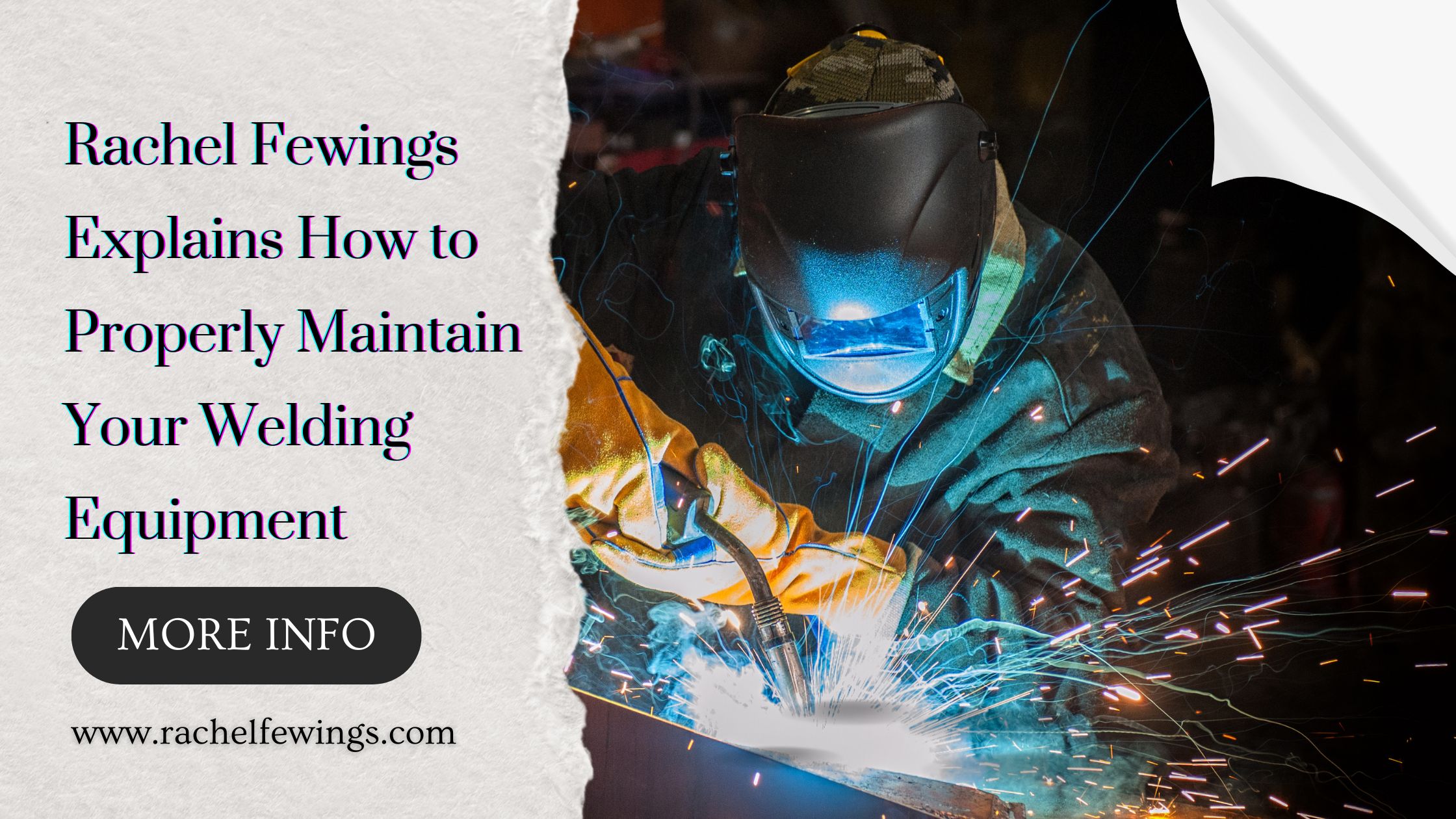
Maintaining your welding equipment is crucial for ensuring both safety and efficiency in your welding projects. In this comprehensive guide, welding expert Rachel Fewings shares essential tips and techniques to help you keep your gear in top condition. By following these practices, you can extend the life of your equipment and enhance your welding performance. Read on to discover the fundamental steps to proper welding equipment maintenance.
Regular Cleaning and Inspection
The first step in maintaining your welding equipment is to establish a routine for regular cleaning and inspection. Dust, debris, and welding spatter can accumulate on your equipment, affecting its performance. Ensure that you clean the nozzles, contacts, and other components frequently to prevent build-up that can cause malfunctions. Rachel Fewings emphasizes the importance of checking for any signs of wear or damage during your inspections, such as cracked cables or loose fittings, which could compromise safety and efficiency.
Proper Storage Practices
How you store your welding equipment plays a significant role in its longevity. Protect your gear from extreme temperatures, moisture, and dust by storing it in a clean, dry, and climate-controlled environment. She advises using protective covers and keeping welding machines and accessories off the ground to avoid accidental damage. Proper storage not only preserves the equipment but also ensures it is ready for use when needed.
Routine Maintenance of Welding Leads and Cables
Welding leads and cables are vital components of your welding setup, and their maintenance is crucial for optimal performance. Regularly inspect leads for any signs of fraying, cracking, or damage. Rachel Fewings recommends replacing damaged cables immediately to prevent electrical hazards and ensure consistent welding results. Properly coil and store lead to avoid kinks and twists that can cause wear over time.
Checking and Replacing Consumables
Consumables such as electrodes, nozzles, and contact tips require regular attention. These components can wear out or become contaminated with use, impacting the quality of your welds. She suggests keeping a stock of replacement consumables and checking them frequently to ensure they are in good condition. Replacing worn or damaged consumables promptly helps maintain the efficiency and quality of your welding work.
Servicing and Calibration
Periodic servicing and calibration of your welding equipment are essential to maintain its accuracy and performance. Rachel Fewings advises scheduling professional servicing for your welding machines to address any internal issues and ensure they are operating at peak efficiency. Calibration ensures that your equipment delivers the correct settings and outputs for your welding tasks, which is vital for achieving consistent and high-quality welds.