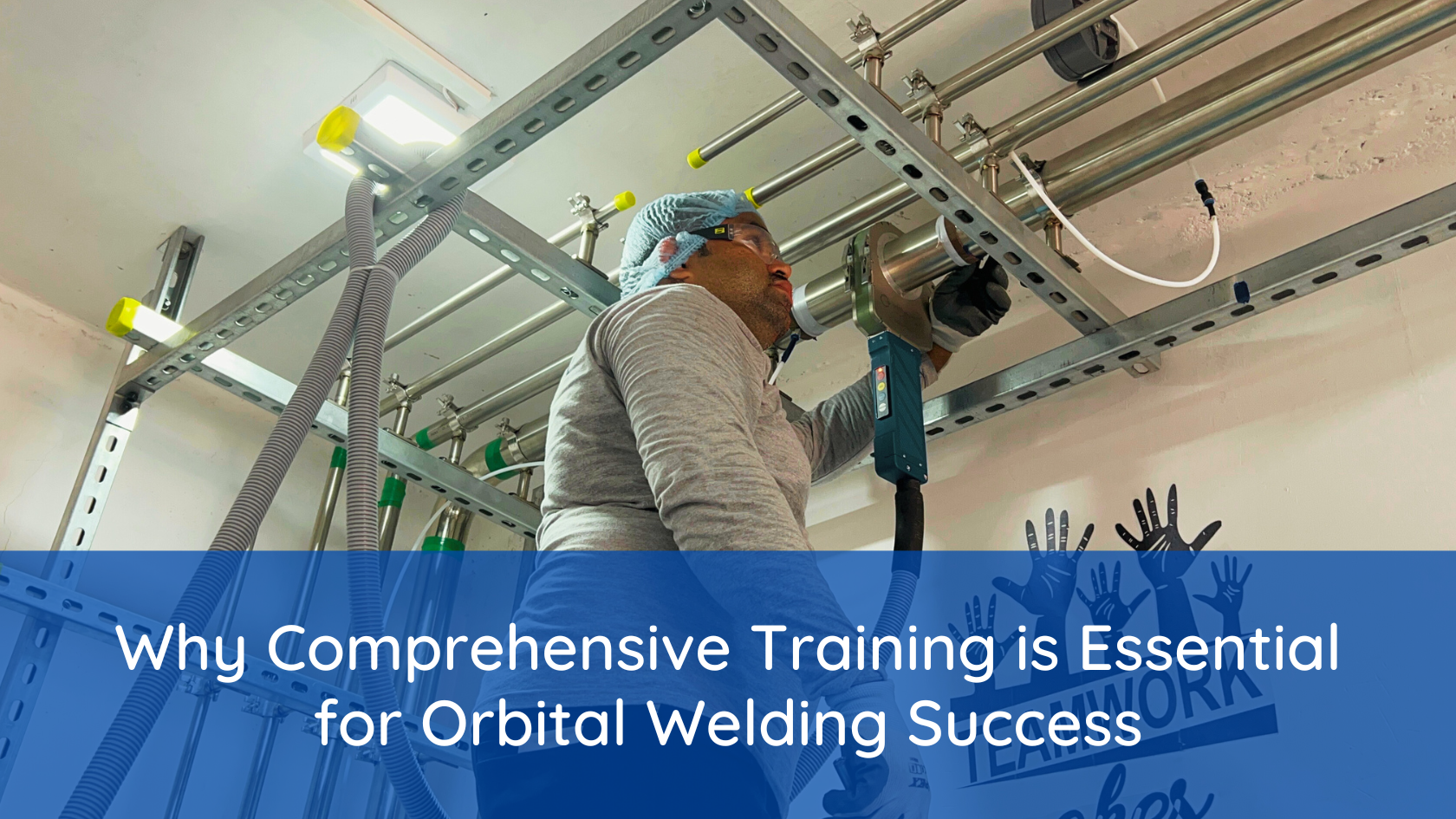
Orbital welding, a specialized form of welding, is essential in industries requiring precision, consistency, and reliability. From aerospace to pharmaceuticals, this welding technique ensures the highest standards in critical applications. However, the complexity of orbital welding necessitates proper training. Without it, operators may face safety risks, subpar weld quality, and inefficiencies. Here’s why comprehensive training is indispensable for those working in this specialized field.
What is Orbital Welding?
Orbital welding is an automated welding process where a welding arc rotates 360 degrees around a static workpiece, such as a pipe or tube. This technique is renowned for producing uniform and high-quality welds, especially in applications where manual welding would be impractical or prone to errors.
The process relies on precision equipment, including orbital welding heads, power sources, and controllers. It is used in industries with stringent requirements, such as nuclear power plants, semiconductor manufacturing, food processing, and more. To achieve these high standards, operators must not only understand the equipment but also master the intricacies of the process.
Key Reasons for Proper Training in Orbital Welding
1. Complexity of Equipment: Orbital welding systems are highly sophisticated. Operators need to understand how to configure, calibrate, and maintain the equipment to achieve consistent results. Training provides hands-on experience with different welding heads, power sources, and control systems, ensuring the operator can confidently handle the tools and troubleshoot issues as they arise.
2. High Standards for Weld Quality: Industries employing orbital welding demand welds that meet strict quality standards. For example, in pharmaceutical and food processing industries, welds must be smooth and free from contaminants to prevent bacterial growth. Similarly, aerospace and nuclear sectors require welds that can withstand extreme conditions without failure.
3. Safety Concerns: Orbital welding involves significant safety risks, including exposure to high temperatures, intense light, and hazardous fumes. Without adequate training, operators may neglect proper safety protocols, increasing the risk of injuries or equipment damage.
4. Efficiency and Cost-Effectiveness: Skilled operators can significantly reduce production time and material wastage. Proper training teaches operators how to optimize welding parameters such as voltage, current, and travel speed. This ensures that welds are completed efficiently without sacrificing quality.
5. Adaptability to Different Applications: Orbital welding is used across various industries, each with unique challenges. For instance, welding in a cleanroom environment for semiconductor manufacturing requires a different approach than welding high-pressure pipes in oil and gas applications.
6. Regulatory Compliance: Many industries using orbital welding must comply with stringent regulations. For instance, the American Society of Mechanical Engineers (ASME) and the Food and Drug Administration (FDA) have specific requirements for weld quality in certain applications. Training ensures operators understand these standards and can meet them consistently.
The Benefits of Proper Training
Proper training in orbital welding offers numerous benefits for both operators and their employers. For operators, it enhances their skills, boosts employability, and ensures safety. For employers, trained operators improve efficiency, reduce risks, and uphold quality standards.
By investing in proper training, companies can also stay competitive in industries where precision and reliability are paramount. It enables them to meet client expectations, avoid costly errors, and maintain compliance with evolving regulations.
Conclusion
Orbital welding is a critical process in industries requiring unmatched precision and consistency. However, its complexity demands proper training to ensure safety, quality, and efficiency. Without trained operators, the risks of poor weld quality, safety incidents, and operational inefficiencies increase dramatically.
Investing in orbital welding training is not just a necessity — it’s a strategic advantage. It empowers operators with the skills and confidence to excel in their roles, contributing to the success of their organizations and the industries they serve.