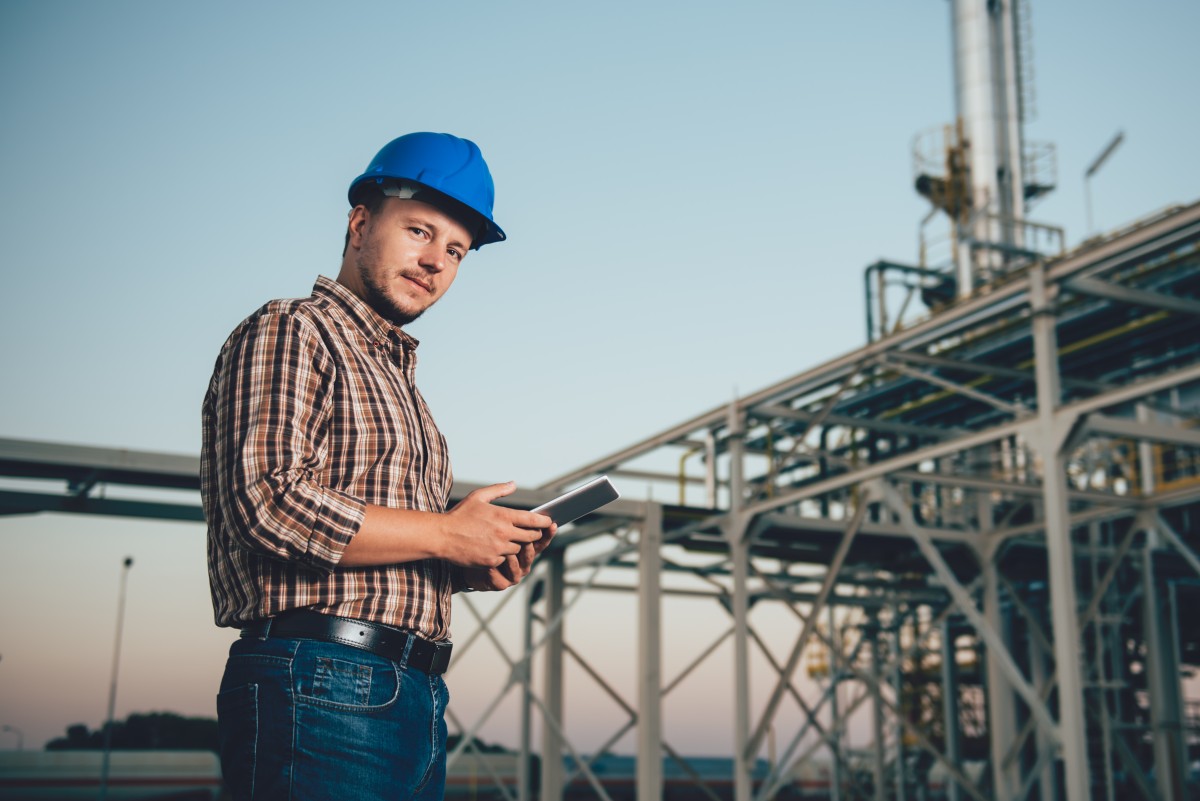
A robust mobile asset management solution helps businesses move from reactive to proactive maintenance, increasing plant uptime, increasing safety, reducing preventable failures, and enhancing technicians' productivity while complying with industry standards & EHS regulations.
Although most businesses have implemented CMMS systems like SAP, IBM Maximo, and Infor EAM, they still use traditional paper-based methods that require technicians to print out Work Orders and collect data on paper. Filled forms reach the office, and the data entry operator manually enters the data into SAP which is time-consuming and prone to errors. Relying on paper-based asset management/field service processes prevents these companies from making informed decisions due to outdated data, leading to asset downtime and safety/compliance risks.
Even when businesses use mobile apps for Work Orders, they still use paper forms for work permits, Job Safety Analysis (JSA), Safety Observations, and Risk assessments.
An effective Mobile EAM solution can integrate mobile apps with digital forms and help businesses maximize asset utilization, increase efficiency, and reduce operational costs.
How does a Mobile EAM Solution add value to your organization?
A Mobile EAM solution empowers your field operators/technicians to perform maintenance activities efficiently on their mobile devices. Reports analyzing this data suggest that companies that have adopted mobile asset management have seen more than a 30% increase in productivity, a 90% reduction in preventable failures, and a 15 to 30% reduction in operational costs. Here are the business benefits realized by Mobile EAM customers according to industry research:
● Increase Productivity with Digital Operations: Certain tasks that don't necessarily need human intervention, such as manual data entry, can be done using mobile forms to increase productivity, data quality, and workforce collaboration. Equipped with mobile apps for EAM, can capture the process & asset data, scan barcodes & RFID tags, capture images, create notifications and comments, execute work orders, and share GPS locations. Shifting your business to digital will optimize field operations and improve worker productivity by more than 30%.
● Move from reactive to predictive maintenance: Using a mobile app while performing tasks will help analyze data in real-time, allowing better decision-making. Advances include capturing measures during the inspection, comparing measurements using repair history, and reporting defects proactively. This precise data helps your business intelligently move from reactive to predictive maintenance and reduces more than 90% of preventable failures.
● Increase Wrench Time: Technicians spend too much time planning work orders, traveling to job locations, searching for spare parts, and coordinating between teams, reducing productivity. Prioritizing crucial tasks is crucial to increasing productivity and wrenching time. Using the Mobile Work Orders App, planning work orders utilizing the map-view, keeping spare parts count using SAP/ERP in real-time, and creating instant purchase requisitions can be quickly done. It increases technicians' wrench time by more than 25 to 30%.
● Increase Safety and Compliance: Information such as P&IDs, SOPs, work instructions, equipment data, links, and videos integrated with the Work Orders app gives more context to field workers performing tasks. They can quickly access this info on their mobile devices, even offline. Filling out mobile forms for risk assessment, job safety analysis (JSA), safety observations, and work permits is easy. Now your business can reduce safety incidents by more than 95% and enhance regulatory compliance & audits.
● First Time Fix: Access to features like video calling and image annotation can provide remote assistance to junior technicians who can effectively understand the specific issue and solve it better. Helping them complete the job on the first visit saves time and costs on repetition. These features address the widening skill gap in industries with a large workforce.
● Location Intelligence: Locational Intelligence has become crucial as it improves field visibility and helps organizations make quicker and more informed decisions. With the mobile EAM app, some advantages are work-orders with a map-view, finding directions, and enhanced audits with auto-capture of time and location.
● Inventory Management: Checking for spare parts using SAP, placing orders for spare parts, and creating purchase requisitions (PR) are all easily done using mobile devices. This mobile app feature can reduce the delay in replacing parts and minimize downtime while automating the workflow for the manager's PR/PO approval with a click away from their mobile devices.
● Reduce Maintenance Cost: With Mobile EAM solutions, there is an improvement in equipment life and reliability, thus reducing the cost of maintenance. An effective mobile EAM solution can reduce maintenance costs by 15 to 20%, per a McKinsey report.
● Sustainability: Eliminating paper-based processes from your business can help improve your organization's responsibility to become cleaner and greener. Its everyone's concern to build a sustainable future.
If you have not yet mobilized asset inspections, work orders, safety checklists, or work permits, you are missing out on significant benefits, including cost savings and productivity. Keep your assets well to remain agile and achieve maximum production to meet demand.