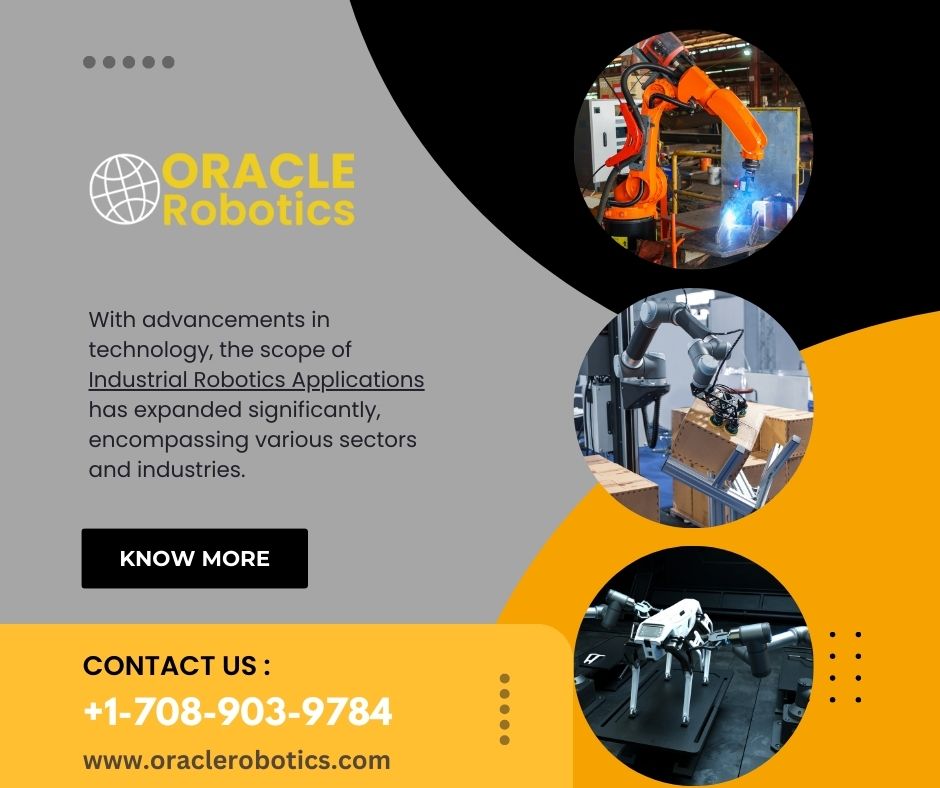
Industrial robots have become an integral part of modern manufacturing and production processes, transforming industries with their precision, efficiency, and adaptability. These advanced machines are designed to perform repetitive tasks, handle heavy loads, and operate in hazardous environments, ensuring consistent quality and enhanced productivity. With advancements in technology, the scope of Industrial Robotics Applications has expanded significantly, encompassing various sectors and industries. Let’s delve into some of the most prominent applications of industrial robots and how they are reshaping the industrial landscape.
1. Material Handling
One of the most common applications of industrial robots is material handling. Robots are used for tasks such as loading and unloading materials, sorting products, and transporting goods within a facility. Their ability to handle heavy loads with precision reduces the risk of damage to materials and ensures faster operations. In warehouses and manufacturing plants, material handling robots contribute to increased efficiency and streamlined workflows.
2. Assembly
Industrial robots play a vital role in assembly lines, particularly in industries like automotive and electronics. Robots can perform tasks such as screwing, welding, and component placement with exceptional accuracy. Their ability to work tirelessly ensures consistent product quality and faster production rates. Moreover, robots can adapt to varying assembly requirements, making them ideal for industries with diverse product ranges.
3. Welding
Welding is a critical application in sectors such as automotive, aerospace, and construction. Robotic welding systems offer precise and consistent welds, reducing the risk of errors and enhancing product durability. They can perform various types of welding, including spot welding and arc welding, in challenging environments where human workers may face safety risks. This capability makes robotic welding a cornerstone of modern manufacturing.
4. Painting and Coating
Industrial robots are extensively used for painting and coating applications. Their ability to apply uniform layers of paint or coating ensures a high-quality finish while minimizing material waste. Robotic painting systems can operate in hazardous environments, protecting workers from exposure to harmful fumes and chemicals. These systems are particularly popular in the automotive industry, where precision and efficiency are paramount.
5. Machine Tending
Machine tending involves loading raw materials into machines, monitoring the process, and removing finished parts. Robots are ideal for this application as they can work continuously without fatigue. In industries such as metalworking and plastics, robotic machine tending ensures consistent production and reduces downtime. Additionally, robots can be programmed to handle multiple machines, maximizing operational efficiency.
6. Quality Inspection
Robotic systems equipped with advanced sensors and vision technology are revolutionizing quality inspection processes. These robots can identify defects, measure dimensions, and verify product quality with unparalleled accuracy. By automating inspection tasks, manufacturers can ensure consistent quality standards while reducing the time and labor required for manual inspections.
7. Packaging and Palletizing
Industrial robots are widely used for packaging and palletizing tasks in industries such as food and beverage, pharmaceuticals, and consumer goods. Robots can quickly and accurately pack products into boxes, arrange them on pallets, and prepare them for shipping. This automation not only accelerates production but also reduces the risk of errors and injuries associated with manual handling.
8. Cutting, Grinding, and Polishing
Robotic systems are increasingly used for cutting, grinding, and polishing applications. These tasks require high precision and can be hazardous for human workers. Robots equipped with advanced tools can perform these operations with consistent accuracy, ensuring high-quality finishes in industries such as metal fabrication and furniture manufacturing.
9. Hazardous Environment Operations
In industries such as chemical processing, mining, and nuclear power, robots are employed to perform tasks in hazardous environments where human safety is a concern. These robots can handle toxic materials, operate in extreme temperatures, and navigate dangerous terrains, ensuring operational continuity while protecting workers.
10. Research and Development
Industrial robots are also used in research and development (R&D) settings to test and prototype new products. Their precision and programmability make them ideal for conducting experiments and simulating production processes. In fields like pharmaceuticals and electronics, robots play a crucial role in accelerating innovation and reducing time-to-market.
The Role of Oracle Robotics in Industrial Robotics Applications
At Oracle Robotics, we specialize in providing advanced solutions for diverse Industrial Robotics Applications. Our cutting-edge robotic systems are designed to meet the unique needs of various industries, delivering unparalleled performance, reliability, and efficiency. Whether it’s automating assembly lines, enhancing quality inspection, or optimizing material handling, Oracle Robotics empowers businesses to achieve their goals with innovative automation technologies.
Benefits of Industrial Robots
The adoption of industrial robots offers numerous benefits that contribute to operational excellence:
- Increased Productivity: Robots can work around the clock without fatigue, significantly boosting production rates.
- Enhanced Precision: Robots perform tasks with a high degree of accuracy, reducing errors and ensuring consistent quality.
- Cost Savings: Automation reduces labor costs, minimizes waste, and optimizes resource utilization.
- Improved Safety: Robots handle hazardous tasks, protecting workers from potential injuries and health risks.
- Flexibility: Modern robots can be reprogrammed for different tasks, making them adaptable to changing production needs.
Future Trends in Industrial Robotics
The field of industrial robotics is evolving rapidly, driven by advancements in technology. Key trends include:
- Collaborative Robots (Cobots): Cobots are designed to work alongside humans, enhancing productivity while maintaining safety.
- AI and Machine Learning Integration: Robots equipped with AI capabilities can learn from data, adapt to new tasks, and improve performance over time.
- IoT Connectivity: IoT-enabled robots can communicate with other machines and systems, enabling seamless integration and real-time monitoring.
- Energy Efficiency: New robotic systems are designed to consume less energy, supporting sustainable manufacturing practices.
- Miniaturization: Compact and lightweight robots are expanding the scope of industrial applications, particularly in small-scale production environments.
Conclusion
Industrial robots are transforming the way industries operate, offering unmatched efficiency, precision, and versatility. From material handling to quality inspection, these machines are indispensable in modern manufacturing and beyond. As technology continues to advance, the potential for Industrial Robotics Applications will only grow, driving innovation and competitiveness across sectors. With solutions from Oracle Robotics, businesses can harness the power of industrial robots to stay ahead in an ever-evolving market.