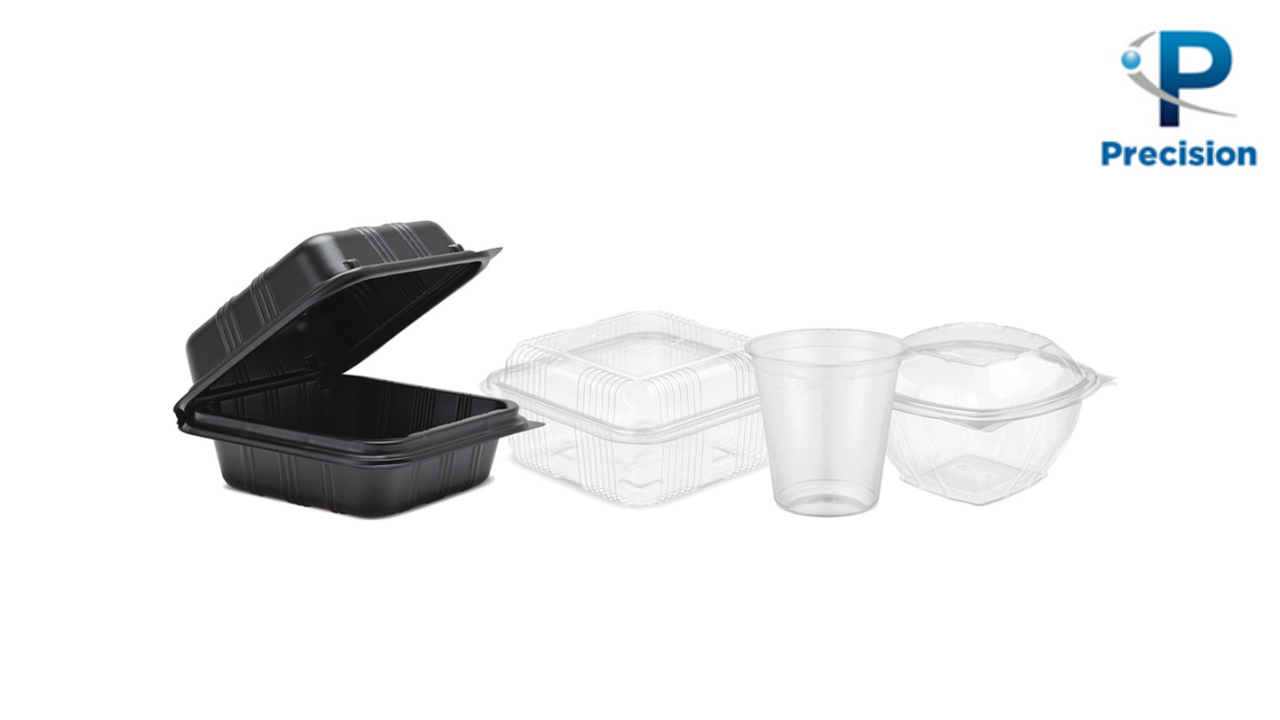
Key Features of Thermoforming
Thermoforming is a widely used technique in the plastic manufacturing industry. It offers numerous advantages, making it a preferred choice for many applications. In this comprehensive guide, we will explore the key features of Thermoforming Plastic Manufacturer in UAE, including the various forming techniques and their benefits. Whether you are a professional in the industry or simply curious about the process, this guide will provide you with a deeper understanding of thermoforming and its importance in plastic manufacturing.
Exploring Plastic Forming Techniques
Thermoforming is a versatile process that allows manufacturers to shape plastic sheets into various forms. There are three main types of thermoforming techniques commonly used: vacuum forming, pressure forming, and twin-sheet forming.
Vacuum Forming
Vacuum forming is one of the most widely used thermoforming techniques. It involves heating a plastic sheet until it becomes pliable and then using a vacuum to draw the heated sheet onto a mold. The vacuum ensures that the plastic conforms to the mold's shape, resulting in a precise and consistent form.
One of the key advantages of vacuum forming is its ability to create complex shapes with ease. It is a cost-effective solution for producing large, lightweight, and low-volume parts. The process offers excellent design flexibility, allowing manufacturers to create custom shapes and sizes for various applications.
Vacuum forming is commonly used in industries such as automotive, packaging, and aerospace. It is particularly suitable for applications that require high-quality surface finishes and intricate details.
Pressure Forming
Pressure forming, also known as vacuum pressure forming, is similar to vacuum forming but involves the use of additional pressure in the forming process. The plastic sheet is heated and pressed against the mold with the help of both vacuum and air pressure. This technique allows for even greater detail and precision, making it suitable for complex and highly detailed parts.
The added pressure in pressure forming results in improved definition of features, sharp angles, and tighter tolerances. It enhances the overall surface finish, making it ideal for applications that require high-quality aesthetics. Pressure forming is commonly used in industries such as electronics, medical, and consumer goods.
Twin-Sheet Forming
Twin-sheet forming is a thermoforming technique that involves joining two plastic sheets together to form a hollow part. The process typically involves heating two plastic sheets simultaneously and then pressing them together to create a sealed, double-walled structure.
This technique is commonly used for applications that require extra strength, insulation, or the ability to hold fluids. It is commonly used in industries such as automotive, transportation, and industrial equipment manufacturing. Twin-sheet forming offers excellent structural integrity and is often used for producing components such as fuel tanks, containers, and enclosures.
Benefits of Thermoforming Plastic
Thermoforming plastic offers several key benefits that make it a popular choice in the manufacturing industry. These benefits include:
Cost-effectiveness: Thermoforming is a cost-effective manufacturing process, especially for low-volume production. The initial tooling costs are lower compared to other plastic forming techniques, making it an attractive option for small to medium-scale production.
Design flexibility: Thermoforming allows for a high degree of design flexibility. Manufacturers can easily create custom shapes, sizes, and textures to meet specific requirements. The process is highly adaptable and can accommodate changes in design quickly and efficiently.
Fast production times: Thermoforming offers faster production times compared to other plastic forming processes. The simplicity of the technique and the ability to produce large parts in a single cycle contribute to its efficiency and speed. This is particularly advantageous for projects with tight deadlines.
Wide material selection: Thermoforming is compatible with a wide range of thermoplastic materials, including ABS, PVC, PETG, polystyrene, and polypropylene. This versatility allows manufacturers to select the most suitable material for their specific application, considering factors such as strength, transparency, chemical resistance, and color.
Sustainability: Thermoforming is a sustainable manufacturing process when compared to other traditional forming techniques. It generates minimal waste, and the scrap material can be recycled and reused. Thermoformed plastic products can also be recycled at the end of their useful life, reducing environmental impact.
Conclusion
Thermoforming Plastic Manufacturer in UAE is a highly versatile and cost-effective manufacturing process. Whether you are looking to produce intricate parts, custom shapes, or large volumes of plastic components, thermoforming offers numerous advantages. With the ability to create complex shapes, fast production times, and a wide material selection, thermoforming is a popular choice across various industries. By understanding the key features of thermoforming and its benefits, manufacturers can make informed decisions when selecting the most suitable plastic forming technique for their specific application.