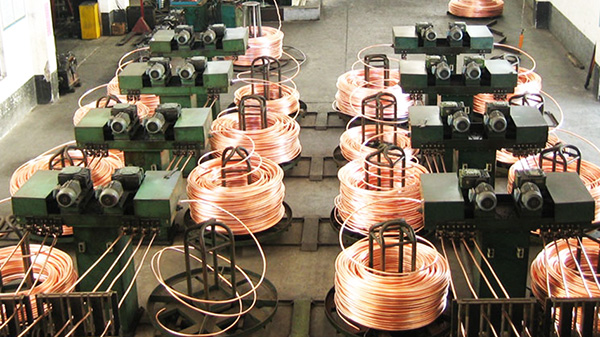
The production of copper wire is a matter of great concern to every cable manufacturer.
Because the copper single wire drawing quality and production efficiency directly affect the subsequent production process, but also the quality of the cable plays a pivotal role, today ZMS cable team takes you to briefly discuss the copper wire drawing machine in cable production often encountered several problems.
The production process, due to the accuracy of the product outside diameter deviation and the uninterrupted production of copper wire drawing equipment, results in the speed of wire drawing will also gradually and annealing not being synchronized.
This causes intermittent irregular changes in wire diameter during drawing due to the fast and slow traction speed.
The Phenomenon Is Caused By The Following Points.
1 Unstable Tension On The Wire Storage Wheel
Production plants in the production process use air pressure in more places, so it will cause unstable air pressure when drawing.
This makes the air pressure in the air pump of the drawing machine high and low, which also leads to the tension of the wire storage can not be kept constant.
However, since the speed of the wire is certain, this makes the pulling force of the wire is not constant, which can cause the deviation of the outer diameter of the single wire can not to be accurately controlled.
2 Copper Wire Chattering On The Annealing Wheel
This causes the copper wire to be annealed in an unstable condition.
The current density flowing during annealing is sometimes large and sometimes small, while the strength of the copper wire at higher speeds is relatively low.
Therefore, it is easy to cause the copper wire on the annealing wheel to fire, so the surface of the copper wire is due to the action of sparks and uneven wire diameter.
3 Wear Of The Main Motor Gearbox
This can make the fixed speed wheel speed of wire drawing and traction speed as well as winding speed not match, thus forming a monofilament pulling thin.
Solution:
Lubricate the wire storage device well to avoid reverse friction on the wire at high speed, thus making the wire-thin.
Adjust the tension of the wire so that the wire is always drawn close to the annealing wheel.
Ensure that the annealing wheel steel ring is in good condition to avoid surface defects in the ring that make the annealing current unstable.
According to the actual situation of the wire drawing machine, re-modeling the wire drawing machine can be based on the following formula.
Annealing wheel speed / fixed speed wheel speed = front slip coefficient × fixed speed wheel diameter/annealing wheel diameter.
Where the diameters of the constant speed wheel and annealing wheel are known, the rotational speed of the constant speed wheel and annealing wheel can also be measured.
From this, the front slip coefficient can be obtained, and the slip coefficient can be used to re-mold this drawing machine so that the molds can be matched to meet the requirements.
Wire Drawing Machine To Pull Out The Monofilament Surface Oxidation Causes.
1 Cooling Water Temperature Is Too High
The temperature of the cooling water in the sealing chamber is too high, exceeding 40℃.
This sealing chamber on the monofilament will not play the required cooling effect, resulting in the monofilament in the annealing temperature is still very high, high temperature encounters oxygen in the air and oxidation.
2 Saponification Fluid Content Is Not Enough
The saponification liquid content of the coolant in the sealed chamber is not enough.
This will increase the friction between the monofilament and each guide wheel, which in turn will make the temperature of the monofilament rise again, causing the oxidation of the monofilament surface.
3 Water Pressure And Water Are Not Enough
The water pressure and water volume of the cooling water in the sealing chamber are not enough, so the monofilament can not achieve a satisfactory cooling effect.
Solution:
1 Frequently check whether the equipment for cooling circulating water is operating normally and whether the cooling effect is normal.
2 in the sealed chamber at certain intervals to add substances that can increase the concentration of saponification fluid, which can change the content of the saponification fluid in the cooling water to ensure that the monofilament can operate normally on the guide wheel.
3 regularly check whether the water pressure of the circulating water is normal, and constantly change the pressure and volume of cooling water entering the sealing chamber according to the change in water pressure during production.
Causes Of Frequent Wire Breakage During Operation.
1 Wire drawing dies in uninterrupted production will be due to normal wear and tear of the wire drawing die sizing area becoming larger.
2 The quality of various rod materials.
In start-up production, the production material from time to time has some quality defects problems, which will cause the monofilament in the process of wire drawing deformation can not be predicted to judge the tension of the broken.
This rarely happens when the quality of the production material is relatively good.
3 The annealing current in production is not constant, the current is suddenly high, and the monofilament is pulled off during the annealing process or fused by the sudden change of strong current.
Solution:
1 Before production, do a full self-inspection of the copper rod to be produced and find out the quality defects of the rod in time.
2 Depending on the situation, find the appropriate countermeasures in time, reduce the drawing speed, or remove the section with defects.
3 Constantly observe whether the annealing current of the drawing is normal during production, especially when it is just starting up, and pay special attention to the change of the annealing current.
4 Adjust the size of the annealing current according to the change in wire speed, and then make the annealing current slowly with the increase in wire speed and become larger to ensure the normal operation of the equipment.
5 I believe that as long as the actual production focus on the above points of control, the quality of copper wire drawing products and production efficiency will have different degrees of improvement, to better and faster for the next process production to provide a strong production guarantee.
The above is a summary of the problems encountered in the process of drawing copper wire, as well as proposed to encounter problems how to solve. So in the cable production process, be sure to pay attention to safety and various risk factors to avoid unnecessary trouble.