameters in real time, minimizing human error and material waste. Furthermore, collaborative robots (cobots) equipped with force-sensing technologies enable flexible deployment alongside human operators, addressing labor shortages and training constraints. The growing adoption of Industry 4.0 principles—featuring IoT connectivity and data analytics—further enhances predictive maintenance and process optimization. As a result, companies can accelerate product launches, shorten lead times, and maintain compliance with evolving regulatory requirements.
According to CoherentMI, The robotic welding market is estimated to be valued at USD 10.48 Bn in 2025 and is expected to reach USD 20.95 Bn by 2032, growing at a compound annual growth rate (CAGR) of 10.4% from 2025 to 2032.
Key Takeaways
Key players operating in the Robotic Welding Market are
Yaskawa Electric Corporation,
Kuka AG, ABB Ltd.,
Panasonic Corporation,
Fanuc Corporation.
These industry leaders have solidified their positions through strategic partnerships, continuous R&D investments, and regional expansions. Yaskawa Electric Corporation has leveraged its experience in motion control to integrate advanced arc welding modules, while Kuka AG’s collaborative robot offerings target small-to-medium enterprises seeking flexible automation. ABB Ltd. continues to enhance its portfolio with high-deposition welding guns and real-time monitoring software, and Panasonic Corporation emphasizes multimodal welding processes for niche applications. Fanuc Corporation has expanded its global service network, offering turnkey robotic cells from design to commissioning. Collectively, these players drive market innovation, standardize interoperability protocols, and set the benchmark for system reliability and after-sales support.Significant key opportunities in the robotic welding market stem from rising demand in emerging economies and the automotive industry’s shift towards electric vehicles.
The need for precise battery pack welds and lightweight aluminum structures fosters investment in specialized welding heads and adaptive programming. Additionally, the integration of artificial intelligence and machine learning offers growth potential by enabling adaptive weld path planning and predictive defect detection. Companies can capitalize on aftermarket service contracts and retrofit solutions, converting legacy manual welding stations into connected, semi-autonomous cells. Digital twins and cloud-based analytics not only increase process transparency but also open new revenue streams through subscription-based software offerings. Consequently, technology providers and system integrators have the opportunity to diversify their portfolios by offering end-to-end solutions, from initial feasibility studies to remote process monitoring.Global expansion in the robotic welding market is being propelled by increased industrialization across Asia-Pacific, Latin America, and Eastern Europe. In China and India, government incentives for smart factories and “Make in India” initiatives are accelerating adoption, while industrial clusters in Mexico and Brazil benefit from nearshoring trends. European vendors are establishing local assembly plants and R&D centers to comply with regional standards and reduce lead times. North American manufacturers are investing in reshoring efforts, integrating robotic welding lines into automotive, defense, and heavy machinery facilities. Cross-border collaborations between automation specialists and local system integrators are facilitating knowledge transfer and customized solutions, thereby reinforcing global market penetration and long-term customer relationships.
Market drivers and restrain:
Market Drivers
The principal driver fueling the robotic welding market is the demand for higher production efficiency coupled with consistent weld quality. As manufacturers face rising labor costs and skills shortages, automated welding systems offer a reliable solution to maintain 24/7 operations with minimal human intervention. Robotic cells can be programmed for precise control of welding parameters—such as voltage, current, and travel speed—ensuring that each joint meets stringent quality tolerances while reducing spatter and post-weld cleanup. Improved cycle times translate into greater throughput, enabling original equipment manufacturers (OEMs) to meet tight delivery schedules and expand their capacity without proportional increases in labor. Moreover, advancements in sensing and vision technology allow robots to adapt to part variations in real time, reducing scrap rates and material waste. Integration with Industry 4.0 platforms provides data-driven insights for predictive maintenance, helping to prevent unplanned downtime and optimize energy consumption. Collectively, these factors underscore how automation not only boosts productivity but also drives cost savings, competitive advantage, and sustainable manufacturing practices across diverse industrial sectors.
Market Restrain
One of the most significant restraints on the adoption of robotic welding systems is the high initial capital investment and integration complexity. Procuring a fully automated welding cell—including industrial robots, specialized welding power sources, tooling fixtures, and safety enclosures—can represent a substantial outlay for small and medium-sized enterprises (SMEs). Beyond equipment costs, companies must account for engineering services, programming expertise, and employee training to ensure smooth implementation and operation. The integration process often involves customizing the cell layout to existing production lines, calibrating vision systems for part recognition, and establishing robust communication protocols with enterprise resource planning (ERP) systems. Technical challenges such as weld torch alignment, joint fit-up variations, and material reflectivity can complicate commissioning, leading to delays and budget overruns. Additionally, maintenance of robotic cells demands specialized technicians and spare parts, which can further strain operational budgets. These financial and technical barriers may deter potential adopters, slowing market penetration, particularly in cost-sensitive regions and industries with low production volumes.
Segment Analysis
Within the Robotic Welding Market, the “Type” segment stands out as the most critical for analysis, encompassing Arc Welding, Spot Welding, Laser Welding and other subtypes. Among these, Arc Welding commands a dominant share. Its prevalence stems from versatility across metal types, cost-effectiveness and ease of integration into existing production lines. Arc welding robots accommodate a wide range of thicknesses and joint configurations, making them suitable for the automotive, heavy machinery and shipbuilding industries. Manufacturers favor arc welding robots because they deliver consistent bead quality, reduce rework rates and minimize operator safety concerns associated with manual arc welding. In contrast, Spot Welding—while vital in high-volume sheet metal assembly—faces limitations when handling thicker or non-uniform materials, which curtails its application scope. Laser Welding shows promise in specialized sectors such as electronics and medical device manufacturing due to its precision and minimal heat-affected zone, but higher equipment costs and maintenance requirements restrain its adoption in cost-sensitive verticals. As a result, Arc Welding retains its leading position, driven by its lower capital investment per unit of throughput and broad applicability, thereby setting the benchmark for robotic welding installations worldwide.
Global Analysis
Regional dynamics in the Robotic Welding Market reveal Asia Pacific as the dominant region, propelled by robust automotive and electronics manufacturing hubs in China, Japan and South Korea. High production volumes, expanding industrial automation initiatives and government support for Industry 4.0 frameworks have solidified the region’s leadership. In Asia Pacific, localized robotics suppliers and system integrators offer competitive pricing and rapid service, further reinforcing adoption rates among small and medium enterprises. Europe follows closely, with strong demand from automotive OEMs and aerospace fabricators in Germany, France and Italy, where strict quality standards and labor cost pressures accelerate automation investments. North America benefits from advanced aerospace, defense and oil & gas applications, though growth is moderated by established manual welding operations in legacy plants. Looking ahead, the Middle East & Africa region emerges as the fastest-growing market segment. Investments in oil & gas infrastructure, shipbuilding and heavy fabrication projects in countries such as the United Arab Emirates and Saudi Arabia are driving rapid automation adoption. Strategic initiatives to diversify economies away from hydrocarbons are fueling demand for high-speed, high-precision robotic welding solutions, positioning the region for significant expansion over the forecast period.
Get this Report in Japanese Language: ロボット溶接市場
Get this Report in Korean Language: 로봇용접시장
Author Bio:
Money Singh is a seasoned content writer with over four years of experience in the market research sector. Her expertise spans various industries, including food and beverages, biotechnology, chemical and materials, defense and aerospace, consumer goods, etc. (https://www.linkedin.com/in/money-singh-590844163)