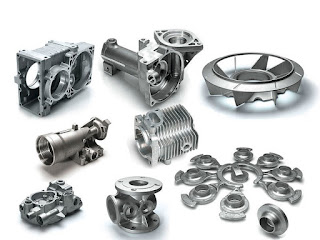
High-Pressure Die Casting (HPDC) is a highly efficient manufacturing method for producing various product shapes. This process forces molten metal into the closed cavity of the steel die at high speed and high pressure. The die has a fixed half and a movable half, both attached to the Die plate of the injection molding machine. Die casting machines have injection tips that use hydraulics and pressurized gases to move a piston forward and inject the molten metal into a sealed steel mold. Injection molding machines also have an attractive loop that uses hydraulics and mechanical switches to absorb injection pressure and keep the mold closed as the part dries. In seconds, this process can turn molten metal into a solid part with an almost clean shape.
The three main metal groups used in this high pressure die casting are aluminum, zinc and magnesium. CWM casts all three metals using a cold and hot chamber high-pressure casting process.
How does the die-casting process work?
In the die-casting process, molten metal or metal alloy is injected into the mold at high speed and pressure. The horizontal die casting machine ensures complete sealing of the mold. They are rated on the clamping force they can apply, and for an Arbomex machine, these can range from 550 to 5700 tons.
Depending on the metal used, the injection unit that fills the mold can be either a hot or cold chamber. In hot chamber injection molding, the metal is held within the machine, then drawn into the chamber and pushed into the mold by the injection plunger. These machine parts are always in contact with molten metal.
In the cold chamber process, the metal is first melted in a separate furnace, transferred to a holding furnace, then poured into a short sleeve and injected into a mold. In the cold chamber process, the metal is first melted in a separate furnace, transferred to a holding furnace, then poured into a short sleeve and injected into a mold. Arbomex offers a wide range of cold chamber injection molding machines.
What is the aluminium die casting process?
High-pressure aluminium die casting is a process that uses a die-casting machine to force molten metal (aluminium) under high pressure into a steel mold or die to form a product. Due to the excellent dimensional accuracy and smooth surface, most die-cast parts require no further processing other than removing edge burrs and any drilling and tapping. In contrast to other casting methods, die casting has the advantage of being fast and inexpensive.
There are several aluminium alloys that the Die Casting Company uses for die-cast parts with different mechanical and chemical properties. Aluminium is used worldwide in 80-90% of high pressure die casting parts alloys. In many cases, die-cast aluminium can replace steel, increasing strength and reducing part weight. We manufacture die castings in small sizes from under an ounce to large sizes of 10 pounds. We can usually manufacture and ship a die casting within two weeks of receiving your order once we have the die in hand and have completed our initial product testing.
Manufacture of high-pressure castings in large quantities
With the right die-casting tools and die-cast part design, thousands of high pressure die-casting parts can be made daily. In some cases, Die Casting produces amounts of 20,000 to 30,000 die-cast parts per week. We can work with your designer or work with them to develop high-volume injection molds.
Production for high-pressure casting in small quantities
We produce die-cast parts for our customers in small quantities, at least 100 die-cast parts. The manufacturing and finishing costs of die-casting parts are higher than larger volumes, so the price of die-casting parts is higher. Some die casters can't handle numbers below a few thousand, so this is an advantage for Die Casting.
High Pressure Die Casting Tooling
Die casting tools are steel hardened to withstand high temperatures and extreme pressures. There are many die-casting tools, from simple and inexpensive inserts to complete die-casting tools designed for only one part. After the die-casting tool is made, the production cost of high pressure die-casting parts is very low. We have an in-house tool maker who can make your mold for die casting or fit your inserts into one of our stands at a very reasonable price.
Advantages of the die casting process
High-pressure die casting technology can produce large parts from light metal alloys in large quantities and at high speeds. This machine has lightweight metal parts with high precision, excellent surface finish, uniformity, and optimal mechanical properties. The high-pressure die casting process can also produce thin-walled components and "co-cast" parts with various inserts such as screws and liners, which then become an integral part of the product.
Conclusion
From product redesign to product reengineering, we are here to help you create a solution that works for you.