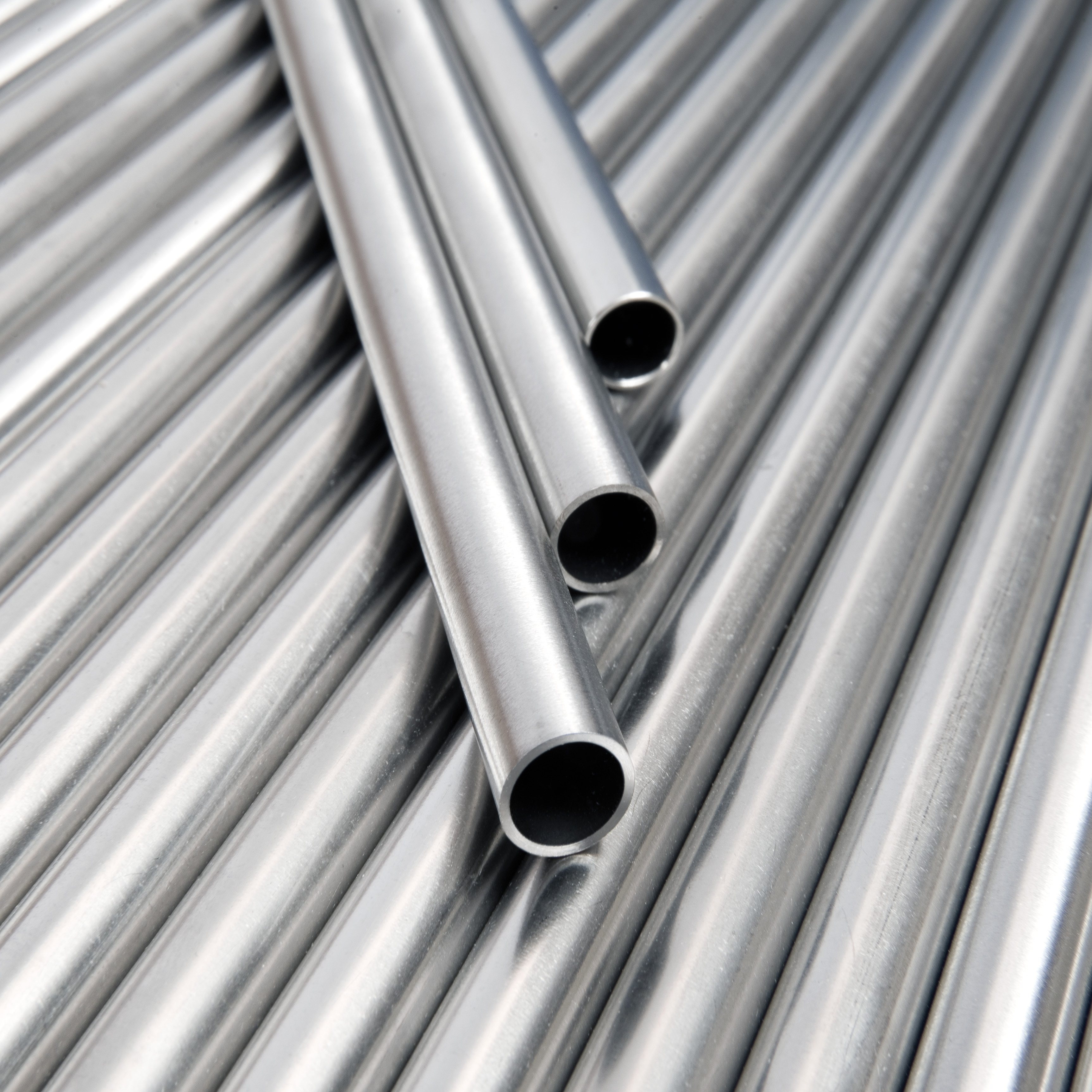
In today's rapidly advancing industrial world, the need for materials that can withstand extreme conditions while delivering peak performance is paramount. Among these standout materials, Inconel tubes emerge as a leading choice for numerous high-stress applications. These tubes, famed for their incredible resistance to extreme temperatures and corrosive environments, have carved a significant niche in various sectors.The Inconel tubes sizes can be customized to meet the needs of a particular industry and range from thin-walled precision tubes to pipes with a larger diameter.
The Inception and Composition of Inconel Tubes
Inconel, a superalloy primarily consisting of nickel, also incorporates chromium and, in some variants, molybdenum and other elements. The combination of these materials provides the alloy with its iconic heat and corrosion resistance, making it a favorite for industries that operate under severe conditions. What's particularly fascinating about Inconel is its ability to retain its strength in extreme temperatures, an attribute few metals possess.
Distinguishing Properties of Inconel Tubes
Several inherent properties position Inconel tubes at the forefront of industrial applications:
- Heat Resistance: Inconel tubes thrive in high-temperature environments. Their ability to retain their mechanical properties, even when exposed to temperatures reaching 1000°C, makes them invaluable in sectors like aerospace.
- Corrosion Resistance: Thanks to the high nickel content, Inconel tubes resist corrosion even in acidic or alkaline settings. This property makes them a go-to option in the chemical processing industry.
- Durability: These tubes are not only resistant to wear but also demonstrate a high fatigue strength, ensuring longevity in cyclic operations.
Key Applications Across Industries
Given their robust nature, Inconel tubes find their use in a variety of critical applications:
- Aerospace: Given the extreme temperatures and pressures aircraft components are exposed to, Inconel tubes are often the material of choice for jet engines and exhaust systems.
- Energy Sector: From nuclear reactors to gas turbine blades, the tubes' ability to resist high-temperature oxidation is a boon.
- Chemical Processing: Handling aggressive chemicals demands materials that won't corrode or degrade. Inconel tubes rise to this challenge effortlessly.
Working with Inconel Tubes
Despite their resilience, working with Inconel requires specialized knowledge and techniques. Welding, for instance, demands specific procedures to ensure the integrity of the alloy isn't compromised. Moreover, understanding the alloy's properties can help industries harness its potential fully.
Looking Ahead: The Future of Inconel Tubes
As industries push the boundaries of innovation, the demand for materials that can stand the test of extreme conditions continues to rise. Inconel tubes, with their blend of durability and resistance, are poised to remain integral to these advancements. As research delves into refining and enhancing the properties of this superalloy, the horizon looks promising for even broader applications.
Conclusion
In a landscape dominated by the quest for materials that marry strength with resistance, Inconel tubes have etched an indelible mark. As industries continue to evolve and confront new challenges, the reliance on these tubes is only set to grow, underscoring their significance in modern engineering and manufacturing paradigms.